Imagine an industrial manufacturing environment in which inventory, materials, vendors and equipment constantly communicate to optimize operating efficiency. This environment is reality through the Industrial Internet of Things (IIoT), which integrates information technology infrastructure with operations technology to create smart factories. Insights from inventory levels, operation performance over time and vendor coordination can dramatically improve a factory’s operating efficiency.
There are several ways the IIoT enables the intelligent factory, including through radio frequency identification (RFID) and Near Field Communication (NFC) technologies. However, before exploring those, it is worth reviewing the characteristics that differentiate a smart factory from a traditional one.
Benefits of the Smart Factory
The IIoT is driving the adoption rate of connected devices in industrial manufacturing due to its many advantages. The first layer is the historical gains manufacturers realize from using artificial intelligence (AI) and machine learning (ML) as part of their process:
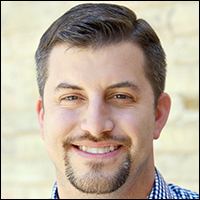
Adam Kimmel
Improved Inventory Control: Insights can help companies manage supply/excess inventory ratio, a significant key performance indicator (KPI) for operations leaders that reduces order management and material handling costs.
Lower Production Cost Through Higher Overall Equipment Effectiveness (OEE): Using collected data and AI, the intelligent factory adjusts production flow to maximize uptime, identify patterns and predict demand variations. This approach also optimizes assets for improved production and energy efficiencies.
Improved Quality and Lower Scrap: Collecting significant amounts of data during production gives operators insight into equipment lifecycles. This view enables them to uncover trends in tool wear and predict the next likely point of failure, to reduce both repair cost and downtime to execute it.
With these three improvements, the IIoT can enable decentralization to add supply resilience without the inefficiencies observed through the recent supply shockwaves. In addition, this approach enables companies to work with new supply partners that can quickly gain expertise on a new-to-the-manufacturer technology or process.
RFID and NFC Make the Factory Smart
RFID creates unique, serialized identification of connected equipment for error-proof data transfer. This “digital fingerprint” can improve inventory management by rapidly assessing existing supply and triggering a restocking order automatically. Inventory managers assign thresholds and order quantities that dictate when and how much the order software should request.
RFID’s unique identification tag can also track assets anywhere, alerting procurement and supply chain team members of an issue in shipment. In addition, it can follow transit steps and time between them to help logistics optimize component routing, reducing lead time and potentially inventory levels.
Smart factories combine digital information and physical assets to extend manufacturing capabilities. The data exists already, so the challenge in optimizing benefit is to collect and transmit the communication between entities in both directions. Bi-directional information flow offers a substantial advantage over traditional barcodes or QR codes, creating a critical feedback loop.
NFC, a subset of RFID, does just that. It converts the component or subassembly into a communication tool, indicating its current production stage to operators through an active scan. This advantage can reduce the need for mid-process checks that create inefficiency while helping to identify a failure through data history. While not passive, NFC tags can provide data from inside a machine with a “tap-and-go” from the user. It can communicate data from pressure, humidity, temperature, vibration, usage and condition history.
Another advantage of NFC is that it instantly connects a failure’s location to a machine, thereby alerting the operator to the issue. Assuming the factory has redundant equipment, the software can route subsequent parts to another device to maintain production output while the team repairs the broken mechanism.
Collecting data enables AI to deliver these benefits for the smart factory, and RFID ensures the system uses the data correctly. Proper knowledge and control of climate and asset health conditions can increase an asset’s uptime and lifetime.
While businesses must always overcome challenges when implementing a disruptive shift to an industry, manufacturing is sprinting into Industry 4.0 by the near-universal adoption of the IIoT. As a result, manufacturers can realize optimized inventory, lower operating costs and higher quality through accurate data about a component’s location, condition or history. RFID and NFC technologies are bringing these insights to the shop floor, enhancing the supply chain functions and plant operating efficiency.
The IIoT is propelling the move toward a standardized, decentralized and connected supply chain. RFID and NFC enable this rapid progress to create an exciting inflection point for industrial manufacturing.
Adam Kimmel has nearly 20 years as a practicing engineer, R&D manager and engineering content writer, and he submitted this article on behalf of Mouser Electronics. He creates white papers, website copy, case studies and blog posts in vertical markets including automotive, industrial/manufacturing, technology and electronics. Adam has degrees in chemical and mechanical engineering, and he’s the founder and principal at ASK Consulting Solutions, an engineering and technology content writing firm.