Airline company Lufthansa is using an edge-based application to manage its preflight checks, leveraging software provided by Ditto. At its core, the wireless system enables workers to conduct preflight screenings with a tablet, thereby saving time employees previously spent manually doing so via paper and pen. Additionally, Ditto’s Intelligent Edge Platform enables the sharing of data between inspectors via Bluetooth Low Energy (BLE) or peer-to-peer Wi-Fi connectivity. The Intelligent Edge Platform database runs across edge devices and in the cloud.
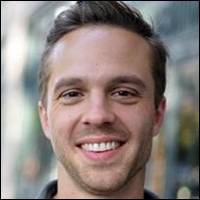
Adam Fish
In what is now a trial deployment across all aircraft and flights, users conduct inspections on Lufthansa’s new Crew App, which the airline built using Apple‘s SwiftUI framework. The solution was initially trialed on select parts of the Lufthansa fleet, and the app is now available for use by the crew on all Lufthansa passenger flights, according to a company spokesperson. Lufthansa is the second largest airline in Europe, with hubs in Frankfurt and Munich, and it operates worldwide and employs 105,290 people.
Prior to each flight, equipment must be checked for safety. Such work includes searching for dangerous or foreign objects, checking the functionality of emergency equipment, such as fire extinguishers and flashlights, and confirming the presence and functionality of other service equipment. Traditionally, preflight checks were conducted manually, via paper and pen. “The old process used paper checklists,” the spokesperson explains, “so those had to be printed, taken on board the aircraft, divided and handed out to individual crewmembers.”
Workers took the printed papers with them as they conducted a routine check of each piece of equipment. This work was performed independently, and crewmembers were unable to see what others were doing as the flight checks took place. “Now there is one digitally shared checklist,” the Lufthansa spokesperson says, “with full transparency on the progress between all crewmembers. That means workers can collaborate their efforts.”
How the System Works
With the Crew App, airline workers use their iPad or iPhone while proceeding to each item on the checklist. After opening the app, they select the updated task list for preflight checks for a specific aircraft and flight. Ditto’s software is embedded into the app. With a team of crewmembers working together, all can open the app and view the same data. As they go about their appointed tasks, they can check off each item or mark any discrepancies or issues requiring a remedy.
If there is a Wi-Fi connection available, that data can be managed on a server. In the case of in-plane work that is underway in or between airport terminals, however, there is often no network infrastructure. In such a scenario, if a device cannot connect to the cloud, it transitions to peer-to-peer communication between all local devices running the app, either via BLE or P2P Wi-Fi (also known as Wi-Fi Direct). Crew devices inside the aircraft form a mesh network, with preflight check data automatically updated across all devices in real time.
With Ditto’s technology, crewmembers can read and write data in a collaborative way, using any iPad or iPhone. The devices automatically create direct connections with nearby devices, but they can also hop data through other devices so that all stay in synch. “This enables applications to be resilient and operate with very low latency, providing significant operational benefit to a variety of industries,” says Adam Fish, Ditto’s CEO and cofounder.
No matter which crewmember is inputting data, Fish explains, that information will flow to every device within the connected mesh in real time. Ditto’s software can also provide automatic conflict resolution for crewmembers who may be editing data at the same time, ensuring that the information from any party is never lost.
Sharing Flight-Check Data in Real Time
If a problem is found during preflight checks, that information can be shared through the mesh network so employees can work in a more collaborative manner. For instance, if a piece of emergency equipment is discovered to be missing or inoperable, another team member can locate a replacement almost immediately. The airline is still reviewing the benefits the technology provides, the spokesperson says, adding, “There are no actual numbers yet, as we are still finetuning [the] app and contents.”
However, Lufthansa finds, benefits based on reduced material requirements are already proving to be significant. “Most importantly,” the spokesperson says, “we are saving literally tons of paper, and the checklist contents are much easier and faster to update.” The technology is designed to operate without the need for any scanning, such as tapping a phone against a piece of equipment’s BLE or RFID tag. “There is no scanning of tags implemented. The crews are manually or visually checking and using the app only for documentation and guidance.”
This new method of checking preflight inspections is part of an enterprise-wide effort Luftansa is currently undertaking to digitize its workflows. “Over time,” the company’s spokesperson predicts, “this new medium should also allow us to provide additional functionality and support via the app that is not possible otherwise.”
Using the Power of Edge Devices
Fish and Max Alexander, both developers, cofounded Ditto in 2018 to provide edge-based solutions where connectivity is not readily available. They built the Intelligent Edge Platform database to run across edge devices, Fish explains, as well as in the cloud. That enables resilient and low-latency synching for applications. “Its simple APIs are easy to use,” he states, “but internally it required a lot of novel innovation, which took several years to engineer.” Ditto released its first solution in 2021, and the company is now offering the technology to major businesses across the aviation, retail commerce, travel and defense sectors.
The goal, according to Fish, is to make connectivity seamless for remote workers. “Over the last 15 years,” he says, “significant investment has occurred in cloud computing, making it a standard in building software.” Conversely, applications are still built in the same way that they were even in the early days of the Internet, Fish recalls, meaning they had to interact with a central server. “This does not make a lot of sense when the average smartphone is the most powerful computing device owned by someone.” Thus, he adds, Ditto was designed to enable applications to take full advantage of the power of the smartphones and tables on which apps run.
“Lufthansa’s app is a great example of digitization and providing tools for frontline workers,” Fish states. While desk-based workers have access to many productivity and software applications to help them to do their job, he adds, frontline workers such as airline crews often still rely on manual or paper-based workflows. The Intelligent Edge Platform, he says, “provides infrastructure to bring software to these frontline industries where harsh communication conditions exist.”
Key Takeaways:
- Lufthansa’s crewmembers are using an Internet of Things solution allowing devices to create a mesh network for preflight check information.
- The airline is now enabling employees to pilot the technology across all its flights, sharing data seamlessly with anyone in the vicinity using the app, even without an Internet connection available.