Construction and agriculture equipment manufacturer Doosan Bobcat plans to expand the Internet of Things (IoT)-based solution it launched at its Czech Republic facility to bring digital intelligence to the manufacturing of its loaders, excavators and other machines. The system also enables the capturing and management of data related to product maintenance and returns. The expansion will involve rolling the solution out to more of its global sites, the company reports.
With the FactoryTalk Innovation Suite from Rockwell Automation, the company has integrated data from all of the machines and equipment in the plant, as well as the products built on those machines, using IoT technology. It can provide real-time data to management regarding work-in-progress (WIP), as well as share assembly directions or instructions and enable two-way communications with workers.
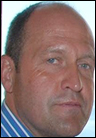
MESA International’s Uwe Küppers
The firm reports that since the system was taken live last year, it has increased efficiency by adjusting scheduling and equipment use according to analytics from the collected data. The solution also enables the company to view the tasks accomplished by workers, and to engage with those employees to ensure optimal scheduling and use of the workforce. With the technology in place, Doosan Bobcat says it can achieve higher-quality work with less need for rework.
Doosan Bobcat deployed the integrated solution last year at its site near Prague to better manage its operational and business processes, says Uwe Küppers, the chairman of MESA International‘s EMEA division and the consultant services manager at Rockwell Automation. MESA is a manufacturing enterprise solution organization that focuses on smart manufacturing. The company met with Rockwell Automation approximately two years ago, Küppers recalls, then began developing a roadmap which led to the solution.
Traditionally, Doosan Bobcat had captured multiple independent data silos from its equipment, while information about activities on the assembly floor was typically collected manually and input into Microsoft Excel files. Assembly operators used printed instructions for each project, or in some cases a computer screen displayed the assembly requirements. However, it was difficult to make operational decisions based on the paper-based data, and manually collecting information on the assembly floor caused extra labor time and expenses for operators and management.
FactoryTalk InnovtionSuite was deployed as a software suite to collect and manage data from hundreds of devices via IoT wireless or wired transmissions, thereby helping the company to view information in an integrated fashion, and to analyze it or use it for augmented reality. Work processes at the plant begin with uncut steel, which moves through such processes as cutting, bending, welding and painting, as a piece of construction equipment is manufactured according to a particular order. Doosan Bobcat needed a solution that could track this WIP, as well as monitor parts used in assembly.
On an analytical basis, the company sought to understand what was happening on its floor, and to thereby make better decisions for work scheduling and trigger the delivery of materials and supplies or other functions. In addition, Doosan Bobcat wanted to share data with operators on the floor in real time. “That was an important part of our digital journey,” Küppers says, to ensure operators understood what was happening, identify when they might run behind, and gain other performance- and quality-related information.
With the FactoryTalk solution in place, data from equipment used during the assembly process is received either through wired or wireless connections, and the software manages that information. “We put an IoT layer on top of all machines,” Küppers explains. As each machine transmits details about its operation, such as when it is running and its conditions, those details are all routed to the FactoryTalk solution, which puts the data into context.
The system tracks each product as it moves through every step, and parts can be tracked based on barcodes or QR codes. Once a code is scanned, it can be associated with a specific order in the FactoryTalk software. As a product moves through the next production step, operators scan its QR code, thereby accessing data on a tablet device at each assembly site in order to view details about the product and its parts, including what assembly has already been completed, what needs to be done next and how. Operators can input their own information to indicate what they do with the product before it moves to the next station.
The software collects operator ID numbers linked with their experience and skillsets. In that way, the system knows who performed which procedure and with what equipment, as well as how long that took. The operators are invited to provide their own input related to the work being done, when they find a problem with an item and how they like the station where they work. They can suggest modifications and redirect a product to the repair station while inputting data regarding the reason for doing so.
The software displays not only content for operators regarding tasks that need to be done, but also the expected timeline so that they can view how much time remains for a given task. Management can view how often a specific product has met its timeline, as well as how it has under- or over-performed in meeting that requirement, so that the schedule can be adjusted accordingly. “That allows management to analyze and have a deep dive into what is happening,” Küppers states.
Once the product is completed, it is sent to a retailer or customer, and the software stores the data for that product. Thus, if a machine requires maintenance, users can access information by, for instance, scanning a QR code on the product to view spare parts, or capture diagnostic information, all provided on a dashboard. However, Doosan Bobcat is not yet offering this feature. If the product is returned to the company for maintenance, its software contains data about the product and can capture such analytics as what failures take place, the production conditions and parts used when it was built, and whether or not there is a correlation.
The system can capture onsite assembly equipment management data, such as how well machines operate, how often they are maintained and if several pieces of equipment operating in close proximity to one another might affect the quality of operations. By capturing analytics regarding the use of the assembly stations, as well as how quickly and efficiently products are made, the company can improve its overall efficiency. While managers would traditionally need to walk around the plant speaking with operators to understand what was happening, Küppers says, they now have a view into those details.
According to Küppers, the solution ensures health and safety by making sure only qualified workers conduct any task, and that they are not distracted with paperwork. This, he says, increases asset utilization since the company better understands how its assembly equipment is being used and can thus reschedule in order to improve that efficiency.
Doosan Bobcat has opted not to comment for this story. However, it reported to Rockwell Automation that it felt the technology served as a journey for continuous improvement. “Once we started, we [began] looking into more areas,” said Hiram J. Sosa, Doosan Bobcat’s EMEA senior automation manager, at a Rockwell event. “One of the things that we focus on is providing the best quality to our customers and also internally as well. So we put in place some of the data captures for the equipment to increase the quality assurance.”
The system offers other features not yet in use by Doosan Bobcat, such as daily updates for management. The firm could utilize the software to receive notifications at the beginning of each shift, indicating machine performance, product quality, and production and maintenance updates for that day. Managers can view who is working in any given area, along with the current status of each product assembly.
The software can reside on either a local server or in the cloud. For Doosan Bobcat, the solution is being employed partly onsite and partly in the cloud. Rockwell Automation has also deployed the technology with several companies in Europe and the United States, which it has not named.