Aerospace and defense company Lockheed Martin has launched a new wireless-sensor mesh-network system designed for detecting intrusion, monitoring secured areas or tracking structure stress, using small devices that contain active RFID tags and can incorporate energy-harvesting technology. For the detection of movement at a border crossing, Self-Powered Ad-hoc Network (SPAN) nodes may be equipped with ground-vibration or acoustic sensors, while for structural-integrity applications, stress sensors would be employed. According to Lockheed Martin, several undisclosed agencies within the U.S. government are currently testing the ability of unattended ground sensors to protect personnel stationed in war environments, and to assist with border surveillance. In addition, Lockheed Martin has signed a contract with a private firm to use the solution as a means of determining the amount of strain placed on a bridge or other structure, and thus its overall integrity and health.
Lockheed Martin is the not only company providing wireless-sensor mesh networks for government use for military purposes or border protection. Since 2008, aircraft and defense company Textron has been providing its battery-powered MicroObserver Unattended Ground Sensors, with built-in vibration sensors, to track the presence of intruders on foot, or in vehicles. More than 1,000 such sensors are presently in operation.
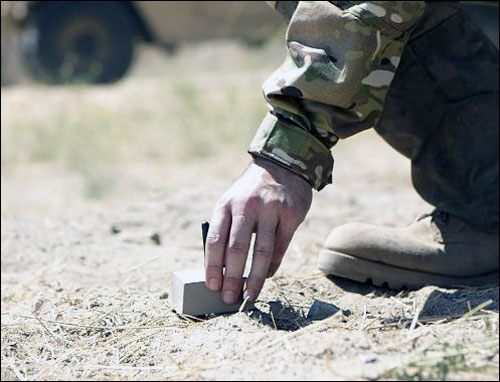
Both Lockheed Martin and Textron were willing to discuss the technology deployments only in general terms, though they report that agencies within the U.S. government are utilizing each company’ solutions for protection in war environments, as well as for border tracking. The two systems transmit data via proprietary air-interface protocols.
SPAN nodes contain built-in energy-harvesting technology specific to a particular application, says Jack Bright, Lockheed Martin’s program director for SPAN, as well as multiple sensors that also vary according to application, in order to detect the presence of a hazardous condition or an intruder. The SPAN node, he says, is designed to be small enough to fit into the palm of a person’s hand. “One of the challenges unattended surveillance sensors have had in the past is size,” Bright explains, because anything too large would be easy for interlopers to locate. Other end-user concerns addressed by the SPAN system, according to Macy W. Summers, Lockheed Martin’s VP of advanced development, include ease of use and deployment, as well as how the sensor nodes are powered. Since batteries have a limited operational life, they would require that users locate the nodes and replace the batteries periodically. Instead, Lockheed Martin developed a solution that would not require battery replacement.
To enable this ability, Summers says, the SPAN nodes operate with extremely low power, thereby making it possible to power them via energy-harvesting technology, such as solar panels. The type of energy-harvesting system used depends on the particular application for which the nodes are deployed. The low power consumption is achievable, in part, because the nodes do not transmit unless there is a sensor reading of concern.
Each node, once placed on or in the ground in a mesh arrangement, transmits relevant data, via signals in unlicensed RF bands, to the next node, and so on, until the information is ultimately forwarded to a handheld device or a gateway that sends data directly to a back-end system via a satellite, GPRS or Wi-Fi communications link.As the gateway collects data from the sensor nodes, algorithm software characterizes the event and determines whether information should be sent to a predetermined location, in order to permit operators to determine how to respond. The system could also activate a video camera, for example, to record the event.
Textron MicroObserver sensor nodes are buried in the ground, says Charles Stuewe, Textron’s director of unattended sensing solutions, with no part—including the antenna—visible above the surface. The nodes utilize battery power to operate a vibration sensor and transmit data to other sensor nodes, he says.
The MicroObserver solution has been commercially available since 2008, while two other products based on that technology have been recently released, but are not yet in use. Textron Defense Systems‘ Tactical Unattended Ground Sensor (T-UGS) and Urban Unattended Ground Sensor (U-UGS) were designed for the U.S. Army’s Brigade Combat Team Modernization (BCTM) program in 2010. The MicroObserver product was developed by Crane Wireless Monitoring Solutions before Textron Systems acquired that company’s sensor business in July 2010, to become part of Textron Defense Systems’ intelligence, surveillance and reconnaissance product offerings. T-UGS and U-UGS were developed as part of the Army’s Future Combat Systems program, later renamed BCTM. According to Henry Finneral, Textron’s VP of advanced weapons and sensors, the U.S. Army has delayed this program.
The T-UGS node is an outdoor intrusion-tracking sensor, while the U-UGS sensor is used indoors. Both types of nodes, Finneral says, were built for brigade combat teams, and could include acoustic sensors, as well as nuclear radiation, infrared emissions and ground-vibration sensors. However, he notes, the T-UGS and U-UGS nodes were never implemented as part of the BCTM program.
On the other hand, a vibration sensor based on MicroObserver technology—which, unlike the T-UGS node, was designed specifically for detecting vibrations only—continues to be used within the United States and Afghanistan. The transponders, planted underground, transmit a unique ID number via 2.4 GHz only in the event that a sensor detects an intruder. They send data up to several kilometers away, to another node or gateway, and that information is then forwarded to the Textron software managing the sensor data, which can issue an alert to a command center or other interested party.
One version of this “tactical node,” powered by an internal battery with a 30-day lifetime, is approximately the size of a bar of soap. A larger version, measuring about 8 inches by 4 inches, includes a battery that lasts for about two years. The former version would be more likely to be installed at a site on which it was required only temporarily. Typically, Stuewe says, Textron delivers its sensor systems to the military and provides limited training required by the systems. The military then deploys them as necessary for its various missions, he adds, noting that specific mission data is typically not public knowledge.