Ed. Note: A version of this article originally appeared at IoP Journal.
At a time when Brazilians are radically divided by ideological currents and even by football teams, good news is emerging in the cotton sector: two companies are raising the quality level of cotton, both within the country and abroad. ID-Cotton, the winner of the 2020 IoP Journal Award, with its solution for tracking cotton crops via radio frequency identification technology, and AG Surveyors, which carries out cotton inspection and certification, have signed a 10-year partnership that is expected to have an international impact on the market.
In an interview with IoP Journal TV (conducted in Portuguese), AG Surveyors’ Carlos Freitas and Giovanna Freitas, together with ID-Cotton’s Flavio Tarasoff, explained the extent of the work, which began several weeks ago. ID-Cotton records cotton bales in the field, with management and traceability to the specific cotton plant, linking the SAI code (the identification system of the Cotton Brazil association) and generating a shipment of those specific bales. AG Surveyors receives the batch shipped via the system and, when the truck arrives at the port, reads each bale via RFID.
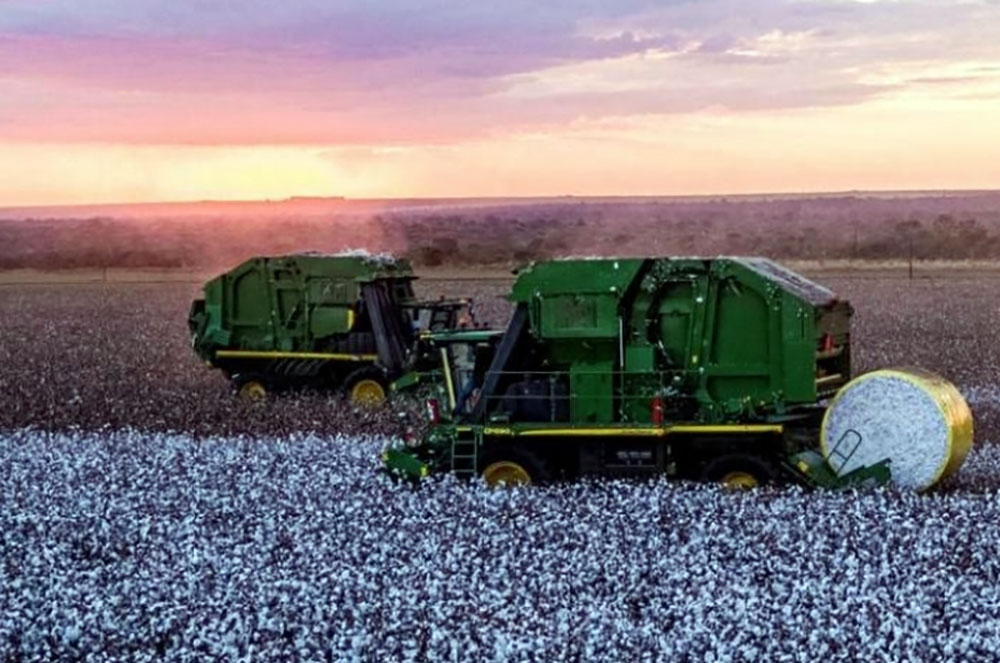
D-Cotton records cotton bales in the field via RFID.
Thus, the company can guarantee only bales that are part of a specific order are shipped in a given container, as well as automatically generate a packing list for customs and then provide the file to the port of destination in order to confirm the cargo. According to Freitas, the implementation met the company’s expectations. “We gained speed, process accuracy and confidence,” he says. All products are tracked from plantation to final consumer via GS1‘s Electronic Product Code (EPC) standard. “The deployment follows the GS1 standard,” Tarasoff explains, “because it guarantees easy data interoperability and preserves the RFID investment.”
Mobile devices with embedded readers are being used for the deployment, Tarasoff says. “Since the operating environment involves third-party terminals or third-party warehouses,” he states, “and due to the operation’s own dynamics, where there may be changes in a container’s location, we are unable to use fixed readers. A mobile device is a kind of portable computer, offering the possibility of adding an app to process data and relevant information to the chain.” One activity utilizes middleware developed by ID-Cotton.
According to Freitas, deploying RFID has provided a positive experience for the company, since it eliminates errors resulting from operations previously performed manually. As with any novelty, Tarasoff recalls, the RFID deployment generated some initial resistance, though it proved to be a wise decision. Previously, he says, processes were carried out manually, either with forms or, at some stages, via spreadsheets and emails exchanged between the company and customers. There was little integration of information, resulting in delays regarding data consolidation and reporting.
Freitas says the partnership with ID-Cotton is providing mobile devices and software for collection, as well as integration with inspection-control software. “The main objective is to use the ID-Cotton solution,” he states, “linking the production chain with logistics.” The tags are being added to the SAI system during cotton processing, prior to shipment to the port. “Thus, the same tag applied to the cotton plant is used for blocking, shipping, port logistics and segregation in the textile industry,” Tarasoff says, “where the cotton must be transformed into yarn.”
The main challenges the project faced, according to Tarasoff, were the need for collection mobility, which was solved using mobile devices; the definition of reading parameters and the exposure time of the tags, which contain Impinj chips; and the change in operating culture. The latter involved demonstrating to terminals and operators the gains in precision and speed compared to visual and manual recording.
“The next step of the initiative,” Tarasoff reports, “is to carry out the integration to monitor and indicate ports of destination for each container.” RFID technology is already integrated into the company’s enterprise resource planning system, he says, which has eliminated several steps and allowed for integration between terminal operations and information provided by customers.