Air France Industries KLM Engineering & Maintenance (AFI KLM E&M) is the maintenance, repair and overhaul (MRO) arm of Air France KLM, one of the top five airlines in the world. The MRO unit supports 1,500 airplanes operated by 150 airline customers, and its 300 facilities worldwide remove parts from those planes, repair or refurbish them, or provide scheduled maintenance. Tracking all of these parts posed a logistical challenge, but the company has deployed a radio frequency identification system to automate the process and cut costs.
Many parts must be shipped in special packaging typically consisting of durable boxes or cases lined with cushioning material. Tracking the packaging would enable KLM not only to monitor the parts within, but also to track packaging that was becoming lost, taking up necessary space in facilities and requiring too much time for workers to find when needed so that a part could be shipped to a customer.
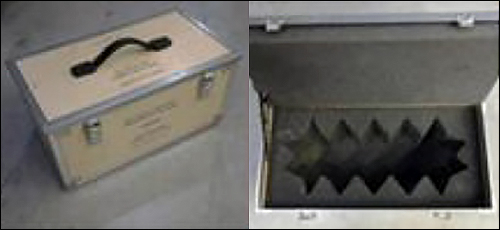
To address the problem, KLM worked with Nefab, a Sweden-based multinational packaging company, to develop a Web-based solution known as Aviation Packaging Information System (APIS) for managing the inbound and outbound flow of packaging between Nefab and KLM E&M. The solution uses fixed RFID readers in buildings and in trucks, as well as Nordic ID Morphic mobile ultrahigh-frequency (UHF) RFID handhelds—compliant with the ISO 18000-6C/EPC Gen 2 standard—for use in areas where no fixed reader has been installed, or as a backup if the fixed reader system goes down temporarily.
Fixed EPC Gen 2 UHF RFID readers from Intellifi were set up at the Nefab facility to capture data about packaging that the company ships to KLM. When Nefab ships packaging to KLM, which usually occurs twice weekly, RFID readers capture the serial numbers encoded to the tags and automatically send KLM an advance shipping notice containing information indicating which items will be delivered.
Several different models of Intellifi fixed readers were also set up in KLM’s engineering department, logistics center, warehouse and shop, where maintenance is performed. Omni-ID Power 50 battery-assisted passive (BAP) tags are used on parts packaging to ensure 100 percent read rates. When a package arrives, an Intellifi reader automatically captures its tag ID and updates the APIS software, which was developed by Dutch company ScoreTrace in association with Nefab and KLM.
Nefab affixes the tags—most of which are reusable—to the packaging and maintains a database of parts and the type of packaging each part requires, as well as the packaging’s location (prior to using RFID, Nefab’s and KLM’s workers had to spend a lot of time searching for packaging for a specific part). Now, readers set up throughout the areas where packaging is stored read tags and provide accurate inventory data on which packages are at specific locations, thereby making it easier to find what is needed.
The system is virtually 100 percent hands-free and can be paperless. So KLM E&M’s employees no longer need to manually record when packages arrive. The Web-based APIS solution allows KLM’s managers to log in and determine what packages were shipped, where they were delivered and when they were received. The system also tracks packaging that has been used, is no longer needed and has been sent back to Nefab, which puts some packages back into storage for eventual reuse, sends some for repairs and discards packaging that cannot be reused. The APIS solution also provides statistics regarding the number of cycles that a particular package has undergone.
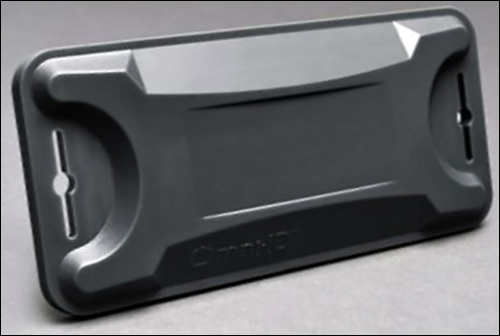
“We can track and trace the location of equipment and are in the process of preparing our products and process with RFID,” says Jos de Kleine, KLM Engineering & Maintenance’s logistic development manager for the Netherlands. “The system gives workers all the information included on the paperwork, which eventually gave us quicker processes and thus savings.”
The system reduced the cost of packaging by 50 percent, de Kleine reports, and delivered better insights into the other 50 percent of the costs. It enabled KLM to standardize its packaging and set up key performance indicators with suppliers so their performance can be measured.
KLM’s goal is to use the RFID system to reduce operational costs by at least 25 percent, decrease the number of parts held in inventory and lower throughput times. To accomplish that goal, the firm plans to streamline processes using the APIS solution. It will integrate the RFID data with its SAP and maintenance systems. In addition, KLM E&M is working with several airline customers to encourage them to install RFID readers, so that the system can track when packaging has arrived from KLM or been shipped back to the MRO provider.