The Jungheinrich Lift Truck Corp., a German manufacturer of industrial trucks and a provider of warehousing materials flow technology, has incorporated RFID technology into one of the lift trucks it sells in North America.
“Our goal [in using RFID technology] is to maximize the productivity of the truck, because that is what our customers depend on,” explains Greg Mason, Jungheinrich’s general manager of products and training. “They always ask for features that will enable them to move more goods, faster.”
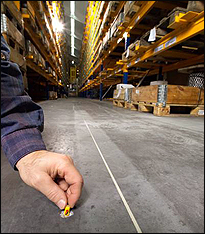
The company has modified the design of its existing EKX 513-515 electric man-up turret truck—a long, narrow lift truck made for navigating very narrow aisles within warehouses or distribution centers—to accommodate an RFID reader and antenna. As the truck moves through a facility, the reader collects data encoded to passive 64 kHz or 128 kHz RFID tags embedded in the floor, which Jungheinrich will embed and encode for its customers as part of the RFID offering. To control the truck’s operation, an on-board computer processes the data encoded to the tags.
The RFID system is also designed to inform the truck’s operating system of the vehicle’s location at any given time, as well as the direction in which it is traveling. It does this based on business logic that monitors the sequence in which the floor-embedded tags are read. At the entrance to each aisle, Jungheinrich embeds a primary tag to identify that aisle, with a secondary tag installed in an aisle’s floor, a short distance away from the primary tag.
If the interrogator reads the secondary tag after reading the primary one, this indicates to the operating system that the truck has entered the aisle. As the vehicle exits the aisle, its interrogator reads the code from the secondary tag before reading the primary tag marking the entrance. This code instructs the truck to slow to a stop and honk its horn, as per protocol upon reaching the end of an aisle.
The tags are encoded with additional instructions, as well. For example, some aisles in a warehouse might have rough, uneven floors requiring the turret truck to operate at less than maximum speed to ensure safe operation. Encoded to the RFID tags embedded in the floor at the aisles’ entrance points is a code representing a safe operating speed for that particular aisle. As the truck passes over the tag, its reader sends this code to the truck’s operating system, which commands the vehicle to slow to the speed deemed safe for that aisles. Or, if the truck is already traveling below that limit, the system prevents it from going above that speed until it has left the aisle.
Without such automated speed control, explains Mason, Jungheinrich’s customers are forced to set the truck’s settings to the speed deemed safe for the rough-floored aisles, and to keep the truck at that speed regardless of where in the facility it happens to be. By using RFID tags to enable variable operating speeds, he explains, customers can “maximize performance everywhere while limiting performance only where that is necessary.”
Other instructions that could be encoded to the tags at aisle entrances include height restrictions, above which a truck would not be permitted to lift loads, based on a permanent obstacle within the aisle, such as a low-hanging air-conditioning duct. If a customer were to later make changes to the warehouse in ways that might impact the directions the existing tags provide the truck—for example, if the rough floor within an aisle were repaired and the speed restriction lifted—Jungheinrich would re-encode the tags embedded in the floor to reflect those changes.
Jungheinrich has made this RFID-based platform a standard element of all EKX 513-515 trucks it sells in North America, and the first RFID-enabled trucks are currently shipping to Jungheinrich customers. The revamped truck is 30 percent more energy-efficient than the previous model, thanks to design advances that reclaim energy expended during operation, and to improvements in converting the battery’s DC power to AC. The truck can now operate for 13 hours before requiring a recharge, versus the 10 hours needed for the earlier model.