The COVID-19 pandemic that arose this year presents tremendous economic and organizational challenges for companies. In order to achieve a continuous containment and flattening of the virus curve, strict protective measures must be implemented at a global level to prevent further infections in the long term.
In this context, companies were the first to rely on distance rules, such as home offices, regulations on maintaining a safe distance and the use of breathing masks. However, not every business sector, such as logistics, production, hospitals, labs or office building in general, can be set to work from home. Processes on the production lines or in the working environment must be redesigned so that people can move around with sufficient distance.
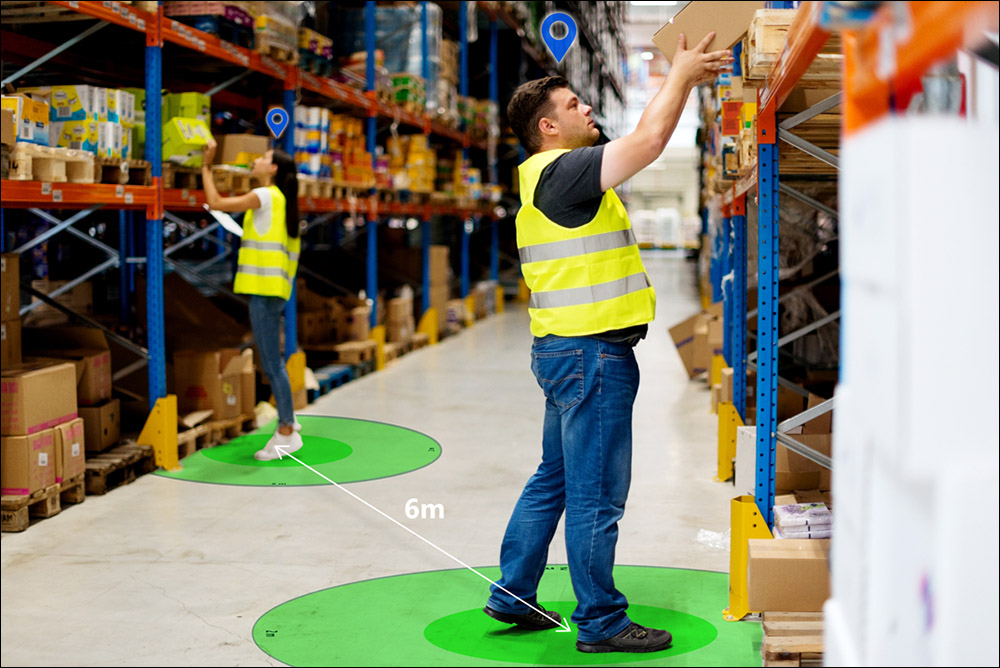
Social distance management
Digital Twins as a Key Role for COVID-19 Protection
Sustainable and secure digital solutions are already available, using precise but comparatively cost-effective, market-proven real-time location system platforms. These are primarily used for accurate indoor and outdoor positioning for optimization and automation of logistics and production processes, such as the automatic identification of production goods, semi-finished products and transport within supply chains.
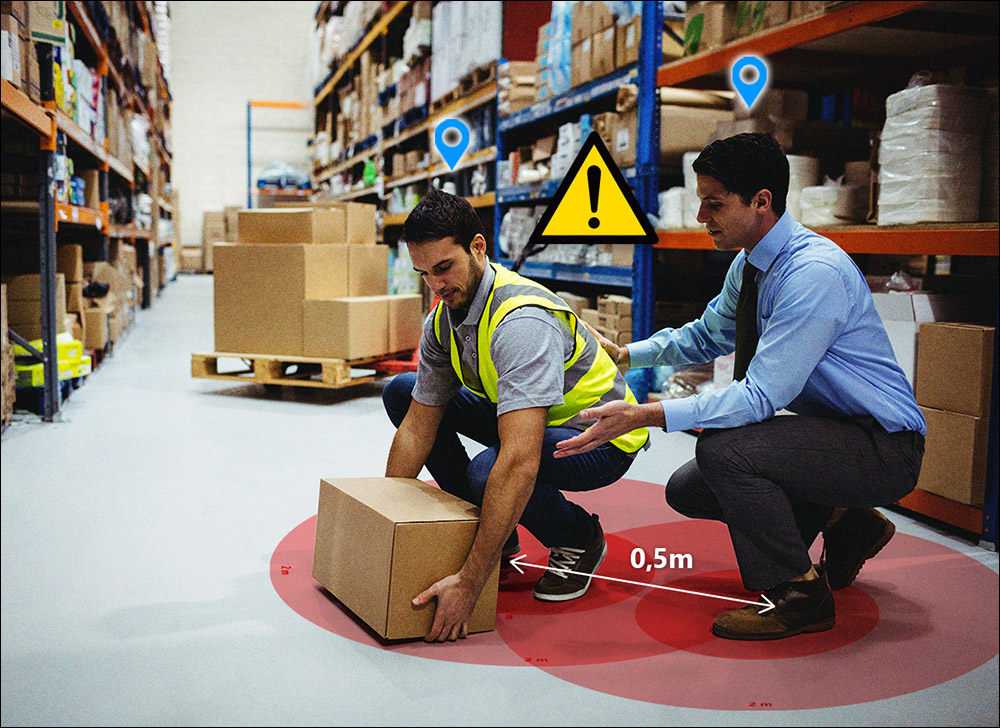
COVID-19: Control warning system of people safety distance
Social distance management apps specially developed by IoT RTLS platform providers enable companies to automate and control compliance by keeping a safe distance of 1.5 to 2 meters (4.9 to 6.6 feet) for their employees. Artificial intelligence (AI) algorithms generate precise location data from simple radio signals, which can then be used to generate distance information for safe distance in the form of a virtual protection zone or “geofence” to minimize the risk of infection transmission. The established personal-protection zone warns employees optically and acoustically by means of light-weight wearables (wristbands or lanyards) before the safety distance is undercut.
Apps equipped with the location technology also have other necessary safety functions:
- Tracing chains of infection: The location and contact zones of COVID-19-infected persons can be traced and identified, and these can then be blocked for all other employees. People who have had contact with a sick person’s areas can be notified to take additional protective measures.
- Contact reduction: Avoidance of crowds can be accomplished, as well as the specification or proposal of individual routes.
- Anti-cyclical employee traffic: Avoidance of crowds caused by peak times becomes possible, and Internet of Things (IoT)-based apps can control passenger movements counter-cyclically. Warning area traffic lights can also help to visualize the danger level of the respective area.
- Avoiding risk groups and protecting at the same time: Employees who belong to a risk group can be actively marked, and unnecessary contact can thus be avoided. An immediate quarantine zone can also be created to isolate sick people and keep healthy individuals at a distance.
- Detection of contaminated tools and materials: Working materials of infected persons can be detected and blocked by a protective radius.
- Keyless entry: Through open interfaces, such a platform can be coupled to opening systems, in order to open, adjust or convert doors, gates and workstation equipment automatically and contact-free.
- “Out into the fresh air at a distance”: Similar to a smartwatch, employees can be given a recommendation to go out into the fresh air and stay there for some time. This is done countercyclically so as not to create crowds of people.
- Observing hygiene regulations: Such apps could provide regular advice on how to comply with hygiene regulations, if desired.
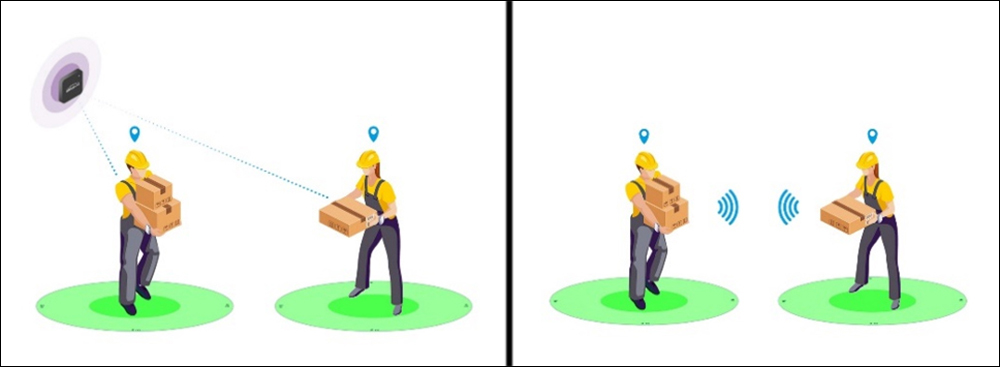
IoT RTLS platforms with UWB real-time location technology enable security zones for employees.
UWB as the Preferred Smart Distance Technology
In the containment of the COVID-19 pandemic, distance accuracy is the top priority, as any shortfall could have consequences. For this reason, the stable ultra-wideband technology is increasingly being used, as it already has a clear advantage over other positioning technologies such as WLAN or Bluetooth, it does not interfere with other technologies and it provides position data with an accuracy of up to ±10 centimeters (±4 inches). Compared to WLAN or GPS, the positioning accuracy is up to 150 times more precise—15 meters to 10 centimeters (49 feet to 4 inches). Even Bluetooth is still too imprecise with 3-meter (9.8-foot) accuracy.
Data Protection Plays a Major Role Due to Digital COVID-19 Solutions
Digital twin technology can help to ensure data conformity and the strict protection of employee data. Location data is generated anonymously and has no ties to specific individuals or personal data. Such software behaves like an encapsulated system, only issuing a warning in case a distance threshold has been reached. Third parties have no access. Only an end user decides how and for what purpose its data will be used.
Fast and Immediate Deployment: Companies Should Not Waste Time
The big advantage of these solutions is that social distance management apps are vastly scalable and are ready to use within a few days. The prerequisite is the installation of RTLS access points in the areas to be monitored, as well as the equipping of employees with UWB-based tags (wearables) and the installation of an IoT RTLS platform. Some RTLS companies already provide such apps to new and existing customers free of charge out of solidarity.
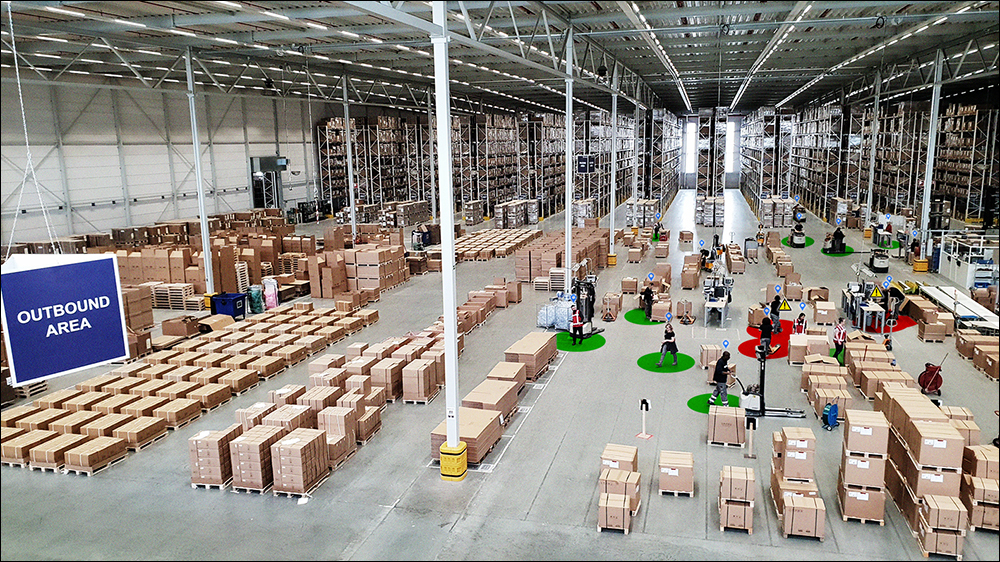
Social distance management in warehouses enable ongoing business processes.
Back to Normality
Employee-safety solutions enable the immediate start of work and ongoing business processes. Professional, reliable and data safety-compliant distance control through an integrated warning system enables the reduction of new infections, as well as efficient COVID-19 management. This enables a quick re-entry and the start of logistics, production and other company processes in compliance with the prescribed hygiene measures.
Images provided courtesy of INTRANAV.
Madlen Schuster is the digital marketing manager of real-time location system software platform (RTLS IoT) at INTRANAV, based in Frankfurt, Germany. The RTLS company, is, with its digital twin, the enabler technology for smart factories and Industry 4.0. With the digitization of precise positioning data of people, industrial assets and the automation of logistics and production processes, INTRANAV’s RTLS IoT platform contributes to a significant increase in efficiency.
Ersan Günes is the cofounder and managing director of INTRANAV. He is responsible for the company’s vision and product. Günes studied electrical engineering and computer science at the University of Darmstadt in Germany and founded INTRANAV seven years ago. He has strong industrial expertise in the field of real-time locating systems and IoT for industrial automation and optimization. Günes has implemented more than 50 IoT projects in the production and logistics industry throughout the past few years.