When a supervisor at a British firm that manufactures offshore oil-drilling rigs received a new RFID tag to attach to pipes and other steel equipment, he sent an employee out behind the building to try to break it. In fact, he offered the man ₤5 if he could destroy the tag in three swings of a sledgehammer. The world of RFID tags in the heavy industrial, oil and gas, and construction industries is all about endurance. A tag must be rugged enough to withstand heavy blows, abrasion, extreme temperatures, high pressure, and immersion in water and harsh chemicals—and still be able to transmit its ID number to an RFID reader.
The tag being savaged by the oil-rig manufacturer was designed by Technologies ROI (TROI). The Dome Cable Tag, as it is named, is encased in rubber—and, in fact, the supervisor never had to pay up on the wager. The rig-maker’s employee placed the tag on a rock, then took the sledgehammer by its three-foot-long handle, raised it over his shoulder and swung the tool down so that its steel head, which weighed nearly six pounds, landed squarely on the tag. After three such blows, the tag remained undamaged, according to Patrick King, TROI’s founder and president, who says he was on-hand for the experiment and watched the hammer pummel his tag. When the worker rotated the handle so that the tag would be hit by the sharp edge of the hammer’s head, instead of its face, that was the tag’s undoing, King says, noting, “It took more than a few swings, essentially chopping at the tag like you would cut down a tree.”
It’s unlikely that the same worker efforts would have destroyed TROI’s newest models, King says: Armored-RFID and Weldable option World (WoW) tags, which consist of EPC Gen 2 inlays clad in stainless steel and weldable to metal surfaces. These durable tags are designed to be able to withstand temperatures of 600 degrees Fahrenheit (316 degrees) Celsius, as well as remain readable on and around metal and, above all, rugged. Like all other TROI tags, the Armored-RFID (commercially released this month) is available through resellers worldwide. What differentiates this tag from its predecessors and competitors, he explains, is its 1/8-inch-thick steel shell. Shaped in the form of dome, the Armored-RFID gleaming carapace can be welded to a metal object. Despite its metallic armor, the tag can still be read at six angles at a distance of up to 2 meters (6.6 feet).
That weldable feature appeals to those in industries such as oil and gas, says Evie Bennett, the VP of distributor William Frick & Co., which is preparing to sell the tag to customers in the oil and gas sector, as well as in construction. “This weldable tag is truly a breakthrough product,” she states, because it allows users, for the first time, to actually weld the tag to the item being tracked, thereby sparing that user from drilling holes for bolts, or from using an adhesive to attach the tag. With either bolts or adhesives, she points out, tags can be knocked off something like a pipe, or be removed by someone with criminal intent, and although, to her knowledge, the latter scenario has never occurred, it’s a concern the tags’ users express to her repeatedly, she says.
The rectangular WoW-1 tag (which measures 1.5 inches by 1 inch by 0.5 inch), the circular WoW-2 version (measuring 1.35 inches in diameter by 3 inches) and the Armored-RFID (1.25 inches in diameter by 0.5 inch thick) are embedded in a stainless steel case and a ceramic layer that can sustain temperatures ranging from 500 degrees to 1,000 degrees Fahrenheit (260 degrees to 538 degrees Celsius). They can be read from six different directions, through the metal, thanks to its antenna design. The Armored-RFID tag has additional insulation enabling it to function at temperatures of 600 degrees Fahrenheit or more.
The Armored-RFID tag’s casing is symmetrical, and its steel shell is an active element of the tag acting as an antenna, not just as a cover for protection. The tag couples inductively with its metal shell, enabling it to receive and transmit RF signals. That unique design and the durable tag that results, King says, are what differentiate his small company from the larger RFID tag providers. He develops all of his tags, he indicates, with oil and gas, construction and heavy-industrial companies in mind.
TROI was established by King in 2003. A synthetic organic chemist, he has been an entrepreneur in printing, thermal imaging and automatic identification, among other fields. With some experience in RFID technology, he established TROI to initially provide consulting services, then joined the staff of Michelin Tires as a global electronic strategist—a position he still holds to this day. In that role, he has helped the tire and automotive industry develop RFID standards for tagging and tracking assets and work in progress.
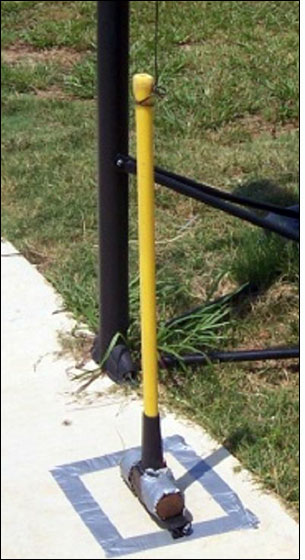
In addition, King began developing a tag that could serve the oil and gas industry better than the bar-coded tags and plastic RFID hangtags frequently used to track pipes and tools. “I realized there were no tags,” he states, “that were rugged enough for that environment.”
To create all of his tags, King says, he starts with an ultrahigh-frequency (UHF) Gen 2 RFID chip, such as the models available from Alien Technology, Impinj or NXP Semiconductors. The chip comes bonded to a pair of wires and sealed in a plastic casing from the wires protrude. He then takes this chip to a third-party manufacturer that solders it to a circuit board with an antenna, resulting in a complete RFID inlay that, he says, is extremely durable. In the case of the Armored-RFID tag, space shuttle materials (a foam skin coated in high-temperature ceramic) are added for greater insulation, thus allowing higher temperatures. Depending on the model, he says, TROI’s tags might also be sealed in silicon, Teflon, rubber, thermoplastics or urethane.
Earlier this year, to test the Armored-RFID tag’s durability, as well as that of other TROI tags, the company’s employees attached the tag to the head of a 12-pound sledgehammer, raised it to a height of 3 meters (9.8 feet) and then released it so that it smashed against the concrete surface below. They then did the same to industrial tags produced by competitors, such as Omni-ID, Confidex and Intermec. The process was repeated until the tag’s case ruptured, then continued until the tag was no longer readable. For most tags from TROI’s competitors, King says, the case ruptured after one to 10 drops, with one surviving for 20 drops. The TROI tags, on the other hand, did not rupture. While most of the tags tested were unreadable after between three and 60 drops, he notes, the majority of TROI’s tags continued to be read until the 115th to 170th drop, and none ever cracked.
William Frick has put the tags through its own set of tests, Bennett says. “We’ve taken sledgehammers to them, we’ve tested them with torches, baked them in the oven, even thrown them in the barbecue,” she says. What’s more, end users have placed the tags at the bottom of the ocean floor at a depth of about 1 mile, and they were still functional upon returning to the surface. “I don’t know of any other tags that can do that,” she says.