Gerolsteiner Brunnen, a manufacturer of bottled non-alcoholic drinks and mineral water, needed to comply with European Union (E.U.) regulations (EU 178/2002) regarding tracking food and beverages. Two years after implementing an RFID-based system, the German company says it has recouped approximately half its investment, and that the system has required little more than routine maintenance in the interim.
Each day, up to 20,000 pallets move through Gerolsteiner’s distribution center in the city of Gerolstein. In April 2005, the company began employing an RFID system that works differently than many similar applications. Instead of placing RFID tags on the pallets, it has embedded passive 136 kHz tags in the distribution center’s floor.
The project took Gerolsteiner and its integrator, SAP SI—a subsidiary of SAP—about a year to complete, because the company conducted extensive testing on hardware and frequencies. It needed to find a frequency that would enable the tags to work well while the forklifts carried bottles of liquid, and even if a crate of drinks were to spill on the floor.
Gerolsteiner decided to use 136 kHz transponders encased in small glass vials—the same transponders frequently utilized in animal-tracking applications. Measuring 3 centimeters (1.2 inches) long and 3.5 millimeters (0.14 inches) wide, the transponders are set into the ground and covered with a type of plaster. The tags are supplied by Texas Instruments and use a proprietary air-interface standard.
Each pallet is labeled with an EAN 128 bar code, with bar-code scanners installed on the forklift to scan bar codes after a pallet has been picked up. When a forklift driver picks up a pallet, the bar-code scanner identifies it. As the vehicle is driven over the floor tags, an interrogator mounted on the base of the forklift reads the tag. The computer system is updated regarding the specific pallet’s location by linking its bar-code number to the RFID tag’s ID. “I always know my inventory levels and where my batches can be found,” says Roland Keul, Gerolsteiner’s head of logistics.
Altogether, Gerolsteiner has installed 2,500 transponders in its DC’s floor. About five transponders are located along each row of warehouse shelves. The area in front of each truck loading space—a marked area on the ground, the size of a large truck—is equipped with 33 transponders, set 1 meter (3.3 feet) apart along the loading space. Gerolsteiner requires this setup so forklift drivers do not have to maneuver vehicles to a particular spot to read at least one of the RFID tags.
Upon moving into the loading area, a delivery truck occupies a specifically assigned parking space. The transponders are embedded in the floor near the marked parking area, covering the area along the side of the truck. Forklift drivers load trucks from the side, passing at least one transponder each time they place a load onto a truck. Each transponder within the same zone carries the same identification number.
A forklift driver receives a load order via a computer screen mounted on a particular delivery vehicle. The computer system notes the ID number of the truck, as well as the specific loading space to which the truck has been assigned, and combines this information with a serialized number used to identify that order. The forklift driver receives a message on his screen instructing him, for example, to put two pallets of apple spritzer and one pallet of mineral water on the truck.
The forklift operator drives to the appropriate warehouse shelves to retrieve the requested pallets. En route, the forklift’s interrogator reads the embedded tags, informing the system of the vehicle’s whereabouts. If a driver enters the wrong row, a warning message will appear on the screen.
The driver then takes a pallet down from the warehouse shelf and moves it to the loading area. Once the forklift’s bar-code scanner identifies the pallet and its interrogator reads the RFID tag in the ground at the dock door, that data is linked and sent via wireless LAN to Gerolsteiner’s SAP system. The system is updated as to the exact pallet being shipped—and to which customer—thus fulfilling E.U. requirements.
Before the system was implemented, Gerolsteiner depended solely on bar codes to track pallets, but it lacked the ability to identify which batches were shipped to particular customers. To do that, Gerolsteiner would have had to hire dozens of people to scan bar codes manually.
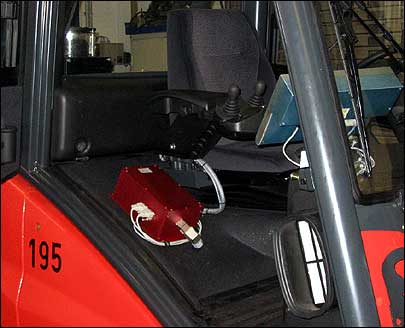
“We would have had €250,000 [$366,600] in salary expenses per year,” Keul says. He estimates that the company spent about €1 million ($1.47 million) on the project, including costs for software updates and non-RFID related hardware such as bar-code scanners. Keul expects the company to receive a full return on this investment in two years, after the system has run for a total of four years.
Antennas for the 35 forklift RFID interrogators were developed and built by German technology solutions company Indyon. Gerolsteiner reports no problems getting workers to adapt to the new technology. The company says it trained a few key people, who then showed their colleagues how to run the system.