Since mid-2010, Kerry Logistics, a Hong Kong-based third-party logistics company, has been using RFID at one of its facilities to track the camera products it packs and ships for Canon. Kerry Logistics makes sure all the correct camera components, accessories and warranties are packed into each product box, and that the right boxes are put in cases, placed on pallets and shipped to retail locations. The RFID system has removed some manual steps, cutting time in the kitting process and ensuring accuracy. It has also sped the process of verifying that each order is complete.
“The speed for capturing serial numbers has been enhanced around 70 percent,” says Wilson Lee, Kerry Logistics’ director of information technology. “The processing time has been shortened from 18 seconds to five seconds for scanning one carton, in which six items are packed.”
The RFID project is only in its first phase. Kerry Logistics has a number of other applications in mind, including extending the RFID system to Canon retail stores in Hong Kong, where the tagged products are shipped. Kerry Logistics drivers could use handheld readers to check the RFID tags on the cases as they disassemble the pallets. This would replace a bar-code system for verifying the order has been shipped and delivered, expediting the process and boosting accuracy.
The RFID deployment initiated by Kerry Logistics represents a small but growing trend among logistics providers, the link between manufacturers and retailers. In the past, manufacturers—under the gun of retailer mandates—asked their logistics companies to RFID-tag goods, says Drew Nathanson, director of operations for VDC Research, a technology research firm. Today, it’s the logistics companies approaching manufacturers and asking them to consider the benefits of RFID. They recognize the internal visibility RFID can provide, such as quicker and more accurate data, which can be used to lower labor costs. “It takes out manual steps that can lead to mistakes,” Nathanson says, “and then the logistics companies can pass all those benefits on to their customers.”
Some logistics companies are also leading an effort to collaborate with their customers, developing applications that are mutually beneficial. And as in manufacturing and other industries, logistics providers are using RFID to track returnable transport items (RTIs), and cargo containers and vehicles in yards or ports. In the near future, logistics providers that service food producers may be asked to adopt RFID temperature-tracking solutions, to help their customers comply with government regulations).
Meanwhile, many of the largest logistics firms—including DHL, Maersk Line and NYK Line—worked with manufacturers, retailers, industry groups and governments to provide global visibility throughout the supply chain. A multiphase pilot project, led by EPCglobal‘s Transportation and Logistics Services Industry Action Group (TLS IAG), tracked consumer items, including electronics, footwear and agricultural machinery, from the Port of Shanghai to the Port of Los Angeles. A key goal was to establish standards for sharing EPC RFID data among trucking, shipping and air cargo carriers, securely and in real time. The information could help logistics providers speed through customs, and thwart counterfeiting and theft, and visibility into the whereabouts of their goods could enable companies to make smart business decisions.
Collaboration
While Kerry Logistics uses RFID to improve its operations, it’s also forging a unique relationship with Canon. Kerry Logistics has tentative plans to attach RFID tags to the warranty paperwork included in the product packaging. That way, a Canon retail store employee could use a handheld reader at the point of purchase to collect the serial number encoded to the warranty tag, creating a registration record of each product. If the customer wanted to return the camera or have it repaired, the retailer or manufacturer could read the card’s tag to authenticate ownership.
This would mean faster access to sales and warranty data for Canon, and the information could be used to identify customers in the event of product recalls. “In the current stage of our pilot, which is just an initial phase, the benefit is limited to the kitting-line process, which benefits the logistics operator the most,” Lee says. “However, Canon also sees the coming potential opportunity on further applying the technology in delivery and post-sales service, such as warranty handling.”
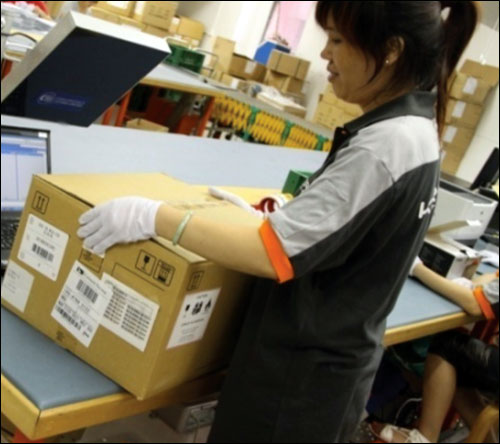
In fact, Lee says, Canon’s buy-in has been essential from the beginning. “It’s our initiative to drive this RFID implementation, and we’ve successfully sought Canon’s consent on doing this. It’s crucial to have a visionary and committed customer to partner with, in order to make such an implementation happen.”
Collaboration was also at the heart of an RFID system developed by Kuehne+Nagel, a global logistics provider, and Iveco, a maker of commercial vehicles. Kuehne+Nagel operates a parts distribution center for Iveco, in Turin, Italy, where orders must be filled quickly and often shipped overnight. Speed and accuracy are essential, so with the help of RFID solution provider Alfaproject, the companies codeveloped PARTS-iD, an RFID system used in the receipt, picking and shipping of automotive parts that pass through the facility and on to Iveco customers. The RFID system has reduced shipping errors by 70 percent and improved customer satisfaction, says Stefano Fantini, Iveco’s customer service supply-chain director.
Kuehne+Nagel and Iveco share both the benefits and the costs of the system. Kuehne+Nagel foots the bill for all fixed costs, such as reader networks, and Iveco pays for the tags used to track its products, Fantini says. The two firms are now expanding the RFID system to a DC in Spain.
Internal Benefits
Logistics providers have been using RFID to track the RTIs, such as containers, totes and pallets, they use to transport customers’ products. Tracking RTIs promises a fast return on investment, because it improves usage and reduces loss of these costly assets.
J.D. Smith & Sons, a Canadian logistics firm that offers freight and inventory management, is testing an RFID solution from startup Axios Mobile Assets to better track pallets and the goods loaded onto them. The system includes rugged yet lightweight pallets, made of bioresin, equipped with EPC Gen 2 passive tags. It provides visibility, so J.D. Smith can verify that the pallets are loaded onto the right trucks and determine when the empty pallets are returned. It can also send advance shipping notices and issue bills. In addition, the system comes with GPS and cellular communication technologies, allowing the company to track its trucks in real time and, perhaps, find more efficient routes, reducing fuel consumption and speeding deliveries.

“This is our first RFID project,” says Scott Smith, president of J.D. Smith, “but there are compelling aspects across the spectrum, from the low weight of the pallet [which lightens a truck’s load, saving fuel], to the trackability” and the ability to reduce emissions. In addition, some customers have expressed interest in leveraging the RFID tags embedded in the pallets for their own purposes. “We have clients that are looking at the challenges that RFID-enabled pallets could help them with—this includes a client in the food industry that wants to pair the tags with temperature sensors” to track the conditions of perishables in transit, Smith says.
Some logistics companies that manage large yards of containers and trailers have deployed RFID-based real-time location systems (RTLSs), to save on labor and improve efficiencies. BLG Logistics, a worldwide logistics firm, is deploying a pilot system involving passive EPC Gen 2 RFID and GPS technologies, to track the locations of rolltrailers at a seaport terminal it operates in Bremerhaven, Germany. The company says terminal personnel often spend excess time and burn fuel unnecessarily while attempting to locate a particular rolltrailer in the yard.
Since 2003, NYK Logistics, a Secaucus, N.J.-based logistics company, has relied on an RTLS from WhereNet to track every container, trailer and tractor in its 70-acre yard in Long Beach, Calif. The system allows the company to locate these assets and identify expected shipments, and it instructs yard workers where to move the containers upon receipt. And since 2005, NYK has been operating a similar system at its transportation facility in Norfolk, Va., where it serves its biggest retail client, Minneapolis-based Target. The system, which uses long-range active tags and readers that feed real-time location data into yard- management software, has allowed NYK to replace manual processes for checking in cargo and vehicle data each time a truck enters the yard, making the facility more efficient. It also cuts the amount of time trucks spend idling as drivers wait to be directed through the yard, reducing fuel consumption.
The Road Ahead
While some logistics companies are deploying and benefiting from RFID, the technology is not making major inroads in this sector. Companies that are tagging shipments as a service to clients under RFID mandates are not exploring other RFID applications. “Some logistics companies have found that offering RFID as an added service to their customers can be lucrative, but that provides revenue, not cost-saving benefits,” says Trevor Peirce, a supply-chain technology consultant and former global RFID program director at DHL Worldwide Network. RFID tag performance must improve before logistics companies across all sectors—or those that serve multiple sectors—will find the cost-benefit analysis attractive enough to deploy the technology for internal gain, he says.
In 2007, DHL Express, a division of logistics giant Deutsche Post World Net, decided not to transition from bar codes to RFID labels for tracking packages in bulk, because the 99 percent read performance was not high enough to usurp current business practices. But Deutsche Post DHL, which transports 5 percent of the global trade volume, uses the technology in a number of applications across its business lines. Since 2008, it has been RFID-tagging 1.3 million pallets of food products it ships annually for German retailer Metro Group. And it uses temperature-sensing RFID tags to track and monitor drugs for Swiss pharmaceuticals company Roche Diagnostics.
The cost of deploying RFID technology is a barrier for some logistics firms, but another, perhaps more important issue, is a lack of data interoperability, says Naotaka Ishizawa, senior technology officer with the technical strategy group at Monohakobi Technology Institute, NYK’s research and development arm, and cochair of the TLS IAG. The EPCglobal-led multiphase pilot project to track goods in the global supply chain uses active RFID technology and passive tags with Electronic Product Codes. The first three phases of the pilot yielded positive results overall, showing RFID could provide end-to-end visibility. EPCglobal issued specifications on how tags should be encoded and attached to goods, to ensure the tags could be read and the data shared easily over the EPC Information Services (EPCIS) platform.
But the scope of the project has been limited to items identified using GS1 data codes, around which the EPCIS platform was built. GS1 codes are used widely in retail and health care, but not all sectors or countries use the data standards. For the fourth and final phase, Ishizawa says, the goal is to develop a means by which data codes compliant with other standards systems can interoperate with EPCIS.
“Transportation and logistics companies have to connect with several different customers in many different sectors,” Ishizawa says. “But due to a lack of interoperability between data-coding schemes, it’s expensive to interface the different systems. From the point of view of a logistics provider, companies in the retail, health care, automotive and other sectors are all our customers. So we need a standard code that is interoperable over all different data standards.”
During an RFID Journal virtual event in September 2010, on the use of RFID in the auto industry, Michael Zehnpfennig, a project manager for DHL’s Solutions and Innovations division, echoed this sentiment. The auto industry’s Vehicle Identification Number (VIN), for example, is not a GS1 industry code that EPCIS recognizes. DHL is currently involved in a pilot program with BMW, in which it is shipping parts between suppliers and a BMW plant. But because the trading partners use different numbering schemes, DHL has to write multiple codes to the RFID tags and then juggle the different codes and formats in its software system. “It’s a difficult task,” Zehnpfennig, says, “and we would like to be able to handle all different kinds of codes [more easily].”
This year, Ishizawa says, the TLS IAG hopes to move closer to interoperability between EPCIS and the data standards used by multiple industry sectors. It plans to work with stakeholders in the logistics industry, standards bodies and members of the Asia-Pacific Economic Cooperation (APEC). Developing a means for data interoperability will open the door for the TLS IAG to complete the fourth and final phase of its global logistics pilot, which will involve logistics firms tracking cargo across many industries, using EPCIS to share information and provide visibility.
Moving Toward Safer Food
A shopper opens the door to the dairy case, reaches way back to find a cottage cheese container with a future “use-by” date and tosses it in the cart. “We all do it,” says Michael McCartney, principal of QLM Consulting, an RFID consulting firm for the food industry. “But just because that container says it has the longest shelf life, that doesn’t mean it does.” If the cottage cheese turns out to be sour, the shopper is likely to blame the grocer though the logistics provider could be at fault.
Growers, shippers and sellers of dairy, produce and other perishable foods have very little visibility into the conditions to which products are exposed during their journey from the source to the shelf. The temperatures inside refrigerated cargo containers vary, depending on location and loading patterns. Foods shipped at improper temperatures have shorter shelf lives and are susceptible to bacteria and viruses, which could cause illness and death.
Logistics firms and food producers have been testing whether temperature-tracking RFID solutions could improve supply-chain visibility and safety (see A Guide to Sensor-Equipped RFID Tags). Some growers have adopted the technology after seeing that it allows them to act on the data they collect and improve freshness. But logistics providers that service food producers appear to be in a holding pattern. C.H. Robinson Worldwide, for example, has partnered with growers to test temperature-tracking tags, but has not yet deployed the technology across its business.
Two developments could change that situation. On Jan. 4, 2011, President Obama signed the Food Safety Modernization Act (FSMA) into law, giving the U.S. Food and Drug Administration new powers to require food producers and shippers to follow safety-prevention guidelines and respond to recall requests. While it does not name RFID, FSMA does require producers to create electronic records that show food has been safely processed and transported. Sensor-equipped RFID tags can automatically collect and store temperature and/or humidity data, providing visibility into the environmental conditions to which perishables are exposed.
A larger and more reliable communication infrastructure could also lower an adoption hurdle, McCartney says. For temperature-tracking solutions to be most useful, the data collected must be available in real time to decision-makers, who can then take steps to correct a problem. If, for example, an RFID reader inside a truck driving through the desert detects a number of tags showing dangerously high temperatures in pallets filled with strawberries, it can trigger an alert to supply-chain managers in a central office, who can divert the truck to a facility where the problem can be addressed. But that requires a reliable communication link between the reader and that central office. Logistics companies once had to rely on expensive satellite networks to ensure packets of data could be transmitted from anywhere, coast to coast. Today, this data can be sent over cellular networks, which provide coverage even in remote areas of the country, McCartney says.
Growers and processors might ask their logistics partners to adopt RFID temperature-tracking solutions, to ensure compliance with FSMA. And retail customers looking to extend shelf life and ensure customer satisfaction might make the same requests of their logistics providers.