- Step One: Strategizing
- Getting Solution Providers Onboard Early
- Key Questions to Ask Before You Proceed
- Addressing Misconceptions
Radio frequency identification (RFID) technology is well equipped for tracking tools on a worksite, whether that involves wrenches on a manufacturing site or generators in a large utility yard. However, ensuring the technology provides a solution that works requires some planning.
Tool-tracking systems are not “one size fits all” propositions. They require customization, testing and phased deployment in many cases, and it’s important to understand what the technology can and cannot do. Metal tools can be identified via handheld readers, or as they pass through fixed reader zones, or they can be counted in toolboxes with desktop readers if the box is open, but such devices are less apt to provide real-time location across a wide area.
There are commonalities for tool tracking. Most companies seeking RFID solutions share the same general needs and challenges, regardless of industry, according to Daniel Vick, Brady Corp.‘s product manager for RFID solutions. “Tools are a critical part of customer manufacturing and maintenance operations,” he says, “and keeping track of which employee has a particular tool, and where that tool is at any given time, can be difficult to manage.” The result is a cost around the labor required to locate tools, he says, and the additional expense of replacing any that have gone missing.
Step One: Strategizing
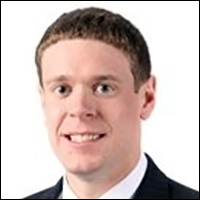
Daniel Vick
These are challenges RFID can effectively address in most cases, Vick says, though there are several key points companies should consider before planning an RFID deployment for tracking tools. One is the environment in which the tools will typically be used. For instance, automotive environments mean varying temperatures, as well as the presence of grease, oil or water, according to Colynn Black, Metalcraft‘s RFID business-development director
Most tools are largely made of metal, a material that often causes interference and reflection of RF transmissions, so on-metal tags may be needed. Another challenge is that tagging the variety of shapes and sizes of tools can be difficult, since there are usually only one or two types of tags for all applications. “Those three things, right off the bat, can be discouraging for a lot of companies” seeking tool-tracking solutions, Black says, but that doesn’t necessarily mean RFID won’t provide benefits.
The first step requires a targeted mindset. Companies need to involve all the parties whom the solution will impact during decision making, including supervisors on the production floor, as well as IT directors, asset managers and corporate leaders. Start with you process goals, Black suggests, then walk through the process as though everything was already in place. That allows you to decide where and how the technology can be used. Most importantly, he adds, users need to consider how they will achieve their goals. Without clear goals from the onset, it will be hard to ensure the RFID adoption was worth the investment.
Getting Solution Providers Onboard Early
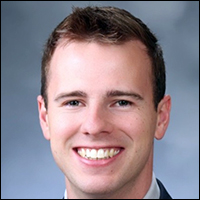
Colynn Black
Real-time location, by which users know exactly where everything is at all times, sounds impressive, Black says, “And it is for a lot of applications, but tool tracking isn’t quite there yet.” Among the early benefits users achieve are the ability to know when a tool has left a certain zone, and to find an item on a shop floor that needs maintenance, with the help of a handheld reader. Starting with such low-hanging fruit can lead to the capture of data that will provide many more benefits, Black says.
In the long term, RFID enables analytics with information never before available. It helps to have experienced support early, Vick notes. “My best recommendation is to identify a trusted solution provider with RFID experience to work with,” he states, “to help them through the entire solution lifecycle, including system design, quoting and implementation.”
Many RFID solutions have the benefit of being scalable; a customer can start with a small scope, then expand once they realize the benefits of RFID. In practical terms, this can mean tracking only a few critical tools within a small area initially, and later expanding to include more tools and other areas. Alternatively, customers can expand into new use cases in additional areas of their business operations, such as shipment tracking, work-in-process tracking or monitoring assets other than tools.
Key Questions to Ask Before You Proceed
From a system design perspective, Vick says, some key considerations and questions must be raised. No matter what the early goals are, businesses can ask some common questions that will help them deploy a working solution. According to Vick, these questions include:
- What specific tools should be tagged?
- How many tools are there?
- In what areas do the tools need to be tracked?
- When not in use, will they be stored in a certain spot, such as a tool crib?
- What is the current process, if any, for tracking tools?
- Where is that process failing?
- Are there any software platforms that tool-tracking data should be integrated into?
- Which tag works for the tools and their environment?
“Generally,” Vick says, “I recommend onsite testing with a number of different tags to confirm which performs best for a given asset in a customer’s environment.”
The next thing to consider is reader and antenna deployment. The specific positioning of readers and antennas, and the configuration—such as power level—of readers should be based on the company’s desired tracking zones, and that may require some level of calibration after installation. Because of the nuances of RFID, Vick recommends this work be performed or supervised by a solutions provider. Exceptions to this, he notes, can include preconfigured solutions, such as RFID-enabled vending machines.
Finally, there’s the question of choosing software. In general, software interprets raw tag read data and displays information in a way that is useful to a customer. Software can be standalone or be integrated into other systems. It can be on-premise or cloud-based. And it can range from relatively simple to very complex. “Solution providers will generally be responsible for recommending existing or custom software,” Vick says, “or otherwise providing software as part of a solution.”
Addressing Misconceptions
There are a few ways in which tool tracking is commonly being accomplished at present. Smart cabinets are frequently being used in the pharmaceutical and healthcare industries, as well as for tool management. Such cabinets come with built-in readers that capture the tag ID number of every tool or other asset within, identifying when items are removed.
A fixed or handheld reader, used in a tool cage, can capture every time a tagged tool leaves storage and, in some cases, with which worker. Handheld readers can be carried around a worksite to locate tools that have been misplaced, or to identify those that require maintenance. Regular audits can be accomplished to locate tools that have gone missing, as well as reconcile inventories and reduce the need for reorders.
Many companies that approach Brady Corp. or Metalcraft expect RFID to provide a real-time view into an entire site once the tags are in place. For this reason, Vick says, “It is important to set appropriate expectations.” He calls this common misconception “GPS performance expectations,” and says customers often look to the technology exclusively to provide a constant view into each item’s location. “Many of us are conditioned, through our vehicles and smartphones, to associate the concept of asset tracking with GPS navigation.” However, passive UHF RFID operates best as a zone-based location system, with real-world read distances ranging from 5 to 50 feet.
Additionally, companies often express to Brady Corp. a desire for any tool-tracking system to be as automated as possible. While many aspects of tool tracking can be automated with RFID and data integration, Vick says, the most successful solutions always involve a commitment to following certain processes, such as employees scanning a badge to check out tools within a tool crib.
Key Takeaways:
- Tool-tracking solutions are bringing value to companies that track when tools leave storage areas, enter specific zones or require maintenance.
- Succeeding with a tool-tracking solution requires understanding what the technology can and cannot do within a particular environment.