Iron Mountain Inc., a records and data storage and information management company, has announced that all boxes it provides to customers for the purpose of records storage will be RFID-tagged, beginning in early 2015. The firm has also launched its Inventory Governance Solution—a new platform of software and services that includes the use of RFID-based data, in order to ensure that customers meet regulatory auditing requirements, such as demonstrating the control of personal identifiable information (PII).
Iron Mountain stores and manages digital data and paper-based records for customers worldwide. It has been doing so for 63 years, helping customers—in vertical markets that include health care, banking and retail—to manage the storage of their documents, as well as their destruction when appropriate. The Fortune 1000 company serves 156,000 customers throughout 36 countries, says Amy Perras, Iron Mountain’s director of global solutions for records management.
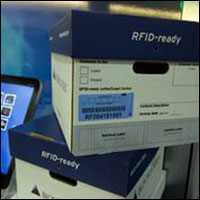
Many of the records stored at Iron Mountain’s sites must be very tightly controlled. Because personal information may be included, regulations require that the company’s clients be able to verify where those records are located at any given time, as well as if and when they are destroyed. Companies often conduct their own periodic audits in order to ensure that the records are where they should be. In some cases, regulatory bodies visit a customer’s own storage location, or one of Iron Mountain’s storage facilities, to ensure that the records are present and secure.
In late 2012, Iron Mountain met with RFID software and solutions company InSync, which ultimately provided an RFID-based solution that would allow it to use passive UHF RFID tags to track assets and records. After deploying this solution, RFID Mountain began providing RFID-based services to some of its customers at several of the company’s storage locations. In so doing, it tagged files, cartons and various types of assets.
Iron Mountain’s staff, or a customer’s auditors at the storage site, read the RFID tags at predetermined intervals, based on a customer’s needs. Iron Mountain decided that by providing such a service, it would be able to offer its customers electronic confirmation that the records are where they should be, and enable them to know if anything is not in compliance, such as a record being missing, according to Erik Johanson, Iron Mountain’s director of process engineering. The company hoped to provide sufficient data to customers that they could head off a compliance issue before it could be discovered during an audit.
Johanson says that the “RFID-ready” boxes that his company plans to introduce in 2015 can be used not only by Iron Mountain, but also by its customers at their own facilities. “The introduction of the industry-first RFID-ready box is just another way Iron Mountain can easily introduce our customers to RFID,” Johanson states, “and prepare them for immediate or future regulatory or auditing needs. This will help lay the foundation now for enabling our customers to audit their records in a cost-effective manner.”
“We wanted to help our customers quickly be able to respond to an audit,” Perras says, “or to even prevent or remediate [an inventory issue] so that when it comes time for an audit, the company can provide compliance.” The Inventory Governance Solution platform, in conjunction with RFID, she notes, “as a way to audit, is a great way to do that.”
Iron Mountain carried out initial testing of RFID technology approximately five years ago, prior to working with InSync. During the past few years since those early tests were conducted, the company has deployed millions of passive EPC Gen 2 ultrahigh-frequency (UHF) RFID labels (made with a variety of Alien Technology and Avery Dennison inlays selected for different types of storable assets). The labels are printed with bar-coded ID numbers, and are then attached to individual records, as well as to the cartons containing those documents for customers who wish to use the technology.
Iron Mountain expects to take RFID deployments live at additional storage centers as the company talks to customers and determines whether RFID is the right fit for their needs. To date, a center in London and multiple facilities throughout the United States are equipped with InSync RFID solutions consisting of RFID-enabled carts, as well as handhelds made by Motorola Solutions’ RFID division (now owned by Zebra Technologies). The RFID-enabled carts, designed and built by InSync, are made with fixed Impinj Speedway RFID readers and Laird antennas and onboard computers running InSync’s iApp software. The carts can capture tags’ ID numbers within several feet of the cart as it moves around the facility. This, the firm reports, provides Iron Mountain and its customer with 100 percent read-rate performance.
Once a tagged item is stored onsite, the unique ID numbers encoded to its tag and its carton’s tag are stored in Iron Mountain’s software, linked to details regarding the records and who owns them. The asset is then placed into storage. Inventory checks can be performed at periodic intervals, or as requested by customers. Because the facilities typically span several hundred thousand square feet, employees use the RFID-enabled cart, which they wheel down an aisle and read tags as they pass, collecting data about all items stored at that location. That information can then be provided to the customer.
Iron Mountain’s staff can also employ handhelds to locate a specific carton or record at a specific location, as needed.
The Inventory Governance Solution combines three services Iron Mountain previously offered separately: data validation (to ensure that key information about a box’s contents is classified according to customer policy before it is sent offsite to storage), data integrity (which refers to ensuring that new data matches legacy information already in storage) and auditing (which allows customers to choose how to audit their records, either by random statistical bar-code scanning or via RFID).
Because the company expects radio frequency identification technology to become more widely used in the future, it has opted to RFID-tag all storage cartons that it provides to its customers, beginning in 2015, whether a particular customer immediately requires it or not. In that way, if a customer opts to transition to RFID technology usage in the future, Iron Mountain will be able to respond quickly, since that customer will already be set up for immediate or future auditing needs.