In the past few years, General Electric has grown its software business by 20 percent annually, and by 2020, it plans to nearly triple its revenue, from $6 billion today to $15 billion, CEO Jeff Immelt said Tuesday at the company’s Minds + Machines conference, held in in San Francisco. (The industrial goliath generated $148 billion in revenue across its operations in 2014.) But Immelt was quick to point out that GE’s interest in strengthening its digital acumen is focused on improving its physical products, in order to boost the productivity of its own manufacturing efforts and those of its customers.
Immelt said GE is using its Predix software, a cloud-based platform purpose-built to enable the collection, processing and analysis of data related to industrial assets and processes, as the operating system to enable that productivity boost. He noted that connectivity enabled by what he calls the consumer Internet has “allowed information to flow, but it has not produced much value” for manufacturers. “So we want to turn connectivity into insights and insights into outcomes—that is the Industrial Internet,” he said. “The Industrial Internet is a fancy phrase, but what it really means is no unplanned downtime and asset optimization. We’re at the beginning days of an entirely new industry, and we believe the Industrial Internet could be twice the size of the consumer Internet.”
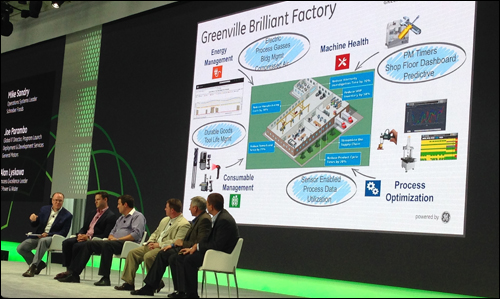
PTC AND GE WORKING TOGETHER
GE announced a strategic partnership with manufacturing software developer PTC at the conference. GE, both at its own factories and in its customer facilities, will offer PTC’s ThingWorx Application Enablement Platform as part of its software services (grouped under what GE calls its Brilliant Manufacturing Suite, which includes Predix). Through the collaboration, customers will be able to utilize PTC’s strength in product design and lifecycle management, as well as its dashboards that provide key performance indicators that track products from design to manufacturing, says Aaron Darcy, GE Commercial Software’s CMO, told IOT Journal, while also leveraging GE’s asset-management and analytics know-how.
The two firms have already been working together with existing customers, Darcy said, including Procter & Gamble, which uses PTC software for product design and Predix to automate the manufacturing. By using elements of the ThingWorx software, as well as Predix to manage connected assets, P&G is evaluating how it can create a “digital thread” that links products from conception to completion, across its operations.
GE is also integrating PTC’s software at its gas turbine manufacturing plant in Greenville, S.C.
DIGITAL POWER PLANT
Speaking of turbines, GE also announced Digital Power Plant, a software application built on Predix and aimed at its customers in the power-generation and electric utility sectors. The software creates a “digital twin” of an important asset, such as a gas turbine, explains Ganesh Bell, the chief digital officer for GE’s Power & Water division, and then uses the twin to model the performance and upcoming maintenance needs of that asset, based on data collected from sensors mounted on the physical asset.
“We think there are about 3,100 sensors in a typical power plant, tracking things such as heat, vibrations and stress” on machinery, Bell told IOT Journal. But the full potential of the data those sensors generate, he says, is not yet being utilized, and the same goes for the reams of maintenance records kept on assets such as turbines—but also compressors, actuators and other key machines—in power plants.
According to Bell, with the Digital Power Plant application, a plant can determine how well an asset is performing, based on actual output, and then manage assets across the facility to prioritize the use of its most efficient machines. GE thinks leveraging the application can help power plants avoid 75 percent of the mechanical failures that typically lead to downtime.
Energy generation and distribution firm Exelon is working with GE to pilot the Digital Power Plant software, Bell reported.
During a conference panel on asset management, however, Jeff Ingraham, Duke Energy‘s director of combustion turbine services, expressed some speculation about whether using sensors and software to monitor turbine performance—which the firm is already doing—will ever be able to completely eliminate downtime.
“We’ve been focused on bringing IoT to monitoring our system for quite some time,” Ingraham said. “We’ve focused on how units are operating, to provide insight to operators so they can identify issues as they’re happening, so we can halt operations and make a repair to avoid catastrophic events.”
But bringing a turbine offline to address a coming failure is also a very expensive event, Ingraham noted, and trying to utilize sensory data to perform more predictive maintenance on assets has not eliminated all failures for Duke Energy. Sometimes, he said, an asset is “operating fine one minute and failing the next.”
When later asked if he thinks GE’s Digital Power Plant application could get Duke to a point at which unexpected failures were a thing of the past, Ingraham told IOT Journal that he’ll be watching and evaluating whether the app can do a better job at predicting problems—sooner—than the root-cause analysis Duke already performs, based on sensory data and maintenance records.