The Northgate Link Extension light-rail tunnel, currently under construction in Seattle, includes RFID sensors built into some concrete liners to detect strain and help monitor each liner’s integrity during construction, and potentially in the future, when the tunnel is in use. L-7 Services, an engineering firm based in Golden, Colo., designed the concrete liners, which are being installed in a parallel pair of 3.5-mile-long tunnels that will accommodate Sound Transit‘s rail service between the University of Washington, in Seattle, and Northgate, north of the city. The sensors, readers and software to manage the collected read data were provided by another Colorado company, Phase IV Engineering.
The Sound Transit tunnel is a three-year project that began in 2013. The challenge that L-7 faced in its design work was to ensure that the concrete liners would not lose structural integrity when any of them were cut to accommodate passageways connecting the two tunnels. For safety purposes, the tunnels require 23 such passageways, spaced about 800 feet apart, so that if a problem occurs involving an underground train in one tunnel, passengers could leave by walking to the nearest passageway and crossing over to the other tunnel.
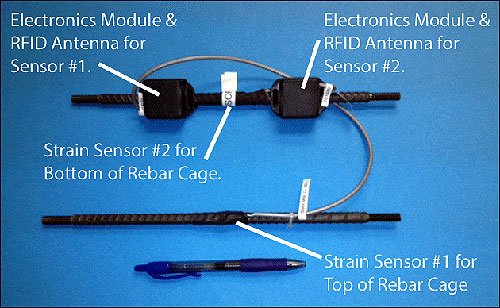
L-7 Services’ principal engineer, Kurt Braun, sought a way to verify that the liners’ integrity was not compromised when openings were cut for the passageways. Therefore, he spoke with the general contractor, Jay Dee Contractors, which agreed that L-7 should look into options for embedding strain sensors in the concrete.
Braun found that wired sensors are bulky and difficult to install, so he began investigating wireless sensors and contacted Phase IV Engineering, which sells RFID-based strain sensors for use in bridge infrastructure. Phase IV developed the battery-assisted passive (BAP) SensTag RFID strain sensor for the Northgate Link project, along with a mobile reader with a telescoping antenna to interrogate the tags embedded in the liners. The firm also provides software to manage the sensor data so that Jay Dee and L-7 can be alerted in the event that the strain level exceeds an acceptable threshold. Sound Transit could also use the sensors in the future to intermittently monitor the tunnels’ strain over time.
The sensor devices, manufactured by Phase IV and measuring approximately 1.5 inches by 1.5 inches by 0.5 inch, are each encased in a hard plastic cover. They come with a built-in strain sensor, a passive ultrahigh-frequency (UHF) RFID tag and a battery so that the tag can automatically measure the strain level without being interrogated by an RFID reader, and then save that data in the tag’s memory. The battery has a lifetime of about 10 years, according to Scott Dalgleish, Phase IV Engineering’s CEO.
“We’re proud that the battery can last 10 years,” Dalgleish adds, though he adds that “Tunnels have a hundred-year life.” As such, Phase IV wanted the tags to be of value potentially for the duration of the tunnel’s lifetime.
Therefore, the tags are designed to operate whether the battery is working or not, so that the sensor will continue functioning long after the battery has expired. Initially, the device serves as a data-logger, storing periodic measurements. When an individual brings a reader to interrogate the tag, it captures not only the tag ID number and current sensor reading, but also the history of other measurements taken in the past. The sensors are being programmed to carry out three readings daily, though the frequency of measurements can be changed at any time by means of a reader.
Once the battery dies, the tag can still operate in passive mode. Thus, in order to read the tag after its battery has stopped functioning, a user would need to bring the reader antenna within about 12 inches of the tagged concrete’s surface. The tag would then use the power of the device’s RF signal to take a strain measurement and send that to the reader. From that point on, it would no longer provide data-logging capability.
However, Braun says, his initial interest in the technology was to ensure that the passages cut into the tunnel did not compromise the liners.
First, the tags are being read before they are incorporated into a section of liner, to capture a base strain measurement in open air. The tag’s ID and initial strain measurement are stored in the Phase IV software. Two sensors are then welded to pieces of steel that are added to the liner’s existing rebar cage, which is cast into the concrete. The sensors are interrogated again after the concrete is poured and the tunnel segment is removed from the forms.
Construction workers take another reading once the tunnel segments are delivered onsite and the concrete has been fully cured. Six curved liner sections are assembled to a ring encircling the tunnel, with thousands of such rings making up each of the two tunnels. The sensor, positioned about 1 inch beneath the surface of the concrete, can be read again after that section of liner is installed in the tunnel, and finally, after the passages are cut, in order to determine whether there are significant changes in the strain measurements. If such changes are discovered, Braun says, additional engineering will be required to ensure that there is sufficient support for the lining around the passages.
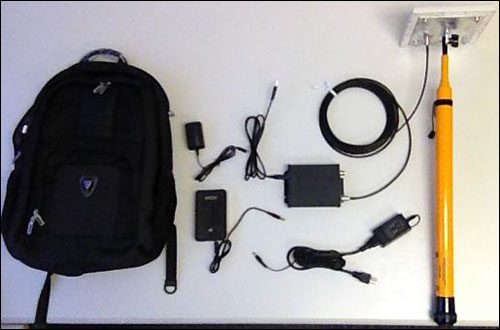
To read the tags, Phase IV designed a backpack with a ThingMagic RFID reader built in and a telescoping wand antenna that ensures users can reach the tags, which may be in a difficult-to-access location, such as at the top of the tunnel ceiling. After the lining panels are cured, Braun explains, a mark is painted at the tag’s location to alert those equipped with RFID readers to where they need to point their reader antennas.
Phase IV provided software for capturing, interpreting and storing the sensor measurements. That software resides as a standalone solution on a PC in a backpack that is kept at the construction site. The company also provided firmware that is loaded onto the reader so that the strain results can be displayed on the device’s screen, as well as forwarded to the back-end software via a USB connection.
Once construction is complete and Sound Transit commences rail operation, Dalgleish says, the transit company’s own staff will be able to use the tags to monitor the tunnel’s structural soundness, based on the amount of strain to individual liner sections.
RFID sensors are not built into every section of concrete liner, Braun notes, but rather in 38 segment rings where the passages are being cut, with two sensors embedded in three of the six sections within each of those rings (totaling about 200 sensors). The six sensors in each ring provide some redundancy, he explains, in case any of the sensors are damaged during the installation process, and also serve as a means to check the sensors’ accuracy.
The liner sections are still in the process of being molded and then installed, Braun reports, and no passages have yet been cut. The tags can be read well through the concrete, he adds, as long as the reader is located about a foot from the surface of the panel where the tag was embedded. Workers are painting a mark above each embedded tag.
Phase IV Engineering will display the SensTag strain sensor at this year’s RFID Journal LIVE! conference and exhibition, being held next week in San Diego, Calif. The company is also an RFID Journal Awards finalist, in the category of Best New Product (see Finalists Unveiled for Ninth Annual RFID Journal Awards).