Bell Helicopter, a civil and military aircraft manufacturer, has brought its on-time delivery (OTD) of parts used during the production of helicopters to 99.81 percent since installing a radio frequency identification system to track the internal movements of parts and containers in 2011. The company, a division of Textron, is employing an RFID solution designed by OATSystems.
Since the deployment, Bell Helicopter estimates that it recouped its investment within a year, according to Aaron Druyvesteyn, the firm’s manager of logistics, who described the solution to an audience at RFID Journal LIVE! 2012, held last week in Orlando, Fla. The financial return comes from reducing the amount of labor hours employees spend searching for missing parts, as well as performing associated stock adjustments. In addition, the high traceability of parts has dramatically reduced the potential for disruptions to the production schedule. In fact, Druyvesteyn said, the company has already saved approximately $300,000, surpassing its total RFID system investment of $250,000.
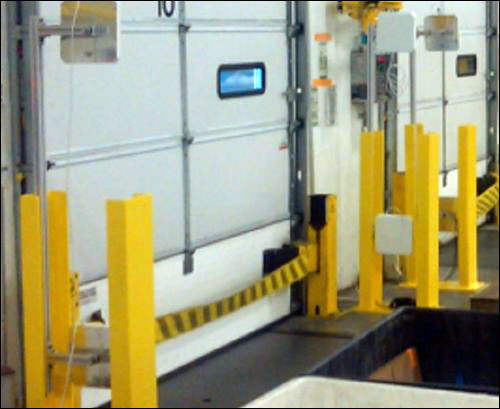
Bell Helicopter distributes parts from its central distribution center (CDC), located in Fort Worth, Texas, to its eight component and final assembly locations, in Fort Worth, as well as in Amarillo, Texas, and Mirabel, Quebec. The company’s goal was to better manage the movement of aircraft parts, and to reduce the incidences of lost or misrouted shipments.
Not only can missing parts or shipment errors cause delays and require additional labor, but the aircraft industry’s stringent regulations can make the misrouting of components more expensive than they would be in most industries. For example, if a part erroneously leaves a warehouse for production, and then needs to be returned, strict guidelines require that it be inspected again before it can be restocked at the CDC—another cause of additional labor hours and delay.
Initially, Bell Helicopter decided to deploy a new warehouse-management system (WMS) to replace its legacy paper-ticket order-picking system. As a result, the company developed an in-house WMS known as the Pick Ticket Management System (PTMS), which was launched in July 2010. “This helped us know when an order was picked,” Druyvesteyn said, “but we still had no way of knowing the date and time orders left the warehouse and reached their final destination.” So in June 2011, Bell integrated an RFID solution into the PTMS, using Alien Technology EPC Gen 2 passive ultrahigh-frequency (UHF) RFID tags that the CDC’s staff can attach to each part as it is picked.
Before deploying its RFID system, Bell Helicopter first established an RFID Strategy Council. “We were new to this space,” Druyvesteyn stated. “There was lots of interest in RFID across the organization. It was critical for the long-term success of RFID that we agree on a common, standard approach. Through the council, we settled on Gen 2 passive tags, the GRAI [global returnable asset identifier] encoding scheme, as well as IT infrastructure and governance policies.” The company chose OATSystems to provide software and integration, which supplied its OATxpress software platform to manage the capturing and filtering of RFID tag data.
The GRAI encoding scheme that Bell Helicopter utilizes includes specific numbers indicating the category of item being tagged—for example, 01 for part tags, and 02 for conveyance tags attached to the plastic tubs, dollies and trams used to move or ship materials. Because several departments within Bell were exploring RFID, there was concern regarding the risk of Electronic Product Code (EPC) number duplication across RFID projects. “We needed centralized management of EPC numbers,” Druyvesteyn said. As a result, he explained, “all EPC numbers are managed and issued by a single system overseen by OATSystems on its OATxpress server.”
The new process works as follows: First, one of Bell Helicopter’s manufacturing centers orders a part from the CDC. That order is picked and executed in the PTMS, which requests an EPC number from the OATxpress server. The PTMS then stores that number before forwarding the data to the BarTender label-generation software. The warehouse workers receive their pick orders from the PTMS, and walk down the warehouse aisles picking parts, using a Motorola Solutions MC-9190-G handheld computer to scan each component’s bar-code label. A mobile RP4T RFID printer-encoder from Zebra Technologies creates an RFID label for each component that workers then apply to the picked parts. The items are scanned to a unique bar-coded license plate on the reusable conveyances (plastic tub, kit dolly or tram), each equipped with two Omni-ID Max hard tags. This serves two purposes: It allows the individual conveyances to be tracked, while also offering redundant, indirect tracking for each order.
The RFID tags are read as tubs and parts pass through the dock doors while leaving the warehouse, and again at the eight production centers. The EPC number, date, read time and portal information are incorporated seamlessly into the PTMS, which records when a part was ordered, picked and scanned to a conveyance, when it left the warehouse, and when it then arrived at its respective destination.
The reader portals—incorporating Impinj Speedway R420 readers, each with four antennas—were designed and installed after several months of testing and development by Bell Helicopter and OATSystems. To determine whether tags attached to tubs and parts could be interrogated while passing through a reader portal, Bell’s RFID team moved a number of tagged items in a tub through a portal into the back of a truck, testing the system with 35 Alien paper labels with EPC Gen 2 inlays, as well as two Omni-ID hard tags.
“After we were convinced we had found the optimum antenna positions and reader settings, we did a real-world test with a forklift, driving the tub into the trailer as fast as it would go,” Druyvesteyn explained. “What surprised me, and the guys from Impinj helping with the test, was that we read every tag 100 percent of the time.”
But Bell Helicopter discovered another problem, Druyvesteyn reported. Each door presented unique deployment challenges, such as fire-sprinkler risers, dock-door and leveler controls, and forklift barriers. “We needed to develop a standard portal design that we could deploy anywhere in the company,” he stated. Therefore, the firm developed a tower design that protected the reader equipment, while maintaining the proper antenna position. “We were really excited about the first prototype,” he said. However, the team quickly found that in some cases, the towers obstructed the view of dock lock lights and control boxes. “This was a major safety concern; the lights tell forklift drivers that it’s safe to drive into a trailer.” Thus, Bell conceived an alternate, low-profile portal design. Not only is the low-profile design safer around dock doors, he said, but it also fits between doors spaced just 30 inches apart.
According to Druyvesteyn, one benefit to using the system—in addition to near 100 percent on-time delivery to distribution centers—is that lost parts and associated stock adjustments are down by 27.6 percent.
“I’m utterly ecstatic about results RFID has provided to us,” Druyvesteyn said, adding that the warehouse now receives far fewer phone calls asking about an order’s status. “Centers would normally call us and say, ‘We didn’t get the parts’. Now, we can tell them the time the parts arrived, and the door number they passed through.”
What’s more, Druyvesteyn said, “the technology can be used in other parts of the business. In essence, the CDC has become the RFID enabler for the entire business. The production centers that receive the parts now have the ability to track them further than just the dock door—they can track them between operations.”
Bell Helicopter’s deployment was a finalist for Best Implementation at this year’s RFID Journal Awards (see Finalists Unveiled for Sixth Annual RFID Journal Awards).