Radio frequency identification is part of the set of cutting-edge technologies and innovations adopted by Sinctronics, which calls itself a Green IT Innovation Center. Located in Sorocaba, a city in the Brazilian state of São Paulo, Sinctronics operates what it says is Brazil’s first integrated ecosystem for electronic products, processing 100 tons of discarded equipment per month, and generating raw material for the manufacture of new products, thereby reducing the extraction of natural resources, saving energy and reducing carbon emissions.
“This is the world’s first plant for recycling discarded electronic products that was built next to a new manufacturing plant, which is fully prepared to receive the materials and parts produced by the recycling plant,” says Carlos Ohde, the general manager of Sinctronics, whose facilities are located just a few hundred meters away from a plant operated by Flextronics, which manufactures printers for HP Brasil. “It is the only one in the world with these characteristics, as far as we know.”
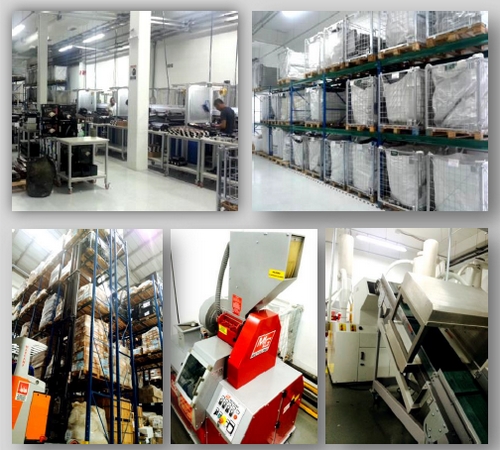
When a discarded printer, for example, arrives at Sinctronics, the first step is to identify the machine’s make and model in order to determine the materials from which it is made. This initial step can be accomplished via RFID—assuming the printer has been tagged—or manually, which requires more time and increases recycling costs.
“At the time of identification of waste products, the use of RFID by the manufacturer is a great facilitator,” explains Mileide Alves Cubo, Sinctronics’ production manager, making it “possible to determine, without testing, the types of plastic, metals and other materials for recycling. The HP printers, all made with RFID tags, allow us to more easily identify their materials, as they are registered on our systems.”
Trucks filled with discarded electronic products arrive at Sinctronics’ receiving docks. As workers unload the vehicles, they use RFID interrogators, whenever possible, to automatically identify those goods and store them along with their peers, in order to facilitate the subsequent disassembly and separation of their components. Those without RFID tags, on the other hand, will need to be manually identified.
RFID also makes the disassembly process more efficient, since it allows Sinctronics to know the exact composition of a discarded product’s components before they are removed.
The Sinctronics plant removes and separates all types of materials from the discarded products, including plastics and metals, but reprocesses only plastics. “Metallic materials such as iron, steel and copper are sent to companies specializing in recycling these elements,” Ohde says, “such as Gerdau.”
The plant completely recovers all of the various plastics, which can later be formed into new parts, for example, respecting all parameters established by its customers regarding resistance, flexibility and color. An analytical laboratory installed onsite carries out the necessary tests to qualify the recovered raw materials.
“We manage the collection and reverse logistics,” Ohde states, “keeping track of the entire process, ensuring proper disposal and meeting all government requirements.” By the end of 2015, he adds, the electronics sector must comply with Brazil’s National Solid Waste Policy.
Sinctronics’ electronics recycling process turns waste into raw materials and parts for new products, thereby saving energy and other natural resources, including reducing carbon emissions. In addition, the company’s research and development efforts foster innovation, enable projects, and provide training and experimentation in sustainable IT. “We have thus formed an integrated ecosystem of sustainable solutions for the electronics industry in Brazil,” Ohde says. “The integration of educational and social practices at Sinctronics promotes improvement opportunities and professional growth through specialization in the green and sustainability technology market, creating opportunities for social inclusion and expansion of value-added services in the industry and society, and generating better quality of life for all.”
Due to the limited number of places known by consumers for disposing of computer equipment and ink cartridges, Sinctronics has received more than a thousand queries per month regarding the possibility of receiving devices from different parts of the country. “Today,” Ohde reports, “we are processing 100 tons of discarded products monthly, but we can multiply this potential by six.”