South Korean chemical manufacturer Exax is planning a move into the RFID market, following its recent investment in antenna- and label-making equipment.
Earlier this year, Exax announced it had purchased a dedicated rotary-screen printing line from Stork Prints that would make it the first company to produce both high-frequency (HF) and ultrahigh-frequency (UHF) antennas in a single pass. This month, the firm purchased complete RFID factory equipment from German technology group Mühlbauer for its Cheonan plant, in order to enable the production of RFID inlays, label conversion and label insertion.
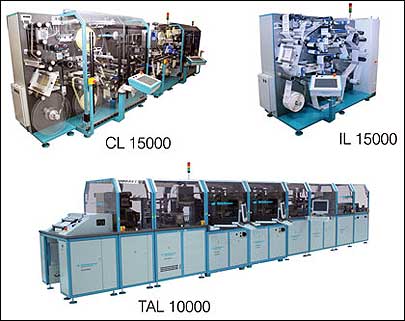
Exax intends to use the new equipment to produce RFID antennas, dry inlays, wet (adhesive-backed) inlays, tags and tickets. The company opted to expand into RFID label production after developing a conductive silver solvent-based ink for antenna printing, according to Seong Kon Chi, VP of European marketing. Later this year, it plans to begin producing RFID labels, tickets and tags to capitalize on the growing worldwide demand for RFID.
“Chemical manufacturing is our core competency,” Kon Chi says, “but we realized there was significant demand for HF and UHF antennae, and our unique conductive ink gives us an advantage in the production. So we approached both Stork Prints and Mühlbauer to provide a complete system for RFID label production. We will focus primarily on the production of HF and UHF antennae. When the printing equipment is installed in September, we expect to print up to 800,000 antennae an hour.”
Exax, Kon Chi says, plans to ramp up production quickly, but to first focus on the domestic and Asia Pacific market before expanding into the European and American markets. The firm, he adds, intends to target big business with its RFID antennas and labels. “We will approach card manufacturers first,” he says, “because we believe the antenna we provide, with its conductive ink, is unique. But we believe the number of applications for HF and UHF will continue to widen in coming years. We will look at HF and UHF tags for ticket manufacturers and air baggage tags, which we believe there will be large demand for in the future.”
UHF tags could also be employed for long-distance applications, which require a read range of 5 to 10 meters (16 to 33 feet), such as track-and-trace labels in the distribution supply chain and road-toll systems. HF labels, meanwhile, could be utilized for chip-based touch-in and touch-out public transport and ID cards.
According to Kon Chi, Exax expects the printing equipment from Stork Prints to go online in September. It purchased three of the company’s PD-IV rotary screen integration units, which are fully integrated rotary screen printing stacks with drying capabilities. The first printing position applies the conductive ink, either as a thick layer of HF coil or as a thinner UHF dipole antenna. The second and third positions are used exclusively for laying down the two other components of the HF antenna—a dielectric insulator with a UV-curable ink, followed by a conductive jumper.
Exax chose rotary screen printing, Kon Chi says, because it is capable of achieving high definition and laying down heavy ink layers needed in HF antenna circuits. The challenge, he notes, was to devise a system that afforded the conductive ink a lengthy dwell time, at a relatively fast production speed. This was achieved by devising an accumulator drying system, whereby the web passes up and down the dryer several times.
Additionally, Exax purchased Mühlbauer’s TAL 10,000 automatic inlay-production machine, which can manufacture up to 11,000 RFID inlays per hour in a reel-to-reel process by applying adhesive onto the antenna bond pads, then placing the chip, curing the complete package and testing each inlay. For converting the RFID inlays into smart labels, smart tickets and RFID baggage tags, the company purchased Mühlbauer’s CL 15000 converting machine, designed to automatically produce adhesive RFID inlays and labels and RFID paper tickets, and its IL 15000 inlay-insertion system, which inserts RFID inlays into finished self-adhesive labels.
This equipment, Kon Chi says, will enable Exax to be flexible in meeting its customers’ demands by producing antennas, dry inlays, wet inlays, tags or tickets. Initial production capacity will be 100 million inlays and tags per year, he claims, and Exax is currently in discussion with chip manufacturers to determine which chips it will utilize in the production of HF and UHF inlays and tags. The chemical manufacturer expects to produce up to 1 billion antennas annually.