Oil and gas company Canadian Natural Resources Ltd. (CNRL) has replaced its paper-based employee-mustering system with a real-time location system (RTLS) solution using ultra-wideband (UWB) technology to identify the locations of workers in the event of an emergency or drill. The system, provided by Connectus Global and using technology from Sewio, allows a mustering process that the company claims is 10 times faster than the manual version. Managers will employ the technology during annual maintenance shutdowns and turnovers, when activities raise the risk of an emergency incident and hundreds of workers unfamiliar to the site are on hand.
The system was first deployed at the company’s Pine River plant in Michigan for a 2019 mustering event, and it provided visibility to enable a quick worker safety response if an emergency occurred. CNRL had acquired the factory that same year and had found that the facility’s existing infrastructure lacked the security it wanted for worker safety during turnarounds. The oil and gas company’s concern was to ensure that hundreds of employees could be counted and located during an emergency.
According to Mike Anderson, Connectus’s CEO, CNRL began developing a solution with Connectus to gain location services that would digitize the mustering process while helping management to “understand the movements of their workers in the site.” The natural gas and crude oil producer is headquartered in Alberta, with sites located throughout North America, the United Kingdom’s North Sea and offshore Africa. It is the largest independent natural gas producer in Canada and one of the largest land bases for undeveloped natural gas-prone areas of northeast British Columbia and northwest Alberta.
The Pine River facility processes and exports low-pressure, liquid natural gas (LNG) and sulfur. Like other production sites in the company’s portfolio, the plant must accomplish periodic and planned maintenance shutdowns and turnarounds. During such maintenance operations, approximately 350 workers, most of whom have never been onsite before, arrive to accomplish tasks that can create hazardous conditions. During turnarounds, tanks and equipment are cooled and drained, which can potentially cause a build-up of pressure and expose volatile compounds to oxygen.
With a large number of temporary workers onsite, the company wanted to address any increased risk during turnarounds, in comparison to normal maintenance operations, and to boost safety and preventative measures. By using technology from Connectus, the firm could digitize the mustering process by which all workers onsite report to an assigned mustering location in the event of a drill or actual emergency. Management could then know that all individuals had been accounted for, or view who was missing and might require assistance. Such mustering, when carried out manually with paper and pen, typically took three or four hours to account for all employees, whereas CNRL sought to reduce that time to just minutes.
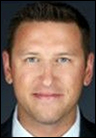
Mike Anderson
Connectus is a systems integrator that provides technology for use at industrial sites at which hazardous area certification is required, Anderson says. The company provides certified-safe equipment and software to manage data from a worksite. Connectus initially deployed the solution in 2019 at the Pine River plant throughout the course of about three months, using temporary power to energize 19 UWB anchors installed at the facility. Those anchors identified the locations of workers’ tags within seven sections or zones, totaling 2,800 square meters (30,140 square feet). To make the technology safe around hazardous materials, Connectus builds Sewio’s UWB anchors into its enclosures.
A total of 350 workers reporting onsite during the turnaround were provided with Connectus badges, which include a built-in UWB chip and antenna, as well as a panic button for man-down reporting. The badge provides not only real-time location during a mustering event, but also access control via an HF RFID chip. The tracking badge includes a panic button with the man-down feature. When that button is pressed, it sends an alarm to Connectus software residing on the plant’s dedicated server, and that alert is then forwarded to the fire and gas system and the control room.
Connectus built the badge and Sewio’s UWB processing board into its injection mold housing. The dual-lock rubber seal provides intrinsically safe certification, Anderson says, as well as FCC and CE certifications, to operate around particulates, dust, oil, chemicals and static charge. “We’ve done a lot of leg work to bring the tag up to a standard that it can be used in an industrial framework and hazardous use cases,” he states. The Connectus software can operate either in the cloud or via an on-premises server; CNRL set up the system using the latter configuration.
During a turnaround, which usually takes place throughout a span of around six weeks, every worker acquires a badge upon entering, which contains a unique ID number linked to that individual’s identification information. Each day, as employees report to work, the detection of their badges can be used to update shift reports. The collected data can also provide dashboards for production, to let a company understand shift and breaktime compliance, time on tools and other data related to a given worker’s location.
The data is otherwise leveraged for mustering purposes. In the event of an emergency or drill, those officials responsible for worker safety can access the software and thereby view lists indicating who must muster at specific sites. As individuals report to their assigned mustering sites, the software is updated to indicate who has and has not been accounted for. If any individuals are still onsite, the software can provide their location within the zone in which their badges are being read.
The information thus enables managers to respond accordingly if someone has not reported for mustering. This process of mustering workers, which previously took 120 minutes, was completed in only 12 minutes using the UWB technology during the first drill in 2019. In addition, the amount of time required to deliver sign-in and sign-out sheets after the completion of mustering was reduced from eight minutes to one second, since the software provides the evacuation list in real time.
While CNRL’s primary focus was on worker safety, Anderson says, the system also reduces insurance fees. When the next turnaround takes place, Connectus will return to the site to redeploy the anchors. The oil and gas company did not respond to requests for comments about the system for this article.