Banner Engineering‘s new Q45 Photoelectric Wireless Sensor merges two of the Minneapolis-based sensor manufacturing firm’s technologies: its photoelectric sensing technology that was traditionally wired, and its SureCross wireless sensor platform, to make it possible to use that sensor nearly anywhere, without running cable. The sensor, released last month, enables a user to send refill requests, or to have machinery automatically start or stop based on what the sensor detects. What’s more, it merely needs to be linked to a gateway reader and be placed in or affixed to a specific object to begin operating.
Banner Engineering has been producing photoelectric sensors for approximately 45 years, to manage such functions as controlling conveyors. When a box or other object passes in front of the sensor and breaks its light beam, the sensor transmits a notification to a programmable logic controller (PLC), which then responds with a command to the machinery that it controls. For example, the PLC may instruct a conveyor, motor or fan to stop. Until now, however, Banner Engineering’s sensors have needed to be wired to that PLC.
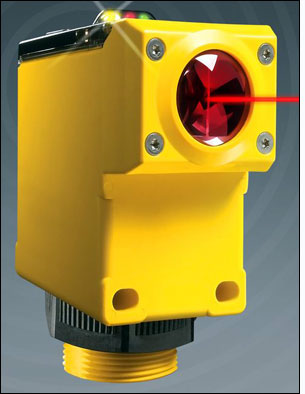
The wireless Q45 sensor utilizes technology that Banner developed about five years ago, when the company began providing wireless battery-powered sensors that transmit various types of data via 900 MHz or 2.4 GHZ signals (using a proprietary air-interface protocol). The technology has been employed for such applications as wirelessly detecting changes in temperature or humidity, and can be used to monitor conditions within a livestock facility (a poultry farm, for example), or to determine whether hot glue was applied to product packaging, based on that packaging’s temperature.
Recently, the company began developing a method for merging its wireless technology with its photoelectric Q45 sensors, resulting in the creation of the wireless version that functions similarly to active RFID sensor tags already on the market, such as those sold by Ekahau and AeroScout. Users of the wireless Q45 sensor can set the device anywhere they choose, after completing a brief series of tasks to link that sensor to a gateway. Although the device is slightly more expensive than the wired version, says Bob Gardner, the senior product manager of Banner’s wireless division, the elimination of the wire infrastructure makes it much less expensive to install. The technology was beta-tested by some companies in the United States, and the product is now being sold worldwide.The sensor operated well during beta testing, Gardner reports. Currently, he explains, a gateway supports as many as six sensors, but if an end user installs an industry-standard Modbus interface, a single gateway can accommodate up to 47 sensors.
According to Gardner, the device has a read range of up to 3,000 feet with a clear line of sight, and about 300 feet in an indoor industrial environment. Powered by two AA batteries, the Q45 wireless sensor beacons a “heart beat” every 30 seconds, unless it detects an object’s presence, in which case it immediately sends a transmission indicating the change in status. The gateway forwards that information to the PLC cabled to that gateway, and the PLC software then determines what action to take, such as stopping or starting some machinery.
The wireless Q45 sensor is equipped with a button that workers can press to indicate that an action is required (typically, replenishing a particular part on that section of a factory floor). That transmitted alert is received by the gateway, which can then forward an update to a computer or a handheld device carried by a worker, indicating that parts are needed.
The technology can also be used to measure water levels. In such a scenario, the wireless Q45 photoelectric sensor would be set up near a float. If that float dropped to a specified level, the sensor would detect that drop and transmit an alert to the gateway. This solution is useful at reservoirs or wastewater treatment plants for tracking the level of liquid within a tank or other containment area.
The wireless Q45 sensors can also be attached to objects that move, such as a rotating mechanical part within a factory. In this case, a sensor can simply be attached to the moving item, rather than requiring the installation of a slip ring or flexible cable, as would be the case if a wired sensor were used, to ensure mobility without breaking a cable.