For the past two years, Vale Inco has been using radio frequency identification technology to track the grade, or mineral concentration, of ore as it is mined in real time. Geologists at the company’s Stobie mine, on the south side of Ontario’s mineral-rich Sudbury Basin, inspect the ore at each blast site, then encode the grade to disposable RFID tags using handheld devices. They put the tags into the ore piles, which are picked up by large vehicles called “scoops” and transferred to chutes that lead them to a conveyor system. From there, the ore goes to a “crusher” that reduces it to 8-inch rocks, then to an elevator that takes it to yet another conveyor system, which deposits the ore in rail cars that transport it to processing mills.
Along the way, strategically placed RFID interrogators read the plastic-encased RFID tags, which are designed to survive the crusher. The information from the tag reads is transferred to a database designed for this project through a system of fiber optic cables that run through the mine.
The RFID system, which replaced a manual, paper-based process, allows the company to more accurately forecast which type of ore it mines and provides visibility into how long it will take to haul the ore to the surface. It also enables Vale Inco to provide the mills with better information regarding the ore blend they should expect, so they can prepare the proper chemicals to process the ore into metals, including copper and nickel. Once the solution is deployed in all of Vale Inco’s Canadian mines, and mine operators can supply the processing mills with a consistent ore mix to maximize metal production, the company expects to save $30 million to $70 million a year, according to Mark Palkovits, a geologic technologist who supervises the project.
The RFID program is one of several at Vale Inco’s Ontario mines designed to gain efficiencies and insight into ore production, transport and refining. The company has been using RFID since 2005 to track containers, drills and vehicles in its mines over existing wireless access points, originally set up for voice communications, to ensure equipment is readily available when needed. Earlier this year, the company started using active RFID to track rail cars from its Creighton and Stobie mines to mills, to provide an audit trail of shipments to customers.
“RFID has helped us automate the ore movement from underground to mill processing,” says Peter Cunningham, Vale Inco’s superintendent of process automation. “It helps us know how much each mine is producing, track the blending of the ore and track the transportation.”
Academia RFID‘s Centre of Excellence, a research and development facility in Montreal that helped develop the RFID solution for tracking ore grades in real time at the Stobie mine, is now working with a U.S. silver mine to implement a similar solution. “This will help them narrow the gap between their forecasts and reality,” says Anthony Palermo, Academia’s business development director.
Like Vale Inco, mining companies worldwide that have had positive experiences with RFID are embarking on new projects using the technology to further streamline production and increase profitability. One RFID application that has been delivering benefits is tracking vehicles underground, in dark, loud tunnels, to reduce or eliminate collisions. This not only protects workers but saves expenses on vehicle repair and replacement—some haulers cost as much as $800,000 apiece. Another application tracks assets—from tools to safety equipment—to ensure they’re in the right place when needed. (See related news stories and cases studies detailing these applications on RFID Journal‘s Web site.)
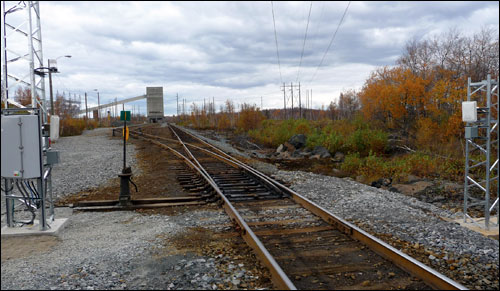
Some of the new applications build on these vehicle- and asset-tracking deployments. At Anglo American‘s El Soldado mine in Chile, for example, a vehicle-tracking system underground also gives mine managers above ground real-time information on the whereabouts of 800 workers, says Javier Ignacio Torres, commercial manager of RFID Chile, which helped develop the solution. And systems that track workers can also prevent people from trespassing and entering hazardous zones, says Frank Wehus, general manager of the Norway office of Identec Solutions, which has deployed RFID solutions for mining customers in Europe, Scandinavia and the United States.
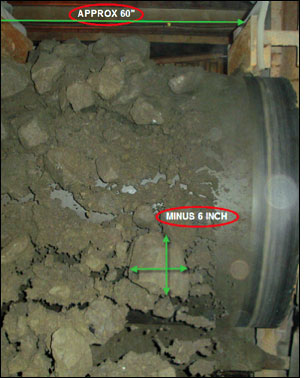
Other RFID applications, such as Vale Inco’s ore-monitoring solution, explore new territory. One area is managing contract labor and rental tools—which the CEO of a major gold and copper mining company described as “a $100 million-per-year problem,” according to Sam Falsafi, energy principal for Shipcom Wireless, a supply-chain software company that works with mining and energy companies. Mining companies are also using RFID to control energy costs.
On the horizon are RFID applications that can help to better maintain equipment, survey potential mining sites and automate drilling. One of the most pressing concerns, highlighted by the recent explosions that resulted in miner deaths in China and West Virginia, is worker safety. Mining companies are increasingly looking to RFID to help protect workers and keep mine conditions safe.
Managing Contract Labor and RENTAL Equipment
The mining industry worldwide relies on numerous contractors to supply workers, tools and equipment, such as vehicles and drills, to construct mines and keep them operational. Contract workers can include construction workers, electrical technicians, maintenance staff and the people who work at mine-site restaurants. In fact, thousands of contract workers and pieces of equipment can be on site at any given time—often during multiyear projects.
Verifying that contractors are doing the work they were hired to perform and billing for the correct number of hours is a big challenge for mining companies. What’s more, rental equipment sometimes gets misplaced in the mines while rental fees for that equipment continue to accrue. “Currently, it’s a pen-and-paper system, and many mines are getting overbilled for goods and services,” Falsafi says.
To help manage this million-dollar problem, Shipcom is developing an RFID system that tracks equipment and automatically feeds the data gathered from RFID interrogators into an enterprise resource planning (ERP) application. The system enables real-time synchronization between financial and operational transactions, and matches events to invoices to facilitate payments. “When it comes to visibility, we want to provide a connection between the top floor and the shop floor,” Falsafi says.
In Chile, construction company Bechtel is using an RFID system designed by RFID Chile to mange contract workers as they construct a new copper mine for Anglo American at Los Bronces, in the Andes Mountains. The project, started in 2008, will extend into next year. Each contract worker is issued an RFID-enabled ID badge—Bechtel has purchased 20,000 badges so far—that includes name, photo, company name and Chilean tax identification number.
The RFID system has reduced the time it takes to clear a busload of contract workers through access points from 25 minutes to 7 minutes, says Max von Dessauer, RFID Chile’s technology director. It also allows roving “timekeepers” armed with handheld RFID readers to scan the ID badges, then enter work codes. The information is transferred to the company’s computerized payroll system over a USB port. The timekeepers don’t have to stop and ask the workers’ names, says von Dessauer. “They just walk around with a PDA and point it at the person and receive the information from the tag.”
Controlling Energy Costs
At Vale Inco’s Creighton mine, which is 7,200 feet deep and consists of numerous levels, officials have been using RFID to control the air-ventilation system, instead of keeping all the fans running at full speed. When vehicles equipped with RFID tags enter a new level, the tags are read by wireless access points, which also collect data from mobile equipment and, in some mines, provide voice communications. The tags alert the air-ventilation system to adjust the fan speed. “This is a huge power savings,” Cunningham says.
In 2009, Newmont Mining, one of the world’s largest producers of gold, deployed a Wi-Fi RFID solution from AeroScout to track more than 600 miners and 95 vehicles, to improve worker safety and drive operational upgrades at its Leeville and Midas mines in Nevada. This year, the company plans to expand the RFID systems to optimize air quality and power usage, says Julio Castillo, Newmont’s underground mine control manager. Based on these successful deployments, Newmont is updating its standard business model to include RFID in new mine development, and is considering the addition of RFID in its other mines as well.
Mining Future Benefits
“The mining industry realizes that it needs to become a tech-intensive industry to be more efficient, so it can still make money despite increased production and labor costs, and increased competition,” says RFID Chile’s Torres. RFID Chile is now working with mining customers to use RFID to optimize equipment maintenance and repair. One pilot tracks truck tires to get precise readings on how many kilometers they have traveled, so the tires can be retreaded before too much wear and tear shortens their lifetime.
RFID, in combination with other leading-edge technologies, is helping mining companies survey remote locations to determine ore types and potential yields of prospective sites. Field workers can label and track samples with RFID, validate the locations with GPS and use satellites to transmit the data, says Konrad Konarski, managing principal of KBR Wireless. Konarski is working with several mines in South America to RFID-tag coring samples, which can be pulled from as deep as 1,000 feet. The mines are also using ultra-long-range passive RFID tags to mark spots in remote locations where coring samples have been pulled.
“Most of the mine locations are surrounded by so much vegetation that if you come back three months later, they are virtually impossible to find,” Konarski says. “RFID allows you to go around and retrieve that data and find where the original sample was taken from.”
And RFID could help usher in a new era of automation in mining. Vale Inco is researching whether it can robotically operate RFID-tagged drills underground from the surface. RFID would help ensure that the equipment is positioned in the correct location. The remote drilling would cut down on the time to transport workers thousands of feet into the mine. “Once in place, the worker on the surface can run three drills at one time,” Cunningham says. The workers would also be well out of harm’s way.
Can RFID and Gas Sensors Keep Miners Safer?
After the Apr. 5 explosion at Massey Energy‘s Upper Big Branch South Mine left 29 West Virginia miners dead, the spotlight once again focused on mine worker safety. The White House ordered an investigation, U.S. lawmakers raised the prospect of new regulations—and some mining experts said pairing RFID with environmental sensors could better protect miners.
When RFID Journal last wrote about the mining industry in 2006, only a handful of mines were using RFID to protect workers. A Swedish mine, for example, outfitted miners with active RFID tags to let managers know their whereabouts in the event of an emergency. And a South African mine deployed an RFID system to ensure workers were equipped with safety devices.
Later that year, after a disaster in Sago, W.Va., killed 12 coal miners, the U.S. Congress passed the Mine Improvement and New Emergency Response (MINER) Act. The law requires mining companies to install electronic tracking and two-way wireless communications systems so rescue workers can locate and talk to trapped miners. Australia, China and other nations are also requiring better tracking of miners. These mandates have spurred more widespread use of RFID as a tool for identifying miners as they enter or exit a mine, as well as locating them in the mine in the event of an accident or evacuation.
U.S. mines are also required to monitor underground gases and air quality with sensing equipment. But many mines fulfill that requirement by placing gas detectors only at the location of exhaust systems that pull air out of the mine, and communicating that information over a landline to the surface. (Some mines also equip miners with pocketsize methane detectors, which don’t report results to the surface.) The probe into April’s accident is still under way, but preliminary results indicate that an explosion occurred after a deadly buildup of methane gas about 1,000 feet underground, and the source of the gas may have been a closed mine shaft.
RFID and sensor technologies located throughout a mine could alert mine operators on the surface—in real time—about dangerous levels of gases building up anywhere underground, so the operators could evacuate the mines. “We can footprint the mine with methane sensors wirelessly connected to our communications backbone, to prevent something like this from happening ever again,” says Mark Rose, president and CEO of Tunnel Radio of America, which sells RFID and wireless communications technologies to 23 mines in West Virginia.
Today, most sensing systems must be hardwired to the surface to communicate environmental conditions, and that tends to limit the number of gas-detecting locations. “We’re looking at several options now for getting the information from the sensors out to the mine surface to the mine operations center,” says Dave Snyder, a senior mine electrical engineer in the mine safety and health research office of the National Institute for Occupational Safety and Health at the Centers for Disease Control and Prevention. “The MINER Act required two things: tracking and wireless communications. So the wireless communications backbone that the act requires can also logically be used to communicate with sensors up to the surface.”