Approximately 25 billion radio frequency identification (RFID) tags are produced worldwide each year for automatic and contactless identification, according to the RAIN RFID Alliance, and that trend is increasing. One challenge facing RFID manufacturers involves the die-attach process, during which a semiconductor chip and an antenna are connected. To get around that problem, Italian RFID tag and solutions provider LAB ID has partnered with German industrial adhesives company DELO.
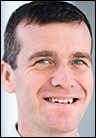
Stefano Farina
LAB ID offers customized ultrahigh-frequency (UHF) RFID and Near Field Communication (NFC) tags, as well as dual-frequency RFID tags that combine both technologies. The company also provides services like inlay design, software and hardware integration, and a tag-reading platform. Its UHF RFID tags are primarily used in logistics, supply chain management and warehouse management, while the NFC tags are utilized for brand protection, as well as for transmitting product information via smartphones. DELO, meanwhile, supplies customized adhesives and equipment for applications in such high-tech industries as automotive, optoelectronics and electronics.
According to Stefano Farina, DELO’s sales engineer for South Europe, the production of RFID tags needs to be optimized down to the smallest detail in order to achieve high throughput and meet the increasing demand. “The die-attach process, which includes connecting the chip and the antenna, is demanding and poses a number of challenges,” Farina states. One issue, he explains, is that chips are becoming increasingly smaller due to the ongoing trend toward miniaturization.
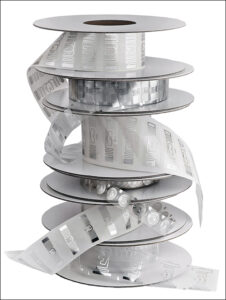
RFID tags, each consisting of a chip and an antenna.
“Today’s chips have an edge length of only 250 to 600 micrometers [0.01 to 0.02 inch] and a height of 75 to 90 micrometers [0.003 to 0.004 inch],” Farina says. “For comparison, a human hair is about 70 micrometers [0.0027 inch] thick. This leaves a tiny bonding area that still requires high strength to achieve the desired lifetime and aging resistance to things like the number of washing cycles. Good electrical contacting is also essential for reliable functioning of the tags and a large read range.”
The process design is essential as well, Farina notes. “All parameters, from chip type, substrate and dispensing system to adhesive and end-product requirements,” he says, “must be reproducibly matched to implement automated and efficient manufacturing processes.” To meet these challenges, LAB ID employs DELO’s conductive epoxy resins; the RFID manufacturer has been using the company’s MONOPOX AC products for more than ten years.
“They have been specially developed for die-attach applications and ensure maximum productivity,” Farina says. “The adhesives serve a dual function. They ensure immediate fixation of the chip on the antenna and provide electrical contact.” According to Farina, the adhesives incorporate metal particles that settle between the bump and the substrate. Following the curing process, he adds, they then conduct the current specifically in only a single direction.
Before the adhesives were used in production, Farina says, extensive functional testing was performed to ensure the RFID tags’ bonding quality and durability. The tests showed strong results in terms of read range and flexural strength, he reports, even after simulated aging. This included storage at +85 degrees Celsius (+185 degrees Fahrenheit) and 85 percent relative humidity, as well as temperature shock tests conducted from -40 degrees to +85 degrees Celsius (-40 degrees to +85 degrees Fahrenheit). Farina says the adhesives’ die shear strength on standard substrates like plastic and aluminum is 50 MPa.
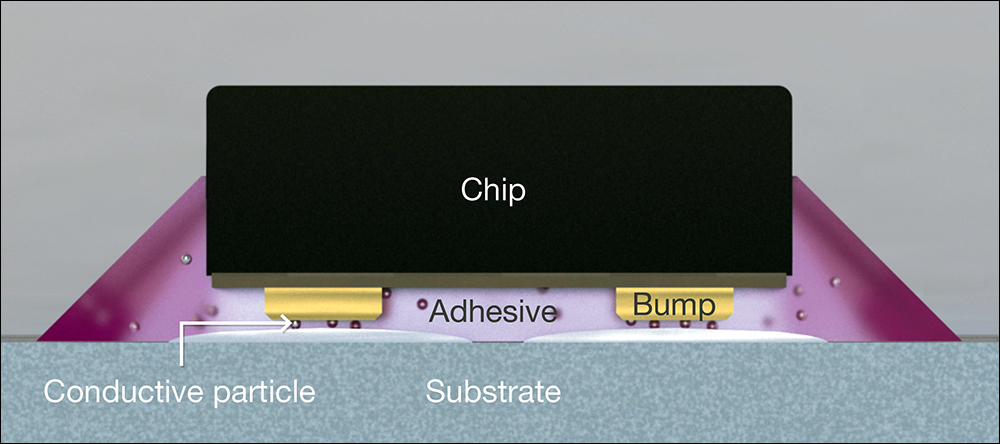
Electrically conductive DELO adhesives connect a substrate (antenna) and a chip and establish a reliable electrical contact.
LAB ID produces the tags in a fully automated die-attach process, with all steps taking place in direct succession on a single line. “The adhesive is first applied to the antenna pad without contact using a high-precision jet valve,” Farina explains. “A chip is then picked up from the wafer and placed on the adhesive drop. The good chemical-adhesion properties prevent the chip from slipping. Cameras check that it is correctly positioned and aligned so that an automatic adjustment can be triggered if necessary.”
During the next step, Farina says, curing takes place at 200 degrees Celsius (392 degrees Fahrenheit) by means of a thermode integrated in the process. “Within one to two seconds,” he reports, “the adhesive is completely cured and the electrical contact with the antenna is ensured. The finished RFID inlays can then be further processed or encoded accordingly.”
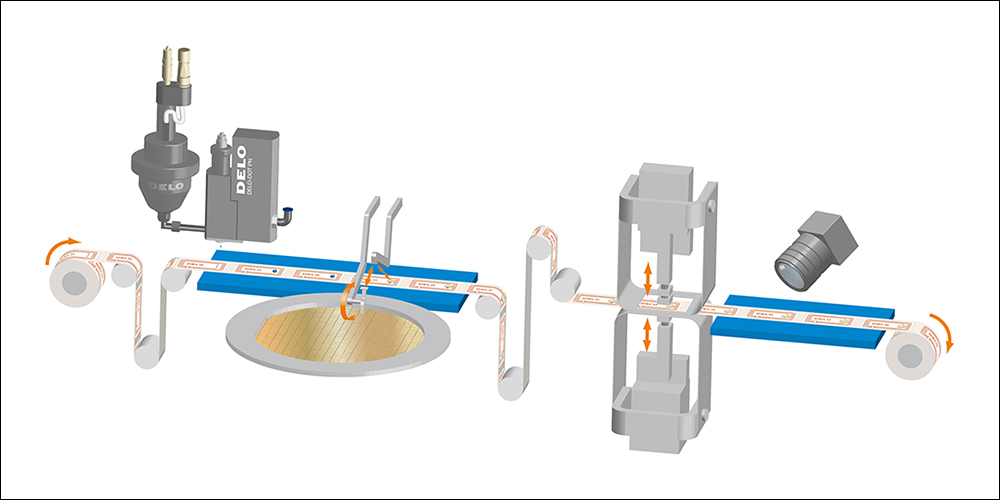
A typical die-attach process in RFID manufacturing: dispensing, gripping and placing of the semiconductor chip, thermode curing, and application control.
Because the adhesive and the process parameters are precisely tuned, Farina says, “production at LAB ID runs reliably and stably in cycles of a few seconds.” More than 400 million tags roll off its production lines annually, he notes—not only RFID tags containing plastic or aluminum, but also those made from paper and other renewable raw materials. “In this case, the DELO adhesives selected for use in the die-attach process cure at temperatures below 180 degrees Celsius” (356 degrees Fahrenheit).
The production of RFID tags is a complex process due to the high demand for micrometer-range precision. “In addition to special adhesives that ensure the chip and antenna are fixed in place, while at the same time providing electrical contact and meeting high functional requirements,” Farina states, “such complexity calls for processes designed to handle large production volumes and still maintain a high level of reliability. Close cooperation between RFID and adhesive manufacturers is essential to implement efficient manufacturing processes, and to support end users with high-performance RFID technology.”
Images provided by LAB ID and DELO.