Container Centralen (CC), a European horticultural logistics company, owns a fleet of more than 3.5 million metal, reusable carts that transport flowers and plants from harvest sites to retailers throughout the continent. The firm has approximately 20,000 customers—which, in turn, have about 80,000 customers of their own—and it is now offering a solution for anyone that uses its carts. The system is intended to prove the carts’ authenticity and count them via RFID.
The solution includes Container Centralen’s CC4Scanner app and Android-based handheld readers. The devices interrogate RFID tags attached to each cart’s base and provide visual confirmation that the tags and carts are not counterfeits. The technology was provided by Lyngsoe Systems and includes readers from Nordic ID and Newland.
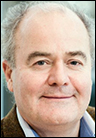
Barto Cleton
CC has employed UHF RFID technology for more than a decade to track the rolling carts—which it calls containers—as they travel to the company’s customer sites, comprising growers, wholesalers, auction houses and retailers. The company provides the carts as a logistics service; plants are stacked on the carts’ shelves, then the carts pass through the supply chain, directly to stores, where flowers and plants are displayed and sold. The empty carts are dismantled and stacked to be sent back for reuse in the supply chain, or to Container Centralen’s closest depot for maintenance or repair, before they return to the supply chain.
These rolling carts measure 120 centimeters by 45 centimeters (47.3 inches by 17.7 inches) in width and reach 2 meters (6.6 feet) in height. They are modular, include three components (the base, support poles and shelves) and are stackable when empty in order to limit space during transport. “That way, we transport less air,” explains Barto Cleton, Container Centralen’s sales director. By reading the tags attached to each cart base, using a handheld reader at the depot, CC maintains visibility into the status of its pool of assets, while ensuring that service fees are applied appropriately to its customers, based on the carts sent and received back.
Traditionally, the company used the collected RFID read data only internally. Now, however, it is offering a solution intended to make RFID tracking possible for its customers, and their customers as well. In that way, CC says, they can benefit from automated cart counts, as well as location or track-and-trace details, and share that information with the logistics company to enhance its understanding of the supply chain and improve the efficiency of transportation.
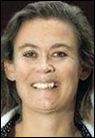
Anja van der Broek
One challenge the RFID system is addressing, according to Container Centralen, involves the growing incidences of counterfeit carts and tags being applied, to be passed off as CC products. Businesses were applying fraudulent tags that looked like CC’s RFID tags but contained no RFID chips. Additionally, says Anja van der Broek, Container Centralen’s European projects manager, CC replaces tags every five to eight years to ensure only authentic tags are used by paying customers, while, the development resulted in what she calls “a better-perforning tag.”
Therefore, the company introduced a new tag, the CC Tag 5, which it developed in partnership with Omni-ID. The tag features authentication and tamper-evidence capabilities, as well as improved performance, says Christian Meinhardt, Lyngsoe’s retail sales director. Container Centralenhas applied the UHF RFID tags to the bases of all its 3.5 million metal carts. Each tag is attached on a hook to a cart’s base. The CC Tag 5 is tamper-proof, the firm reports, so if someone tries to remove it frm a cart, the IC will break and it will no longer be functional.
To survive the rugged horticulture environment, the tags are made from the same plastic used to cover headlights in vehicles, Meinhardt reports. The tags can be authenticated without requiring an Internet connection; with the new tags and reader, a company could establish a connection once daily to download a device’s memory and thus manage inventory data on a server, while the authemication has already taken place. By ensuring each cart’s authenticity, the company says it can be sure it can accurately credit customers for the return of any carts they’d been using. “The tags help us to ensure the membership fees are matching the amount of containers in the system,” Cleton states.
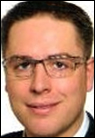
Christian Meinhardt
To check the authenticity of the containers, companies must access Container Centralen’s online store and purchase one or more handheld readers that suit their purposes. Then, after downloading the app on the reader, they can hold the device within range of the tagged carts being identified, and the tags will respond with their own uqnique ID number, along with a backscattered brand ID. If a tag has been tampered with, it will not respond, Meinhardt says, and if it is not authentic, the read data will be missing the brand authenticator. However, if the tag ID is read and authenticated, a CC logo will appear on the handheld screen, indicating the tag is authentic, in which case the cart will be identified and authenticated.
Not every party will adopt the technology, CC notes, but those that do will be able to capture data for their own purposes, saving labor based on manual counting, while reducing the risk of losing carts. If customers opt to share their own RFID tag-read data, Cleton says, Container Centralen can use the collected information to better analyze cart flow throughout Europe. “We estimate that carts rotate through the supply chain approximately seven times per annum,” he states.
With each rotation, the carts typically pass through the possession of five separate parties, including a grower, a transport company, an auction house, a wholesaler and a retailer. “The container passes from one party to another,” Cleton says, “and not every party scans,” though all carts are scanned once they arrive at the depot.
In the future, Container Centralen plans to use the new tags and readers internally, not only to confirm that carts are received and shipped at depots, but also to track those that are damagned as they move through the repair process. Down the line, shippers can link barcodes on plant pots or printed delivery notes to the carts on which they are stacked, thereby enabling shippers to track the products themselves. In the meantime, van der Broek says, Container Centralen has launched internal and customer-facing apps to ease the process of collecting data regarding the carts.
The customer app can provide easy scanning capability for CC’s customers, Cleton says, and the data can then be shared with CC’s or a customer’s database in order to help organize overall logistic flows. Only non-sensitive data is shared, such as logistics or track-and-trace information about the carts. With the new system, he reports, “We can provide better customer service. We know where containers are emptied,” and can thus collect and reroute them locally, which reduces the transportation of empty carts. “The objective is to reduce empty kilometers.”
For CC’s customers, the automated data is expected to help ensure they have carts available onsite when needed. That will relieve them of unnecessary labor, van der Broek explains, as well as the distraction of tracking the carts. “These companies are focusing on transporting flowers,” he says, “not managing containers.” In addition, the data provides CC with analysis so it can determine the movements of carts over time, and thereby better serve customers in future seasons, based on previous activity.
The new scanners were introduced in March 2021. “We have a lot of customers trying them out,” van der Broek says, adding, “We’ve had a lot of positive reactions.” CC uses an internal version of the application in its own depots to capture data about the carts beind received, which can be linked to the specific customer returning those carts, thus automating the crediting process.
According to Container Centralen, the demand for the reusable carts is increasing as they prove to be more sustainable than single-run, one-way packaging. The use and auotamtion of the carts’ data capture, Meinhardt says, is part of a worldwide trend toward service-based logistics. “We call that ‘product-as-a-service’,” Cleton states. In the future, CC expects that more customers and users will deploy fixed reader portals as RFID tag reads become more reliable on metal.