Global coat and outerwear manufacturer Herman Kay Co. is carrying out a five-phase RFID deployment to track the garments that it produces and ships to customers. At the company’s distribution center in Douglas, Ga., workers are already using handheld RFID readers to identify which items have been picked, compare the collected garments with the quantities on a pick ticket, and catch any errors during the picking process, before products are packed into cartons.
Herman Kay Co., a third-generation, family-owned business, holds the license to manufacture and market coats and outerwear bearing a number of major brands, including BCBG, DVF, London Fog, Michael Kors and Anne Klein. It then sells the apparel to most large retailers, including Macy’s, JCPenney, Nordstrom, Lord & Taylor and Dillard’s. Herman Kay’s own manufacturing site in the Dominican Republic produces wool coats, while third-party manufacturers produce other outerwear, such as raincoats, according to Herman Kay’s designs and specifications.
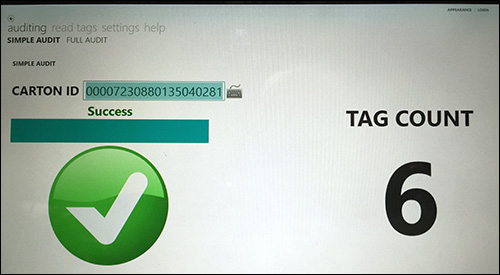
When garments arrive at Herman Kay’s distribution center, they are stored on hangers until they are picked, packed and shipped to customers according to their specific orders. Many of the styles look very similar, says Richard Haig, the company’s CIO and CTO, and checkers have thus needed to visually inspect the hangtags and labels, often twice, before the products were packed for shipping.
Approximately two years ago, Haig says, his firm began looking into RFID technology at the request of one of its customers—Macy’s—which is seeking to have all of its suppliers apply EPC ultrahigh-frequency (UHF) RFID tags to every item sent to its stores. “We do what the customer wants, to support them,” Haig states. However, Herman Kay wanted not only to apply the tags for Macy’s, but also to use the tags and gain some benefit from them in-house as well.
Working with RFID software solution provider SML Intelligent Inventory Solutions, Herman Kay Co. developed a five-phase plan that would begin with using RFID in its order-checking process, and then deploying readers at weigh stations after goods are packed. The other phases include the installation of RFID reader portals at the DC’s receiving and shipping docks, having all garments tagged at the factories and having those tags read as the garments leave the factories for the distribution center. All products destined for Macy’s and Hudson’s Bay Co. (HBC) stores, as well as a limited number of other retailers, are currently being tagged at the factory, while the plan is for all products to be tagged by the spring of 2016.
In August, Herman Kay Co. implemented phase one. Throughout the month, checkers at its DC began using handheld readers to identify which products had been picked for a particular shipment. The workers first use picking lists to collect products according to customers’ orders. The products—all on hangers throughout the supply chain—are then hung on overhead trollies.
Previously, checkers had to visually compare the coat labels against the picking order to ensure that no mistakes had been made. Now, the process is more automated. Each checker has a Technology Solutions (UK) Ltd. (TSL) Bluetooth EPC RFID reader paired with a tablet computer. Before checking goods picked for shipment, an employee accesses the picking list on the tablet that displays the items that should be present. The checker utilizes the TSL reader to capture the unique ID number encoded to each garment’s tag, and the device then forwards that data to the tablet via a Bluetooth connection. The tablet sends the information to a server running SML Intelligent Inventory Solutions’ Clarity software for the management of the RFID and shipment order data. The Clarity software displays a green check mark when all goods’ tags are read and match the stock-keeping units (SKUs) of the products on the picking list. In the event of a missing or incorrect SKU, the software displays a red highlight of the item in question, which checkers can view on their tablets.
Since this system was implemented several weeks ago, Haig says, it has caught multiple mistakes and prevented the wrong items from being packed, or orders from being filled with a product missing.
The next phase of the deployment involves an Alien Technology RFID reader with a Zebra Technologies antenna installed at its two weigh stations, one in each of the distribution center’s two buildings. As goods are packed in cartons, a GS1-128 bar-code label is attached to each box. The carton then travels down a conveyor to a worker, who scans its bar-code label and moves the box over the RFID reader antenna, which captures the RFID tag numbers of the goods inside the carton, thereby linking them and the box’s bar-code label with the shipping order. The worker then moves the box to a scale, which measures the weight and stores that data with the shipping order as well. As this is done, the Clarity software verifies the box’s contents against its “desired packing list.” If everything matches, the software displays a green thumbs-up. But if a discrepancy in the contents is discovered, the software issues a warning and the worker rescans the tags or returns the box to the packer to be opened and repacked.
The third phase, expected to take place in early 2016, will consist of installing RFID readers at the receiving stations of both buildings at the Georgia distribution center. The DC has six receiving doors at one building and three at the other, Haig says, but the company does not need to install a reader at each of the nine doors. Instead, a reader and antenna will be installed at several of the busier doors, and moveable readers will be set up temporarily at any of the other doors where goods are being received.
For the fourth phase, slated for summer 2016, readers will be installed at the DC’s outbound dock doors so that the company can automatically collect data regarding what is being loaded onto each truck, thereby creating a history of when goods are shipped, and also catching any errors, such as an incorrect carton being placed on the wrong truck.
The deployment’s final phase will involve the third-party manufacturers, as well as Herman Kay’s manufacturing site in the Dominican Republic. At each of these sites, 100 percent of garments will be RFID-tagged, and the tags will be interrogated as the garments are loaded onto trucks in containers departing the factory. This will not only help those factories identify any mistakes before they occur, but will also provide the distribution center with advance shipping notices. All five phases are expected to be completed by the end of next year, Haig says.
To make tagging easier for the manufacturing sites, Herman Kay Co. is working with two tag suppliers: SML Group and Avery Dennison. SML and Avery Dennison are printing integrated RFID hangtags for attachment to garments.
To date, Haig says, there have been several learning points for him, his team and staff members who use the technology. “We’ve had to dispel the belief that people can push a button and immediately know where everything is,” he states. “They have to understand the limitations and not be oversold on the immediate benefits, to think long-term and understand that this will evolve as business needs and strategies evolve and change.”
With each phase, the company will gather data that will provide greater visibility into the supply chain. “This has been a learning opportunity,” Haig says. “It may initially slow you down.” But when workers realize how accurate the resulting data is, he adds, enabling them to catch errors before shipments and verify their accuracy, they tend to be won over by the technology.
Haig will describe the deployment in detail at RFID Journal’s RFID in Retail and Apparel conference and exhibition, being held on Sept. 17 in New York City.