For a decade, Austrian company Datatronic has offered an RFID-based fuel-management solution for transportation, construction and public service companies, with a reader installed on each vehicle’s fuel tank and an active tag on the nozzle of a gas station’s fuel pump. In the past year the company has turned that solution on its head by launching its BlueTank system, in which a passive UHF tag is attached to the vehicle and a reader is installed on the nozzle. By changing the hardware configuration, the company is able to offer the solution at a fraction of the cost of the predecessor technology, and the company claims users gain an ROI in about one month based on eliminating the loss of fuel.
Company fuel stations are frequently difficult to manage. Often there are no staff onsite to manage who is accessing diesel or gas, for what purposes, so that typically about 30 percent of the fuel used each month is simply unaccounted for, says Wolfgang Peiritsch, Datatronic’s president. Staff could pump fuel not only into the company vehicle, but personal vehicles as well, for example, and the company is unlikely to know about it. Some systems track fuel use with RFID-based ID badges, but such a system identifies only the driver, and not the vehicle that is being fueled. In addition, employing staff at the stations to oversee diesel and gas consumption can be expensive.
Datatronic’s initial solution—with an active RFID tag placed on the pump nozzle (usually one for dispensing diesel fuel) and a reader installed on each vehicle—was expensive, and could be complicated as well, since the reader required a power source from the vehicle.
“So we developed BlueTank,” Peiritsch says. With the BlueTank system, an EPC Gen 2 UHF passive RFID tag is attached to the vehicle, near its fuel filler pipe, and CAEN RFID Quark R1230CB reader is mounted onto the nozzle.
First, a user removes the nozzle from the fuel pump and a motion sensor detects that action and wakes up the reader. When the nozzle is placed in the vehicle’s fuel filler pipe, the reader captures the unique ID number on the RFID tag, which is typically affixed with an adhesive directly above the filler pipe’s opening. The reader is programmed to read only at close range, typically 1 to 30 centimeters, depending on the customer’s requirements.
Once the reader captures that ID number, it sends it to a controller programmer (a piece of hardware controlling the functionality of the fuel pump) installed onsite on the tank via a Bluetooth connection. The controller then uses BlueTank software to compare the ID number against a list of accepted ID numbers. If the number is recognized as authorized, the controller releases a switch to enable the user to begin fueling. The programmer then measures how much fuel has been pumped and stores that data.
The data can be sent to BlueTank software on the user’s back-end server as well, via a GSM or GPRS cellular connection or via an Ethernet cable.
If the company also wishes to track who is fueling which vehicle, another CAEN RFID Quark R1230CB reader is mounted near the fuel station’s pump and wired to the programmer. In that case, a driver would present his or her RFID-enabled badge to the reader, which would verify that employee ID number on the RFID tag and store that data in the system.
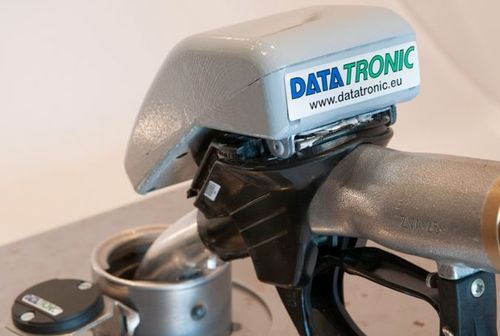
Peiritsch estimates that the system would cost users about $10 per tagged vehicle (the Blue Tank solution uses RFID tags from a variety of vendors, depending on the size and shape of the vehicles being tagged), and $1,000 for each nozzle’s reader. The software and installation would cost another $5,000. Comparing that cost against the cost of lost fuel, he says, the ROI would be a mere month if the company had about 100 vehicles. (Peiritsch says that on average, about 35,000 liters—about 9,250 gallons—of fuel are used on a company vehicle each year, and 30 percent of that fuel may be unaccounted for.)
In addition, the software provides historical data such as which vehicles are being fueled, how often, and how much fuel they require.
Construction and bus companies are using this system, which was launched commercially one year ago, says Peiritsch, in places like Europe, Israel, United Arab Emirates and Colombia. The system not only protects companies again the misuse of fuel, but also makes the process of fueling more efficient than a manual registration in which users have to press keypads or manually record the fuel they are using.
The rising cost of fuel is making the solution more popular among fleet managers, according to Peiritsch, who says until recently, companies have simply accepted the loss of fuel rather than upset staff with tighter regulation of fueling. Today, he says “because the prices of diesel and gasoline are so high, BlueTank has become a very desirable system to avoid fuel misuse.” In addition, he adds, more companies are offering 24-hour unmanned fueling stations, which would gain most from the technology.