After several years spent developing a radio frequency identification system featuring embedded EPC ultrahigh-frequency (UHF) passive tags in its heavy truck, coach and bus tires, Michelin—one of the world’s largest tire producers—has now taken additional steps toward full deployment. To this end, the company has adopted testing technology to confirm that every tag is functioning properly before permanently embedding it into the sidewall of a tire being manufactured, and has released a hosted RFID-based solution for monitoring tire pressure.
Michelin’s tag supplier, Hana Microdisplay Technologies, verifies the functionality of all tags it supplies to the tire maker. Before shipping the tags to Michelin, Hana uses Voyantic‘s Tagsurance system to automatically test multiple tags loaded onto a tray. Michelin then checks each tag again via a Tagsurance manual test station prior to embedding it in a tire. The manual and automated test stations are the same, with the exception that the manual version is operated via a foot pedal that triggers the measurement, and emits an audible beep to indicate that a tag has performed satisfactorily.
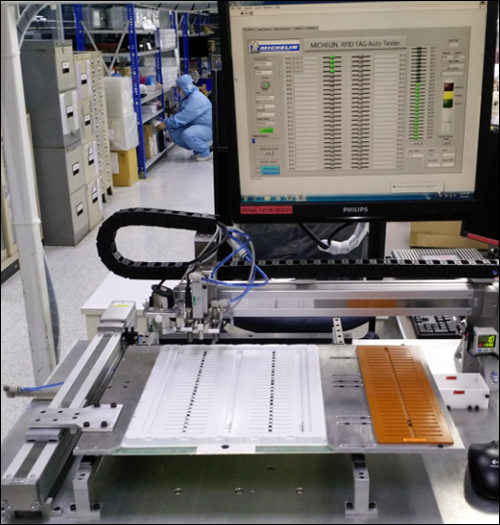
Furthering Michelin’s RFID goals, the company recently launched the Michelin Tire Care suite apps, which include its cloud-based iManage app and cloud-based service. With iManage, fleet operators can use an RFID reader to capture the unique ID number encoded to each tag at the same time that they read the pressure sensors built into the tires. That data is forwarded to the cloud-based server so that the fleet operator can track each tire’s history, as well as what its pressure readings have been, thereby making it possible to better determine when a tire has reached the end of its lifespan and should be replaced to ensure the vehicle’s safe operation.
During a tire’s manufacturing, Michelin embedded a tag directly into the rubber of the tire’s sidewall, though the tag can also be sold to customers in the form of a patch that attaches to a tire’s exterior.
Rubber and steel belts in the tire can affect RFID signals. Therefore, the tags must be over-tuned to compensate for the material’s detuning effect, thus making them better able to respond to interrogation with a strong transmission when embedded into tires. Michelin worked with Hana Microdisplay to develop an EPC UHF RFID tag specifically for this environment, one that could be incorporated into a tire and still function well. The tag is also being used by other tire manufacturers.
“Tags are embedded into tires before the curing process; once cured, it’s irreversible,” says Julien Destraves, Michelin’s RFID integration design engineer. And a working tag is important not only to Michelin, but to its customers. “A lack of read range due to bad tags will lead to a denial of service for our customers,” he explains. “That is why we want to ensure 100 percent of quality check.”
Testing tags in high volumes prior to manufacturing is not an easy task, however. The test needs to be conducted with a large quantity of tags very quickly, Destraves explains.
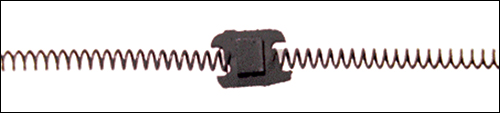
In 2012, Michelin began consulting with Voyantic to develop a testing system to be used with Hana RFID tags before they left its facility, and again at Michelin’s factory before they were placed into the tires, recalls Niina Aurén, Voyantic’s RFID testers product manager. “They wanted a reliable testing solution for high-speed testing while guaranteeing all the tags would work similarly,” she states.
Voyantic developed a solution that includes its Tagsurance tester—which employs the EPC Gen 2 protocol to measure the tag’s operational sensitivity—and the Snoop Pro coupling element, which functions as a near-field UHF reader antenna. The solution is designed to provide wide-band testing, from 800 to 1100 MHz, to cover the entire UHF band within which the tag could transmit. Tires are composed of rubber and steel plies that create a detuning effect, she says, so it’s that much more important for a tester to confirm that the entire RF band is working properly.
The testing was taken live in 2014 with a single manual testing station at Michelin, followed by another at the Hana manufacturing facility. There are now two testing stations in use by Hana, says John Erdmann, Hana Microdisplay Technologies’ president and CEO—one in Ohio and the other in Thailand. “We plan to add a second system in Ohio and one in another plant of ours in China,” he says.
At Hana, tags are placed on a tray and run through the Tagsurance tester. If the tester measures a tag’s sensitivity level as being too low, it displays that data, and staff members can remove that tag from the tray. The tags that perform correctly are then sent to Michelin, which conducts a second test before embedding a tag in a tire.
Although the optimal testing condition is in the far field, Aurén says, that is not possible in the production environment, in which so many tags are in the vicinity. Therefore, the tester includes the Snoop Pro coupling element—which, unlike a typical near-field antenna that inductively couples with the tag, is based on coupling specifically developed by Voyantic for testing UHF tags with dipole antennas. It takes the tester only 10 milliseconds to verify that a tag is functional on a wide frequency range, she adds, and 25 milliseconds to measure the tag’s exact sensitivity. A shielding plate on top of the Snoop Pro is intended to shield out the adjacent tags, so that only the tag of interest will be tested at any given time. In this solution, the shielding plate was custom-designed for use with the Michelin tags.
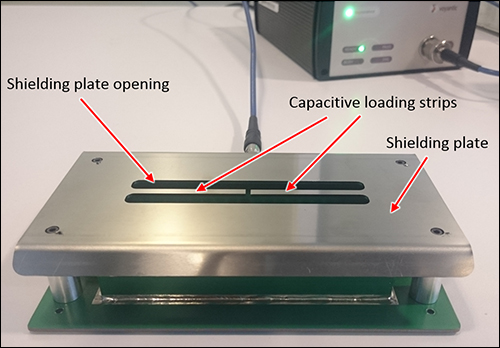
The Snoop Pro shielding plate is cut into two parts from the center, resulting in two separate capacitive loading strips that are electrically connected along the opening edges. This design lets the Snoop Pro coupling element mimic the environment the tire would generate.
“All of Michelin’s tire tags are tested with the system [at Hana],” Erdmann says. Although the testing system was developed for the Michelin tags, he adds, “it can be used for other tire tags, and we plan to explore that in the future.”
Michelin is now preparing full production of the RFID-enabled tires for use in large vehicles by the end of 2016, and is using the test stations on each tag. “We are counting in millions soon,” Destraves says.