Researchers at Idaho-based Northwest Nazarene University (NNU) have created a prototype RFID-enabled robotic system that can carry out farming tasks. Josh Griffin and Duke Balanon, both engineering professors at NNU, are heading a program to develop what they call the IdaBot. The professors launched the project in 2015, with financial support provided by NNU, as well as more than $80,000 in funding from the Idaho State Department of Agriculture’s Specialty Crop Grant Program. The project’s team also includes two undergraduate students: Richie Grindstaff (a senior engineering student) and Lucas Pomeroy (a junior engineering student).
“The goal of the IdaBot project is to reduce labor costs for specialty crop growers, ease implementation of precision agriculture techniques in specialty crops, increase the productivity of specialty crop laborers and ease the labor shortage strain for specialty crop growers,” explains Griffin, citing grapes and onions as examples of specialty crops.
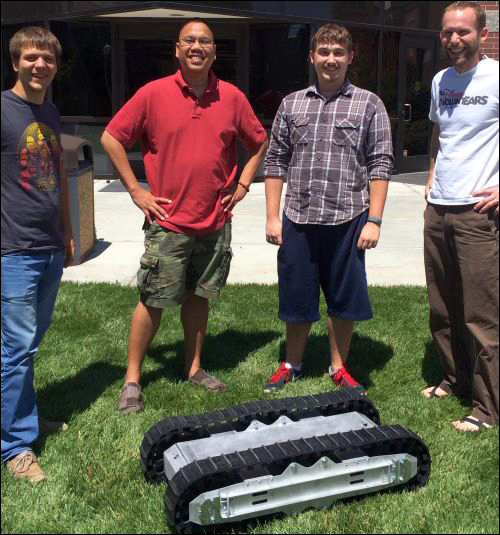
To construct the IdaBot’s motorized platform, the team used an HD2 Robotic development kit from Superdroid. The motorized unit measures 39 inches in length, 26 inches in width and 10 inches in height, weighs approximately 90 pounds, and has a maximum speed of 1.28 miles per hour or 113 feet per minute.
The team added a variety of sensors: GPS for rough localization of the robot, an inertial measurement unit (IMU) and sensor fusion chip to determine its orientation, motor encoders to measure how far the device has traveled, and a light detection and ranging (LIDAR) system to provide collision avoidance.
With tank-esque treads for mobility, the IdaBot could eventually perform a wide range of agricultural jobs. However, the developers’ first objective is to hitch the IdaBot to a sprayer and have the robot control the sprayer’s application of fertilizers, pesticides or other chemicals in vineyards located in Caldwell, Idaho. After sticker-like RFID tags have been affixed to each vine, the robot can be programmed to spray whatever configuration of vines the farmer wants. The IdaBot can then make its way through the vineyard, using the signal from the tags to determine what vine it is currently next to and whether or not it should be sprayed.
The team opted to use ultrahigh-frequency (UHF) Gen 2 RFID tags due to their low cost and profile, as well as the fact that they are passive and have a wide enough range. It is anticipated that the tags’ long range could potentially cause issues with undesired reads that will have to be rectified through the use of ranging algorithms. They chose an Impinj RS2000 reader development board, Griffin explains, because it was easy to integrate with the robot’s system hardware.
“I anticipate two challenges for the RFID system: (1) determining the range to the tag for the purpose of applying chemicals and (2) separating reads from tags that are located on an adjacent trellis row from those located on the row in which the robot is located,” Griffin says. “Eventually, we plan to test various ranging algorithms published in the research literature that use the amplitude and phase of the signal received from the tag. If we can determine the distance to the tag with resolution of a few feet, we will be able to both turn on the chemical sprayer at the right time and throw out stray reads from tags located on adjacent trellis rows.”
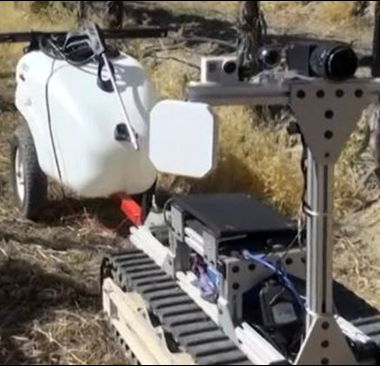
The robot could be used in tandem with a drone fitted with a multi-spectral camera; a computer program that determines how much spray a plant needs would process images from that camera. This, combined with the fact that the spraying mechanism allows for greater precision than what could be achieved with indiscriminate spraying, means that farmers would require smaller amounts of chemicals and that the spraying’s environmental footprint is lessened. A program that uses images to estimate the amount of fruit on a tree is also in the works. This would assist farmers in pricing their produce, and in determining how much shipping material they would need.
The team is field-testing the IdaBot at Williamson Orchards & Vineyards and Bitner Vineyards, located in Caldwell. Two UHF reader antennas have been mounted on the IdaBot for the tests, but they have not been integrated with the robot’s platform as of yet. The device also has a sprayer that does not yet contain the valves necessary to control the spray. The team hopes that by the end of 2017, the robot will be able to autonomously navigate a grape trellis row and apply chemicals to the correct vines. Assuming that the design process can be streamlined to allow for manufacturing in large quantities, Griffin estimates that a no-frills IdaBot would cost roughly the price of a pickup truck, making it a feasible investment for many farmers.
“At this point, we are focused on prototyping our robot for research purposes,” Griffin states. “We do not have a timeline for the commercialization of the IdaBot.”