- Laying the Groundwork in an Airplane Hangar
- Locating Hard-to-Reach Assets
- Combined Approach with Integrated Sensors
- Tackling Small Inefficiencies
In what was once a post-World War II airplane hangar on the campus of the California Polytechnic State University (Cal Poly), students are testing a simulated conveyor system equipped with a variety of sensors and on-board logic to identify objects, detect how they move and adjust its settings accordingly. In the airspace of the nearby Experimental Flight Range, drones are maneuvering around pre-calculated routes, reading RFID-tagged objects below. And in the Cal Poly Animal Sciences field, cattle are gaining trust with these overhead flying robotics that identify each bovine from a distance—which is progress, since cattle don’t typically care for unfamiliar, buzzing equipment hovering above them.
Overall, several dozen students are testing new innovations for real-world problems, all under the leadership of Cal Poly engineering professor Tali Freed. The work underway there is part of the university’s PolyGAIT Center for Global Automatic Identification Technologies, which Freed founded and directs. Unlike many university research facilities, PolyGAIT focuses on delivering solutions specifically to companies that have problems to solve.
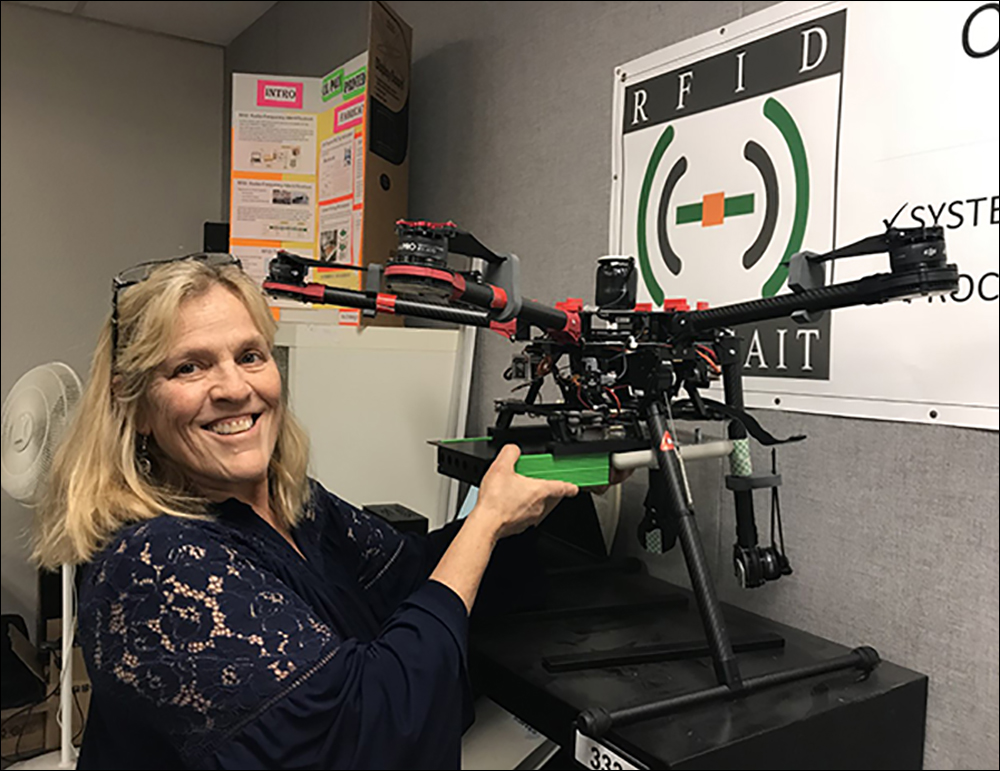
Tali Freed (Photo: Cal Poly)
For the past two decades, PolyGAIT has provided a team of student and faculty researchers who explore and innovate new ways in which to leverage the benefits of RFID technology. Since PolyGAIT opened its doors in 2003, Freed has never stopped being an evangelist for her students’ education and for the RFID industry. She believes both will make an impact on the world, now and in the future.
Freed graduated with a Ph.D. from Berkeley in 1995, with an interest in designing solutions for real-world problems, as well as the academic pursuits and education that universities provide. In the early days of her career, she says, “I always flip-flopped between academia and industry, and the only reason I haven’t been flipping in the last 21 years is that my university allows, and encourages, so much industry work.” In fact, the center she founded is among the few around the world that provides industry-ready RFID solutions through in-house development and testing. Freed likes the sense that work in the lab leads to real-world solutions.
These days, Freed is among the world’s foremost RFID researchers and innovators, while 19 years ago she was merely studying up on a then-new technology. She first heard about RFID and how it could be used in 2003, when Walmart issued its initial mandate for suppliers to tag products so that they could be automatically identified as they were received, stored or sold. In July of that year, Susan Opava, then the university’s dean of research, invited Cal Poly researchers to meet with two alumni and California-based Walmart suppliers, who sought help in deploying RFID to meet that mandate. Interested in learning more, she attended an MIT Auto-ID Lab meeting in January 2004.
There, Freed met Mark Roberti, RFID Journal’s founder and former editor, as well as Kevin Ashton and MIT professor Sanjay Sarma, the co-founders of the Auto-ID Center. (Ashton is often credited with coining the phrase “Internet of Things” in 1999, though the term was first used by Peter T. Lewis in 1985.) Freed refers to Ashton and Sarma as RFID prophets who, along with Roberti, Daniel Dobkin, Todd Humes, Stephen Lockhart, Daniel Engels, Bruce Roesner and others, have been dedicated to the technology’s growth. She launched PolyGAIT to provide a place where businesses could gain support in designing and testing new RFID systems.
Laying the Groundwork in an Airplane Hangar
The university provided Freed with the 1947 airplane hangar, which had originally been used by an active on-campus airport. The hangar had long since been unoccupied, and Freed recalls it as having been “an old building full of junk and spider webs,” which required full renovation as a test lab. She appreciates the synchronicity that with drones developed under its roof, the facility continues to support aircraft 70 years later.
During the early days of research, many RFID and automation experts visited the new lab and provided feedback, with design work by students already underway. The donation of conveyor systems by FloStor, along with design and installation by John Voris and George Ferrell, expanded the lab ‘s capabilities. An anechoic chamber and a Faraday cage were built by Freed’s colleague, Cal Poly electrical engineering professor Dean Arakaki.
One of the earliest projects was the design of what became the first UHF RFID-enabled medical cabinet, for use in at-home environments. The team tested off-the-shelf readers and tags to determine the best configuration for use on syringes and medicine bottles. They placed a reader into a wheeled cabinet structure, then linked personal identification information for the cabinet’s owner and began reading the tags of products that individual would be prescribed for self-administering. The result of that work is still commercially in use.
While the first device was a personal medical cabinet that patients could use at home to ensure they never confused medications, and that they kept to a prescribed treatment regiment, it evolved into the tracking of high-value injection drugs for cancer or HIV treatments in clinics. “That application was not an easy one at the time,” Freed recalls. “The landscape of existing tags was very minimal.”
The lab also patented a solution designed for managing reusable plastic containers (RPCs) so that the produce industry and its RPC provider could track high-value containers as products moved through the supply chain. Such containers are leased to producer sites, where they are loaded with lettuce, broccoli or other products, and are shipped to stores and placed on shelves until they are emptied. The containers are then shipped to the cleaning facility of the RPC owner before being returned to the producer to be reloaded with fresh produce.
By enabling the automated management of these containers, the technology reduces the cost of lost containers and allows companies to view and improve their supply chain efficiencies. PolyGAIT developed similar circular processes for reusable containers of other types, such as metal beer kegs and chemical totes.
Locating Hard-to-Reach Assets
Another solution rooted in PolyGAIT’s research is an asset-management system that detects office and technical equipment behind closed doors or in difficult-to-access areas. Traditionally, companies and organizations must employ workers to walk around a facility, scanning barcodes or visually reading the serial numbers of printers, computers, tools and other equipment. “We demonstrated that if you put RFID on those assets,” Freed says, “then you can scan them by walking through a hallway or room,” equipped with an RFID reader in a backpack or on a cart.
In that way, she explains, the reader will interrogate tags from that relative distance and users will see the assets without having to enter every office. The university put the solution to work in its own buildings, and the technology succeeded in locating missing items such as an industrial vacuum cleaner that had been stashed in a basement’s crawlspace. Physically finding that vacuum would have required bending under water and gas pipes and scrambling to the place where it was stored. Until the RFID system was deployed, the high-value equipment had been missing.
PolyGAIT has similarly helped companies both large and small develop and implement RFID systems for inventory management. The neighboring Pacific Gas and Electric (PG&E) Diablo Canyon nuclear power plant, located in Avila Beach, was the first such plant to tag its slow-moving inventory with UHF RFID, which allowed frequent labor-free inventory cycle counts.
For the past six years PolyGAIT has been taking RFID to the air with drones that capture tag reads in storage yards, vehicle lots and, most recently, cattle pastures. Freed published a paper defining the optimal routing of drones to ensure they can most efficiently cover an RFID read area, in order to minimize a drone’s time in the air and thus the battery drain. She also worked with a company that imported new vehicles and needed to track the ID numbers of thousands of them in the port. RFID would replace the time-consuming process of staff members physically going to each vehicle and scanning barcodes or examining vehicle identification numbers.
For one challenging use case, a vehicle company found that it could not properly read passive UHF RFID tags attached to vehicle windows, even within a relatively short distance. “We did some research and discovered that RFID tags can stop reading in sunlight,” Freed says, since a certain spectrum sunlight can affect chip performance. The problem was corrected by providing shading over the tags.
Combined Approach with Integrated Sensors
Going forward, Freed is interested in the many applications that require multiple technologies to provide solutions more complex than the inventory-management solutions of RFID’s earliest days. The smart conveyor system now in use at the lab is an example, as it combines UHF RFID tags on cardboard boxes and other types of containers that travel (and are recorded) on the moving belts and rollers, as well as a real-time location system that identifies high-value work-in-process moving through a manufacturing line.
The system also employs infrared sensors that identify when the objects pass on the conveyor and through portals. Programmable logic computers accelerate or slow the conveyor’s speed based on the presence of objects and RFID tag reads, while pressure and temperature sensors monitor its status.
Another new project in the works combines vision technology, vehicle monitoring sensors, GPS and RFID to detect whether large material-handling vehicles at ports or industrial sites are loaded, as well as whether or not they are in motion and where they are going. With multiple sensors on the equipment, and with RFID tags on goods transported by those vehicles, the system identifies each action being taken, along with what goods are being moved. With that level of visibility, Freed says, “You can analyze the processes’ efficiency and idle time rates, and how many employees you actually need.”
Tackling Small Inefficiencies
Every new project at PolyGAIT starts with the question of potential applications, Freed says, adding that she prefers applied research over studies conducted simply for research’s sake. As she explains, “It always starts with ‘What’s the return on investment?,’ ‘What’s the justification?’ or ‘What’s the inefficiency that we can resolve by using technology?'” Cattle are one focus at the center, which is building solutions around identifying individual animals as they move around pastures or through stock yards.
In the early days of the center’s tenure, the researchers built a solution around LF RFID tag reads on bulls. As the animals were sold at auction, their LF ear tags were individually read, then related data about each bull was displayed on a screen for buyers so they wouldn’t have to leaf through paperwork to learn details about the cattle’s size, health or history. More recently, drones were used to interrogate UHF RFID tags on cattle collars at a relative distance in pastures, and the tag reads were matched with the drone’s GPS location. The details of this project were presented this year at RFID Journal LIVE! 2022 by then-graduate student Sabrina Olson (see Drones on the Farm: Tracking Livestock with RFID Equipped UAVs).
Throughout its two decades of operation, the center has been staffed by hundreds of Cal Poly students from numerous disciplines. Typically, 25 to 30 students participate, including future engineers, artists or graphic communicators, biologists and chemists. “It’s fascinating work,” Freed states, “and it’s so multi-dimensional.” She adds that many of the center’s researchers have gone on to work at companies such as Raytheon, Lockheed Martin, Boeing, Cisco and Tesla, while several are pursuing RFID and other wireless technology development.
“I think that what I’ve always loved about RFID,” Freed says, “is that what I saw back in the beginning [in 2003], I’m still seeing now: a wide variety of applications, time and money saved, and the ease of use it can provide.” The technology now includes other frequencies, passive and active tags, Bluetooth Low Energy, LoRa and a variety of cellular-based systems. “RFID is part of huge set of technologies that keeps broadening and enabling productive industries.”
Key Takeaways:
- PolyGAIT’s Tali Freed oversees one of the world’s only research centers dedicated to helping companies solve problems with RFID.
- Freed’s commitment to improving industrial processes and reducing inefficiencies is matched by a dedication to the next generation of innovators.