Businesses need answers, not just more technology. They require applications that leverage technology to solve problems today and will lead to additional solutions tomorrow. Specifically, what is real today—and what will be real in the near term—for active ultrahigh-frequency (UHF) RFID solutions that will support effective business applications?
Basics on Active UHF RFID
Currently, ruggedized active (battery-powered) UHF RFID tags can be read from a distance of 300 feet to more than 1,500 feet away, while passive RFID tags offer an effective range of less than 30 feet, even while exposed to very harsh environments, including temperature extremes and even under many feet of snow. Reading tags on, in or around steel, iron or other metal assets no longer presents a problem. Active tags can also be read while moving at 60 miles per hour or more, with near 100 percent reliability.
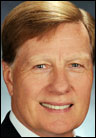
The readers, not much bigger than a pack of cigarettes, can be in fixed positions and aided by ground loops and other devices to ensure high accuracy for determining identification, time, direction and location. The UHF frequency band is desirable for active tags, due to general acceptance by the Federal Communications Commission (FCC), and is currently used in a wide variety of applications—from bridge and highway toll collection to container tracking. The UHF signals do not interfere with portable smartphones, consumer wireless devices and other transmitters. Therefore, accuracy is very high and interference is never a problem.
Telematics, Vehicle and Cargo Tracking
Tens of thousands of trucks and other vehicles can be tracked as they move into and out of distribution centers, seaports, warehouses and other facilities, in order to ensure efficient operations, environmental concerns, safety and security. What is new is the concept of instantly identifying the driver along with the truck’s cab, trailer and cargo—each with its own tag—at a gate. If all four do not match up as expected, then an alert is issued immediately.
Integrating this function with other capabilities, such as weigh scales, will ensure, for example, that trucks deliver what is needed and leave empty, and that all is confirmed at the gates with time and date stamps. Going further is integration with other technologies, including video, photography and license plate recognition, as well as bar-code labels, passive UHF and high-frequency (HF) tags, and active RFID sensors, such as those designed for monitoring cargo temperatures (in the case of refrigerated units, or reefers). Additionally, integrating software will allow this data to feed enterprise resource planning (ERP) systems for such applications as time and attendance, payroll, accounts payable, inventory and materials management. All of this information creates intelligence that can be presented on an operations dashboard in real time.
Construction Sites
Requiring fabricators to tag components at their factories before shipping the parts to construction sites allows the automated capture of tagged items’ data upon delivery. This saves an enormous amount of labor at the construction site to ensure accurate goods receipt supporting the construction schedule. Such automation reduces or eliminates the need for personnel to manually interrogate every component’s bar-code label.
By installing an RFID reader within a truck, a company can locate assets fitted with active UHF RFID tags in large storage areas or laydown yards, simply by driving though the site. Using active UHF RFID tags can enable fast locationing, especially when assets are constantly being moved around a dynamic storage yard. Finding the correct asset at the right time is vital to operational efficiency (read: it saves hard dollars).
Active UHF RFID tags are also being used to monitor concrete’s curing temperatures and times. This technique is employed during large construction projects involving multiple sections or a floor of concrete, for which time is critical, not only for the proper curing of the concrete, but also for the overall project management and schedule. Not only does it help to know when the time is right to pour the next section, but it also enables a firm to monitor the concrete’s color and appearance when forms are removed to ensure consistency. New York City’s Freedom Tower is an example of a project for which each floor was monitored to ensure it was acceptable, and that the time was right to start the next pour and the next floor. This can shave weeks—or even months—off a construction schedule, saving millions of dollars.
Personnel Safety
Companies that conduct evacuation drills due to the nature of their operations require accurate, real-time information. Unfortunately, many are still using pen and paper, magnetic boards and other inaccurate recording methods to determine who is at which location onsite. While it is important to ensure personnel know what to do during a drill, the time lost in production operations is an expense that can and should be minimized dramatically.
In the event of an actual emergency, first-responders need to know who is safe and who is not. Moreover, it would save time and reduce the incidence of injuries if responders knew exactly where to go to find at-risk personnel.
The solution: automated muster stations. Personnel and all visitors can wear active tags, whether in the form of key fobs or wristbands, to report where they are, especially at muster stations. All individuals can thus be instantly identified, and those at risk can be pinpointed. Such a system can be employed to reduce the time needed to carry out periodic drills—typically lasting a half-hour or more—in 10 minutes or less. This is routinely done on oil rigs, where workers are tagged and can be directed via signage to appropriate muster stations or lifeboats. All the while, dashboards monitor what is happening and can be tracked by safety personnel at onshore or off-site locations. Accurate, real-time communication is critical to providing safety and efficiency.
Mobility
Recently, mobile readers of active RFID tags have been introduced into the ecosystem. Some are small enough to be plugged into a laptop, just like a USB memory stick. Another option is a battery-powered UHF RFID mobile reader that can be hung from a holster, with data transmitted to the PC or tablet via a Bluetooth connection. Using a Bluetooth-capable interrogator provides flexibility in operator use, especially in bad weather, in vehicles or in environments in which dangling wires are unacceptable, including those requiring i-SAFE or ATEX certification. Wireless mobile data capture provides a new level of efficiency when attempting to cover thousands of tags across large, open expanses.
Software Applications
RFID hardware can sense and deliver identification data, but the software can move and manage relevant information in the context of the application, creating actionable intelligence. Having software collect the RFID reads, monitor reader performance and provide certain alerts is the foundation. Above this is the need to feed data into other modules and the “cloud” that can analyze and present the proper data at the right time, with a user interface that makes sense of it all and then presents the information in a form that drives relevant and timely decision-making.
Customers are demanding application-specific, cloud-based integrated software solutions that can be fed by multiple data-capture devices, including active, passive, Wi-Fi, HF and low-frequency (LF) RFID technologies. Furthermore, automated systems not only provide analysis, trends and graphs, and issue alerts and alarms when necessary, but also offer predictive analytics that can be used to anticipate future needs and potential problems. The “predictive actioning” takes us to the next dimension for operational decision-making.
Real-Time Location Systems
For the past few years, there has been growing adoption of real-time location system (RTLS) technologies by hospitals to track and monitor medical equipment. In the future, this will expand to include the tracking of clinicians, patients and other personnel, to aid in managing all hospital resources.
Recently, Apple has endorsed the use of iBeacons, which will proliferate in retail applications. Smartphones provide GPS and location data with hundreds of thousands of apps. Rugged tablets have achieved ubiquitous use, even supplanting PCs in many cases. The industry will see a new wave combining tablets and smartphones with battery- and/or USB-powered RFID readers with Bluetooth capability that provides valuable real-time visibility. We will increasingly want to know where assets and people are located, even while both may be on the move.
The Internet of Things, Clouds and RTST
All data captured from reading a myriad of devices using various wireless technologies will feed Internet-accessible clouds and bring to reality the Internet of Things, in which everything becomes connected and visible. This allows for what I call the RTST—or “Real Time Status of Things”—into the fold. Yes, we want to know where stuff is, but we also want to know the status of our stuff: location, security, temperature, humidity, motion and more. Where is it, where is it going and what condition is it in? And we want it all accessible from tablets, smartphones and future devices that aid in mobility and ease of use. Even more, we need geo-independent access, especially if the Internet goes down for any reason. Companies require an integrated and distributed computing infrastructure that allows secure access from anywhere in the world at any time, without having to log into their own ERP or corporate network.
Frost & Sullivan defines a smart product as an “intelligent sensing technology that is increasingly being integrated with Internet technologies, thereby allowing the product to react to and communicate with the changing environment around it. This leads to optimal operations and improvement in efficiency.”
Yes, wireless devices will multiply and bring a new wave of creative thinking to how we solve problems. It is an exciting time for us all. Everything is becoming smart.
Smart thinking leads to transformations and the development of disruption for market advantage. So now is the time to make the “smart play.”
John Shoemaker has spent the past 25 years in the AIDC industry, functioning at the C-level for several technology companies offering wireless and sensor solutions. He is currently the executive VP at Identec Solutions Inc., a supplier of active UHF RFID technology for use in providing safety, productivity and efficiency within harsh environments.