Avery Dennison Smartrac has released a new RFID tag designed to be built into tires during manufacturing, and to then provide data to those with RFID readers in the supply chain and at retail stores throughout the tires’ lifetime, even when they are being recycled. The AD Maxdura tire tag can capture and manage data regarding each tire’s lifecycle, enabling a range of environmental and safety features, according to Lauri Hyytinen, the company’s market-development manager for the automotive sector. The passive UHF RFID tag measures 43 millimeters by 2 milllimeters (1.7 inches by 0.08 inch), and Avery Dennison claims it is among the smallest embedded tire tags on the market.
The company developed the tag to fill a perceived gap in the market, and it is expected to be made commercially available during the fourth quarter of this year. Several years ago, Hyytinen says, Avery Dennison met with an automotive original equipment manufacturer (OEM) to discuss challenges related to tire traceability. The OEM, which has asked to remain unnamed, had already been tracking auto components via RFID tags, though it had hoped to use the technology for monitoring tires as well. The company tested several existing UHF RFID tags on tires, Hyytinen says, but found that none met its exacting specifications.
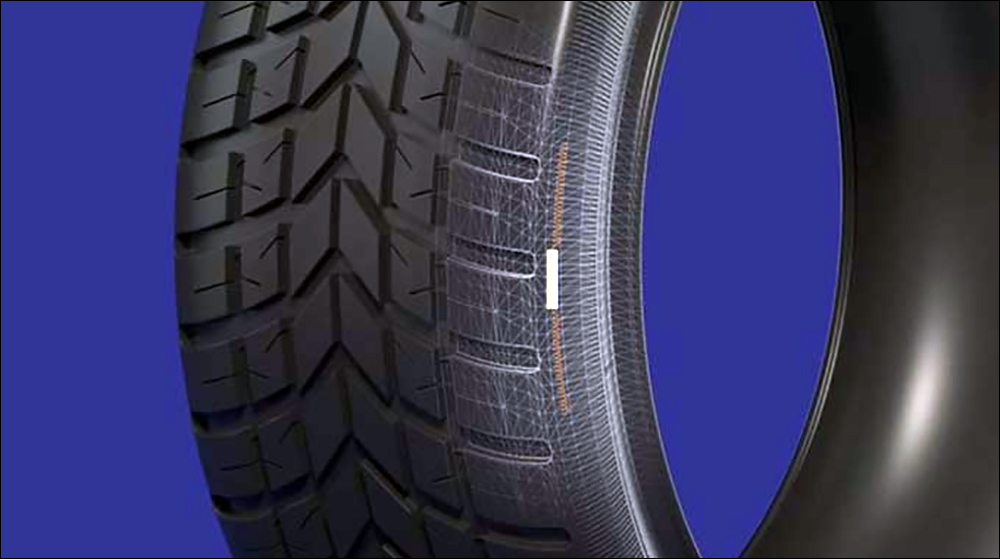
The AD Maxdura tag is embedded directly into tires during manufacture.
Therefore, the OEM sought a more reliable and stable RFID tire tag that could be embedded during the production process and survive for the duration of the tire’s life. “That meeting was a starting point for our development and defined targets for the AD Maxdura tire tag,” Hyytinen says. Avery Dennison has been making multiple versions of its Maxdura tags, a branded hard tag that varies in form factor and functionality, depending on the application for which it is used. “We have different transponders for different applications, such as industry, healthcare and logistics.”
Durability is a common feature across all Maxdura tags, he reports, and that was deemed paramount for the tire tag. However, Hyytinen says, performance posed a challenge. The tire industry has unique requirements it must meet when it comes to RFID tags. Chief among them is the need to build the application of tire tags (embedded in each tire wall) into an automated tire-production process. The reading of those tags must be carried out reliably, he explains, without disrupting the manufacturing process. That means the tags must be sensitive enough to be read in environments in which location and orientation cannot be controlled.
According to Hyytinen, an effective RFID tire tag must be read reliably from a variety of positions and in multiple environments. “Every tire model is unique,” he states. Factors such as the type of rubber, the metal structure of the wheel, the specific tag placement, the rim type and the distance at which tags are interrogated all influence the product. To that end, he says, Avery Dennison developed the tag so that it would work equally well on a passenger car, a sport utility vehicle or a truck.
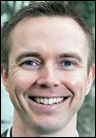
Lauri Hyytinen
The AD Maxdura tag was designed to receive RFID interrogation within the UHF band, in air, but the resonance frequency is specifically adapted to the rubber embedding. “The tag needs to support the wide frequency band to work reliably in a highly detuning tire environment,” Hyytinen says. It is built for a long life, he adds, since effective tire tags are first read on the production line, then are used potentially for years. “A tire has some 10 million mechanical events in its life, and the transponder must survive throughout them.” Since each tire is different, the embedding point varies depending on type and manufacturer.
The tag can provide a long read distance, the company reports, as well as a wide reading angle and stable performance over a wide frequency area. Several global tire manufacturers have tested the product to date, Hyytinen says, and it has offered reliable reads at a distance of up to 11 meters (36 feet). The tag is being applied to tires as part of the vulcanization process and it becomes fully connected within the layers of rubber as soon as the tire comes off the production line. There are two different chip types available, he says—one offering greater memory, the other with increased sensitivity for reading in challenging environments.
If used to its full potential, an RFID tag could enable a manufacturer to follow production, optimize logistics, and accurately track and trace tires. That means reading tags as tires move from a manufacturing plant through distribution centers and to the sites of automotive companies and stores. Automotive OEMs can identify tires reliably during car or truck production, Hyytinen says, and ensure that the correct tire is mounted at the proper location, while advanced driver-assistance systems could adapt to a tire’s specific characteristics. For instance, a vehicle might optimize the response to skidding on a curve, based on the type of tire being used.
RFID enables the tracking of tires on fleets of commercial vehicles or rental cars. A reader could capture information about a tire at the end of its lifespan; for example, recycling centers could read tags to determine the materials built into them. What’s more, the tags provide authentication. Consumers can benefit from higher safety levels, Hyytinen says, since RFID can prove that tagged tires are original brand products. The technology also provides enhanced quality compliance, as it ensures that four-wheel assemblies are compliant with customer sequence requirements.
The automotive industry is already familiar with RFID technology, which is being used for many manufacturing processes. “Over a hundred components are already marked with RFID in separated projects,” Hyytinen states, “and the industry is rapidly adopting RAIN RFID as the industry standard for all components.” Several auto assembly lines are already equipped with RFID reading gates to get a reliable bill of materials for each vehicle. “The more components are marked with RFID, the bigger the benefits are for the manufacturers.”
Approximately three billion tires are manufactured annually, and the tagging of those tires with RFID is becoming more ubiquitous. Michelin, for instance, began building RFID tags into its tires in 2015, and it plans to make RFID tags standard across all of its products by 2023. Already, 90 percent of the company’s truck tires come with RFID tags (see Michelin Ramps Up Tagging Program, Launches RFID-based App and Manufacturing: Michelin Uses RFID to Improve Performance).