Automobile manufacturer Audi is preparing to install a radio frequency identification solution for tracking its newly manufactured vehicles through finish work and shipping, at multiple global factories, based on a template installation in use at its new Hungarian plant. The EPC Gen 2 ultrahigh-frequency (UHF) RFID system, provided by German RFID company noFilis, was taken live when Audi Hungaria Motor Kft. launched the production in Győr, Hungary, in June 2013. The system is now being used to track the finishing and inspection of the A3 sedans and A3 cabriolets that the plant produces, as well as the vehicles’ outbound preparation and shipping.
The car company chose to create a template system at its new plant, where implementation would be easier than at factories that already have operational procedures in place for tracking vehicles. The manual systems typically employed at other plants require that drivers use paperwork to direct them through the finishing process, and that they exit the cars and scan bar codes at some locations as well, in order to create a record of their movements. This is not only labor-intensive, says Carsten Zimmer, Audi’s project manager of information processes, but also provides limited visibility for management into where each vehicle is in the finishing and shipping processes.
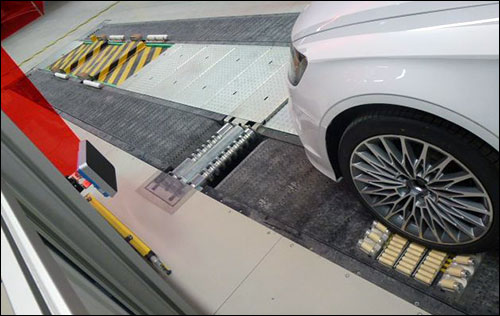
Once an assembled vehicle has its wheels in place, it begins moving through what is called finishing work. A driver actually drives the car to each appropriate station, to the storage yard, and then onto a truck or train. At the Győr plant, 160,000 vehicles are currently being produced annually, though that number is expected to increase. The cars are stored within one of two lots: one dedicated to shipping by truck and another dedicated to train shipment. A third yard contains additional spaces intended for use as production increases and new models are launched.
Audi sought to eliminate paperwork and make the finishing, outbound-preparation and subsequent shipping processes more transparent and leaner.
Once a vehicle has been assembled, a UHF Smartrac DogBone tag with an Impinj Monza 4QT inlay is attached to the inside of the front bumper. An automated tag-commissioning process in the production line writes the vehicle identification number (VIN) to the tag, as well as another ID number used by assembly stations. In this way, even if the computer system or local network goes down, workers can continue to identify each vehicle in front of them via an RFID reader.
The company installed approximately 50 Sick RFU 630 fixed readers within its assembly areas, as well as at gates leading into and out of storage yards. It also equipped workers with a Nordic ID Merlin or Agillox AGX DOT 300 handheld reader.
After a vehicle completes the assembly process and is tagged, a driver moves that car past an RFID reader, which forwards the tag’s ID number to the back-end system. NoFilis CrossTalk Agent software, residing on each reader, interprets the reads, filters out unnecessary data or false-positive read events and forwards the relevant information to Audi’s business middleware, which identifies the vehicle and transmits that data to Audi’s back-end system. The driver passes through a series of finishing and inspection stations, and with each read event, a record is created of which steps have been carried out. At the same time, the CrossTalk software manages and monitors the health of the RFID hardware and software. In the event that it identifies a problem, the system then issues an alert to the assigned recipient.
Once the finishing work is concluded, the driver moves the vehicle to the storage lot and parks it in one of the open parking spaces displayed on an LED screen. According to Patrick Hartmann, noFilis’ global sales director, tags are attached not only to vehicles, but also to some of the storage yard parking spaces, in order to create a record of that space in Audi’s management system and the CrossTalk software. Once the car is parked, the driver uses a handheld reader to interrogate the UHF RFID tag affixed to that space, as well as the tag on the car’s bumper, thereby creating a record of which space the vehicle is in. CrossTalk Mobile Agent software, installed on the handheld device, sends the data to Audi’s management system via a Wi-Fi connection. If there is a Wi-Fi problem, the data is stored until the network connection is resumed.
Since the system was taken live, Zimmer says, Audi has increased its transparency in regard to the plant’s car-management processes, and has saved time by eliminating “stop-and-go” scanner stations, which required drivers to step out of each car to scan bar codes or fill out forms related to the work in progress. In addition, it has reduced the quantity of paperwork for each vehicle.
Audi plans to go live with this system at other plants, following the template of the Hungarian installation. The rollout plants include locations in Ingolstadt and Neckarsulm, Germany; Brussels, Belgium; and San José Chiapa, Mexico.