Automotive subassembly company Android Industries reports that it has reduced the labor cost of its inventory and operations replenishment by 10 percent, using a combination radio frequency identification and bar-code solution provided by Zebra Technologies. The system, installed two years ago at the company’s facility in Arlington, Texas, allows workers to use either an RFID tag or a bar-code scan to order parts from the warehouse, while warehouse workers retrieving the goods can view the order on their onboard computers via Zebra’s Material Flow software application.
Android Industries assembles complex modular systems, including instrument panels and vehicle assemblies, and ships those units to its customers’ car and truck factories. Its business has been growing, the company reports, and it continues to employ lean manufacturing practices to keep costs low.
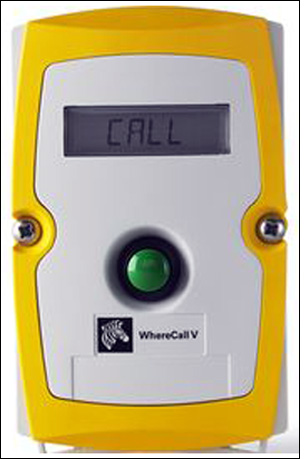
Recently, Android Industries wanted to use an automated system to better manage its material flow and replenishment processes, while also reducing waste. The firm must often make quick changes to its operations in response to customers’ orders, and it needed a flexible system that would enable it to change the parts associated with a specific workstation easily.
Before installing the Material Flow replenishment system, Android Industries used a manual method to keep its assembly staff furnished with the parts required for the task at hand, says Dirk Cranney, Android Industries’ material manager. Workers from the warehouse would drive through the facility’s assembly areas, searching for component containers with low levels of parts, and would then locate a replenishment supply of those components. Assembly workers, known as operators, would either send a message via radio or simply shout out to those individuals when they needed parts, or they would place a piece of paper on top of any components boxes they had emptied, indicating the need for replenishment.
The warehouse staff had to remember where those parts were located within the warehouse, and then find them and bring them to the operator. As the Arlington site—the company’s largest—was growing, several buildings were added, totaling 750,000 square feet of storage area. What’s more, goods were often stored farther from the assembly area, and the assembly area itself was becoming larger. All combined, this created a greater challenge for staff members attempting to manage replenishment via the manual system. Operators might not find someone in the area within hearing range to ask for replacement parts, or workers may have trouble locating parts within the warehouse, or miss an empty parts box on the assembly floor that required replenishment.For management, there was little visibility into what was happening with this system, as well as when inventory levels were getting low in the warehouse.
With the Zebra system in place, the process is simpler, the company reports, requiring fewer trips for the warehouse staff. Operators at each station are equipped with one of two devices; if they use just one replaceable part, they have a pendant consisting of a WhereCall V battery-powered 2.4 GHz RFID tag complying with the ISO 24730 standard for 2.4 GHz active real-time location systems (RTLS), with a single push button. If they use more than one part, they have a bar-code scanner that links back to the Material Flow software on Android Industries’ database. A single WhereNet RFID reader installed on the ceiling can interrogate all WhereCall tags within about a 7,500-square-foot area in which assembly is taking place, says Adebayo Onigbanjo, Zebra Technologies’ senior product marketing manager.
If an operator’s parts supply is running low, he can press the button on the WhereCall pendant, which transmits a replenishment request, along with its unique ID number, to the reader. The reader then forwards that information to the Zebra software via a wireless connection. The software, residing on Android Industries’ back-end system, retrieves the part number associated with that particular tag ID and sends an alert to a defined group of 20 onboard computers running the software on warehouse forklift vehicles, thereby indicating the need for a specific part by a specific operator.
One of the forklift drivers can respond to the request by pressing a prompt using the touchscreen, and therein, the order will be displayed only on the responding driver’s screen. The Zebra software instructs the driver as to where boxes filled with those parts are located within the warehouse, based on the company’s predetermined storage plans. He can then proceed to that location, take a box of parts, deliver it to the requesting operator’s station (also displayed on the software) and press a prompt indicating that the order has been fulfilled. The system also captures timestamps from the initial call to the delivery, enabling Android Industries to understand the efficiency of its replenishment process, as well as the frequency of parts replenishment.
Those ordering multiple parts can scan the bar-code on the boxes of the items requiring replacement, which will then be transmitted from the bar-code scanner to the Zebra software. The same process of displaying data takes place for forklift drivers.If a forklift driver pulls material from a storage location and sees that the inventory levels for those goods have dropped to a specified minimum, he can create an exception in the Material Flow software that sends a text message or e-mail to the office staff, indicating the need for a investigation or reorder. The data used by Material Flow is generated directly from the enterprise resource planning (ERP) system’s data, and is imported into the Material Flow software.
The efficiency gains have reduced expenses for the company, Cranney says, and have led to Android already recouping its investment. Warehouse workers spend less time driving around the facility, which saves on labor and fuel costs, and also increases productivity. He estimates that the cost of material replenishment has dropped by approximately 10 percent since the system was installed.
“We have models that assess the flow in the plant,” Cranney says, adding that using the WhereNet system “adds to the data we use to do that.” The solution enables management to easily determine such details as the number of replenishment orders fulfilled per warehouse worker, and opportunities to rebalance workloads as needed. More important, he says, the system provides safety improvements, since the less time staff members spend driving around “sharking” the assembly floor (circling the area looking for goods that require replenishment), the less opportunity there is for injuries.
Android Industries operates multiple assembly facilities around the world, of varying sizes. According to Cranney, the company is currently considering ways to expand the Material Flow application to some of those other locations.