As digital technology expands throughout manufacturing, there are many new tools available. Barcodes and RFID are some of these tools, and they can be integrated into many portions of your workflow. With the use of barcodes and RFID, an operation can improve many aspects of its maintenance program. Documents can be moved to a digital platform, and the whole workflow of a maintenance issue can be made more efficient. Issues can be reported more easily, breakdowns and replacement parts can be found much faster, and safety can be improved. These enhancements will help your maintenance staff work smarter and faster.
Digital Documentation and Recordkeeping
One benefit of barcodes is less manual documentation. With barcode technology deployed on equipment assets, a technician can utilize digital tools to help make his or her job easier.
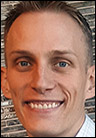
Imagine this scenario: a maintenance technician receives a call about a breakdown. He goes out to the shop floor with a scanner and tablet. The equipment barcode is scanned, and the technician has all the information about the asset at his fingertips. He can look through the last failures, the equipment manual, the work instructions and so on. No more digging is required through file cabinets or stacks of paper.
When the technician has finished his job, he can make notes right away—not at the end of his shift. The time tracking can be automated and give a true sense of the actual time he spent on the job. Improvements in data quality help the business make intelligent decisions about its assets.
Of course, this benefit requires the use of an effective computerized maintenance management system (CMMS), which would need to be integrated into the equipment and work practices. For example, a utility service company called Hofor started using RFID technology to track water line maintenance. The technicians went from maintaining a binder to scanning valve caps and accessing history through software. By using this software, they could find the history of the valve and ensure they were performing the proper maintenance on the correct valve. Hofor estimates a 40 percent time reduction for data collection during water line maintenance.
Reporting Problems
In the event of a problem, you will want to report it quickly and effectively. This is much easier with barcodes on equipment. Using mobile maintenance software, an authorized operator can report a problem simply by scanning a barcode and filling out a simple work request. This method leads to efficient handling of equipment issues and empowers front line personnel to keep the operation running smoothly.
Equipment Location
In a large manufacturing operation, it can be difficult to find the right piece of equipment to work on. Oil refineries can have thousands of valves, traps and gaskets; and in many cases, it is difficult to determine where a problem is originating. By using RFID technology on equipment, a technician can be sure he is starting on the correct valve. This is particularly useful for preventive or periodic maintenance tasks.
Parts Location
For anyone who has worked in an aging factory, finding the location of an exotic part can be a maddening task. By converting parts storage to RFID, the operation can quickly locate a needed part. And by using barcodes, technicians can ensure they are grabbing the correct part the first time. These improvements can save an operation from wasting time having employees roam around the site and rummaging through parts areas, or having to make multiple trips to the same area.
Personnel Safety
Digital location technology can also be used to locate personnel onsite. This can be useful in many hazardous scenarios, and with contractors who may not realize every rule. Give them an RFID badge which tracks their movement, and if they enter an unauthorized area, an alert can be delivered to site security or safety.
The benefits of integrating barcodes and RFID technology are significant for manufacturing. There are numerous reasons to embrace the potential of these solutions—from faster maintenance mobilization to speedier completion of repairs, to better inventory control, and even improved safety.
Bryan Christiansen is the founder and CEO at Limble CMMS. Limble is a modern, easy-to-use mobile CMMS software that takes the stress and chaos out of maintenance by helping managers organize, automate and streamline their maintenance operations.