Finnish furniture manufacturer Martela is known for its innovative, modern designs. Now, the firm is employing radio frequency identification to innovate the way it manages its operations.
Martela, which is more than 65 years old, has significantly expanded its services over the past 10 years, says Johanna Kemppainen, the company’s marketing manager. It not only sells desks, chairs and other utilitarian furniture pieces to office buildings, schools, hotels and other institutional users, but also provides full life-cycle management of the goods it offers.
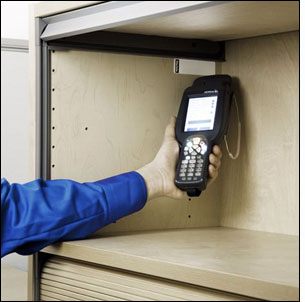
“The customer wants more full services,” Kemppainen explains. After receiving a furniture order, Martela delivers and installs the requested items at the customer’s facility—but the relationship does not end there. As an added service, the firm will return to that client’s site on an ongoing basis in order to inventory the furniture, which may be a requirement to comply with government auditing regulations, or simply be done so that the company can track its assets for internal purposes. And at the end of the furniture’s useful life—say, when it becomes broken or worn out, or goes out of style—Martela will remove the items and replace them.
While adding these services offered Martela an important competitive edge in the marketplace, Kemppainen says, it also placed a significant labor burden on the company. “We had noticed that inventory was a big task for us,” she states. The firm’s employees were using a fully manual system for counting furniture inventory at customer locations—not even bar codes were utilized. So when the business decided to look into a means of automating the process, it went straight to radio frequency identification. “RFID was seen as an easier way to complete the inventory,” she says.
To date, Martela has deployed its RFID-tracking system for three of its customers. Once a furniture order is placed and delivered to a client’s site, Martela’s workers attach an adhesive Confidex or UPM Raflatac passive EPC Gen 2 RFID tag to an inconspicuous spot on each product, and then use that tag to quickly identify every piece of furniture for the purpose of conducting inventory. While the manual furniture-counting process could take up to 10 minutes per average office room, the adoption of radio frequency identification has reduced the required time to just 10 seconds per room, says Ville Lukkari, the business development manager of Vilant, the RFID systems integrator that developed the solution for Martela.
Employees use NordicID‘s PL3000 ultrahigh-frequency (UHF) handheld RFID reader to encode a unique identification number to each tag. The number correlates with the furniture’s model name and other attributes, such as color, as well as the customer’s order information. Additionally, a separate tag, encoded and mounted onto a doorframe in each room, is used to note the location of every piece of furniture. This tag is read each time an inventory process is begun.
During early testing, Vilant tried using NordicID’s Cross Dipole handheld reader to encode the tags with the unique ID numbers. This caused problems, however, because the interrogator’s long read range—up to 4 meters (13 feet)—was too great, making it difficult to ensure that the correct ID was encoded to the proper tag, since many pieces are placed in close proximity to each other. To rectify this problem, Vilant purchased the PL3000 UHF reader, which has a shorter range—up to 1.6 meters (5 feet)—thus making it much easier to ensure that only the tag directly in front of the reader is encoded. To take inventory, Martela’s employees utilize the Cross Dipole handheld reader. Because of that model’s longer read range, employees are able to collect the tag IDs more efficiently, and from a greater distance, than if they used the PL3000 reader for counting inventory.
As a worker walks through a room collecting inventory data, the Cross Dipole reader emits a beep each time a tag is interrogated. In this way, the employee can simply enter a room and point the reader at each piece of furniture, wait for the beep, and then move on. The ID number of each tag read is also listed on the device’s display, and Vilant’s software ensures that duplicate reads are removed. The interrogator beeps only the first time it reads a tag. If it reads the same tag twice, the second event will not trigger the beep.
Once the employee completes an inventory count of a designated area (a particular room, for example), the handheld shows which items are new and which have been removed from the old inventory, or if the inventory still remains the same. Each time a room’s inventory is completed, Vilant’s RFID software updates Martela’s inventory applications with that information. Martela shares the inventory data with its customers, which can then utilize that data for such purposes as carrying out an audit or determining the location of a specific piece of furniture.
Martela launched the RFID-based inventory process early this year, Kemppainen says, and plans to expand it as an offering to all of its clients. “Customers are happy to get the statistics about what they have,” she states. And because the tags will allow the firm to quickly identify each piece of furniture when a customer wishes to replace it, the system provides internal benefits for the furniture maker, which will be able to then track the used pieces as they are either resold or sent out for dismantling and recycling.