Altrad Group, a France-based manufacturer of construction equipment, is using Bluetooth beacons to track the real-time movements of scaffolding products within a portion of its production facility and warehouse, with plans for a larger deployment. The solution, known as SINTRA, is provided by German technology startup Smartly Solutions. Altrad is attaching Bluetooth Low Energy (BLE) beacons to crates in which scaffolding products are stored and shipped, with beacon-reading smartphones mounted on walls and gates, and beacon-reading tablets or mobile phones in workers’ hands. A SINTRA app running on the mounted reading devices uses the received signal strength indicator (RSSI) to approximate each tag’s location within the facility in real time. Workers can then use their tablets, with a separate SINTRA app to locate and identify crates.
Altrad, which earns approximately $2.7 billion each year, manufactures 20,000 tons’ of scaffolding annually at its facility in Germany’s Lausitz region, making the company one of Europe’s largest scaffold producers. Manufacturing scaffold from steel tubes, nuts and bolts, and then tracking those items’ movements, is a monumental project, according to Ulrich Lawory, Altrad’s managing director.
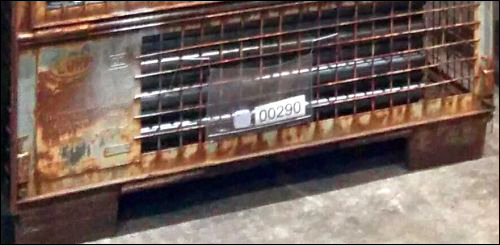
At its factory, workers typically cut the tubes to meet a particular scaffold’s size specifications, then bolt and weld them together. Next, the components are galvanized and packed for shipment to specific customers—building companies throughout Europe.
The finished product is transported in cages that amount to wire bulk crates. Typically, the company reports, the crates are the same size, and it can thus be difficult to distinguish one from another, even when they are loaded. For that reason, Altrad has traditionally attached a printed identifying label to the front of each crate during the loading process. Employees read those labels to differentiate one packed crate from another, in order to prevent any confusion regarding which crate contains which product. Going over these crates to locate the correct goods to fill an order could be time-consuming, Lawory explains, noting that such a task “was a waste of time. This had to be saved.”
The company began working with Smartly to create a solution, says Karsten Königstein, Smartly Solutions’ managing director.
Altrad had previously investigated using passive ultrahigh-frequency (UHF) RFID tags to track the tubes and other parts in the scaffolding, as well as the crates. However, Königstein says, RFID technology did not lend itself well to tracking products composed of metal. “At the end,” he adds, “it was too expensive and hard to implement with that amount of steel” located onsite. The cages are typically stacked one on top of another, in multiple stacks, and tags’ transmissions were blocked by the large amount of metal present. “RFID tags and wire bulk crates vanished from our radar,” he states.
Battery-powered BLE beacons, however, work well in such an environment.
First, Altrad places a SINTRA beacon tag into a plastic bag attached to the front of a cage filled with finished scaffolding for a specific customer. The unique ID number emitted by the beacon is linked with that customer’s order in the SINTRA cloud-based software. A worker can carry a Samsung Android-based tablet running the SINTRA app to receive beacon transmissions within the vicinity. In addition, about a dozen Samsung smartphones with Android operating systems (OS 5.1 and higher) are mounted on the walls covering one area within the warehouse—about 1,300 square meters (14,000 square feet) altogether. “We use this infrastructure,” Königstein explains, “as it is much cheaper and easier to maintain and is worldwide-certified.” These mounted readers run a separate SINTRA app that estimates the location of the beacon within the reader’s proximity, based on that beacon’s RSSI.
The Android-based reading devices serve several functions. They capture and determine the RSSI values of the beacons’ signal, compress the data and forward it to Smartly Solutions’ cloud-based SINTRA software. That software then identifies the beacon’s location, based on the RSSI and the reading devices’ known locations.
Altrad’s personnel use the data provided by the technology in several ways. Individuals on the warehouse or assembly floor can utilize the handheld tablet to confirm that a specific crate is the one they need to fulfill an order, by using the app to display what is in range of the phone and where is it located, as well as to view the entire floor’s RTLS data, based on information collected by the fixed beacon readers. The fixed readers (smartphones) and the handheld tablets communicate with the SINTRA software via the facility’s Wi-Fi network, though other deployments can use GSM-based cellular connections.
Workers can also use the app in Geiger counter mode on their tablet. In such a scenario, they can simply input the details of what they are looking for. The app will then identify the crate’s location based on its linked BLE ID number. Once it receives a transmission from that beacon, the app alerts the tablet user and displays approximately how far from the tablet that tagged cage is located, based on the RSSI.
Since the system was taken live, Altrad reports, it has saved labor time since employees can more easily locate the proper crates for shipping. However, Königstein says, the company has not yet calculated how much time is being saved.
With an automated tracking system, Altrad sought to monitor not only loaded crates but also raw materials, such as tubes, before and after they were cut or welded. In this way, workers could be assured that the right piece was being used in the making of scaffolding. The company is now investigating the best way to apply beacon tags to steel tubes and other items used for the scaffolding’s assembly.
In the long run, Altrad intends to deploy approximately 1,500 mounted beacons within its warehouse and another 1,000 in the assembly area.
Smartly Solutions was launched about 18 months ago to provide beacon-based technology for the manufacturing sector. Königstein, the company’s founder, worked at Bosch Software Innovations, where he focused on Internet of Things-related sales and business development. Prior to that, he says, he had been a top manager at a company known as BPM, which Bosch purchased.
The SINTRA solutions are built to be low-cost and operate on a subscription basis. Smartly’s customers—typically, manufacturers in consumer goods, food, pharmaceuticals, and oil and gas—pay a monthly fee to use the entire SINTRA solution, including software, tags (beacons), cloud storage and readers (Android-based smartphones and tablets). “We call the business model we offer ‘System as a Service,'” Königstein says. “Setup time is really in the area of a few hours,” and is intended to spare customers’ IT departments from getting involved in deployments.