In the wake of the Sept. 11, 2001, terrorist attacks, the international chemical industry came under a great deal of scrutiny from lawmakers, public advocates and citizens who live near chemical plants and transportation routes. The attacks brought out the need to better track the estimated $1.7 trillion worth of chemicals that are traded worldwide each year.
These chemicals are transported in a variety of containers—from bottles, plastic totes and gas cylinders to 55-gallon drums, cargo containers and tanks. The containers travel around the globe aboard ships and then wind their way through cities and towns onboard trains and trucks. Most often, the chemicals are destined for a variety of manufacturing purposes, to help clean up drinking water and produce pharmaceuticals, fertilizers, reliable energy sources, home-building products, synthetic fabrics and so on.
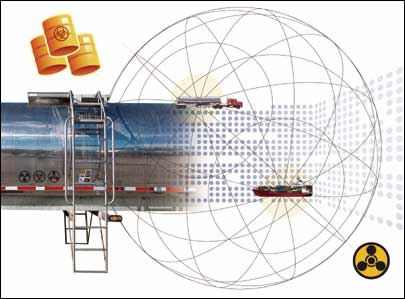
For years, chemical companies have tried to develop systems for tracking chemicals to manage inventory better and ensure that hazardous substances were not either accidentally or intentionally used incorrectly, lost, stolen or leaked. Union Carbide‘s tragic gas leak in Bhopal, India, 20 years ago, which left thousands dead, still looms vividly in corporate psyches.
The most popular chemical-tracking system to date has been bar coding containers. But many in the industry say that none of the methods has given companies an accurate accounting of where shipments are, what they contain and whether empty containers have been cleaned and inspected. Some chemical companies in Europe, the United States and Asia have started to test or deploy RFID applications as a possible solution to safety, security and tracking needs because the technology is less labor intensive than bar coding and the tags can be programmed to carry more information.
“In chemicals, the biggest issue is safety and security,” says Collin Masson, research director for chemical and process manufacturing at AMR Research. “There’s a brand problem if it’s your facility that gets targeted if it didn’t have the right security.”
Yet, chemical companies have been slow to adopt RFID. A recent AMR survey of executives found that 18 percent of chemical companies have an RFID pilot under way and 9 percent are planning to implement RFID solutions this year. Another 18 percent plan to evaluate the technology in 2006. Masson says that one reason adoption has not been as rapid as in other industries—such as consumer packaged goods, in which the survey found 39 percent of companies interviewed are either already piloting or deploying RFID—is because the chemicals industry has been less affected by mandates. Whereas CPG manufacturers are responding to retailer mandates in the United States, the only chemical companies subjected to mandates are those that supply products, such as paint, fertilizer and motor oil, to retailers or do business with the U.S. Department of Defense.
Despite slower adoption rates, many major chemical manufacturers—in addition to companies that use chemicals and transport them—are starting to test or deploy RFID. These companies see RFID as a tool not only to improve security but also to realize other business goals, such as improving demand forecasting, product replenishment and asset management.
DuPont, the world’s fourth largest chemical company, based in Wilmington, Del., is evaluating RFID applications to track truck traffic at its transportation depots. Dow Chemical, the world’s second largest chemical maker, based in Midland, Mich., is testing a combination of RFID and GPS to track chemical transport via truck, rail and ship. Dow is also using the technology for container tracking, product applications, and product tracking and replenishment for customers such as Wal-Mart, to which the company ships an assortment of consumer products.
“One of our current challenges is to prioritize our many opportunities in terms of which ones are most likely to bring the greatest value to our customers as well as to Dow,” says Paula Tolliver, who is leading Dow’s RFID steering team. “RFID and GPS are not silver bullets—perfect solutions on their own. But when thoughtfully integrated into the larger processes and systems that govern the manufacture of product and manage the safe and timely delivery to our customers, these technologies can bring great value.”
Improving Security
As terrorists have repeatedly used the developed world’s transportation systems to cause death and destruction, the looming question is whether fanatics will next target the chemical sector—a critical infrastructure—for sabotage, theft or attack. In 2002, Tom Ridge, who was then secretary of the U.S. Department of Homeland Security, testified before Congress that chemical targets were in the sights of terrorists and that was of concern because there were “security deficiencies at dozens and dozens” of chemical facilities. The chemical supply chain has also been under scrutiny, due to the fear that some of the 19 million cargo containers that enter the United States each year through land borders, airports and seaports could be used to transport chemical, biological or even nuclear weapons.
The focus on securing chemical facilities and transportation routes has led U.S. chemical companies to spend more than $2 billion since the terrorist attacks to enhance security, according to the American Chemistry Council, which represents the leading companies in the $460 billion domestic industry. All 130 ACC members agreed to the Responsible Care Security Code, completing vulnerability assessments and security upgrades at some 2,040 facilities, including physical and information security improvements. As part of this voluntary initiative, a number of chemical companies started putting in place or testing RFID solutions to help them better track containers—and, in some circumstances, trucks, pallets, cases and employees—to gain more visibility into the international supply chain of chemicals.
In Europe, regulators took a different approach. The European Commission proposed a law calling for the registration, evaluation and authorization of all chemicals sold on the continent and requiring companies to regularly perform security vulnerability assessments. Last September, even the Russian government announced it was setting up a governmental commission to review biological and chemical security “in the light of recent events.”
Bayer AG, the world’s third largest chemical company, based in Leverkusen, Germany, has issued RFID-enabled ID cards to 70,000 employees in its three Rhineland plants—Leverkusen, Dormagen and Krefeld-Uerdingen. The company says it meets the recommendation of the German Störfallkommission (Disruption of Plant Operations Commission), which published guidelines for improving plant security after the U.S. terrorist attacks in 2001.
RFID-enabled IDs cards not only optimize site security but also keep employees safe. “Some of the gases and chemicals are pretty nasty, and people in the chemical plants need to know which employees are authorized to enter certain areas,” says Naresh Milak, a partner with IBM Global Services. “If there is an incident or event, you need to be able to track your employees very quickly.”
Perhaps the most immediate source of return on investment for chemical companies deploying RFID involves keeping tabs on another valuable and hard-to-track asset: the containers themselves. Bayer and other companies are testing RFID tagging of reusable containers, which can be quite expensive. Cylinders that hold industrial gases used for medical and manufacturing purposes, such as oxygen or nitrous oxide, range from $400 to $500 apiece. Fifty-five-gallon steel drums, which can hold solvents or hazardous materials, can cost up to $800 each. Large metal cargo containers, filled with such products as paints and sealants, run from $4,000 to $10,000, with higher prices for boxes that contain refrigerators to cool chemicals or agitators to keep chemicals moving en route.
The tracking of most types of chemical containers is poor and labor intensive because data collection is mostly done manually. In addition, companies order chemicals for quick delivery, which doesn’t give manufacturers a lot of time to check around the yard for available containers that have been cleaned and are up-to-date on federally mandated inspections. The result: Most chemical companies buy hundreds if not thousands more containers than they actually need just to have them on hand when orders come in. Joseph Tobolski, associate partner at Accenture’s Technology Labs, says that the problem of tanks, containers, drums and cylinders getting lost or stolen “could cost millions of dollars a year.”
Back in 1998, Air Liquide, the Paris-based industrial gas conglomerate that has 130 subsidiaries in more than 70 countries, started applying RFID tags to its cylinders at its production facilities in Louisiana and Texas. The cylinders are used to supply oxygen, nitrogen, hydrogen and many other gases to a variety of industries, including oil refineries, hospitals and paper manufacturers. “For years and years, since the birth of the industrial gas business, people have been trying to come up with a cylinder-tracking system that worked,” says Albert Atkins, project manager for Air Liquide in the United States. “Lots of systems have been tried without ever finding the right one.”
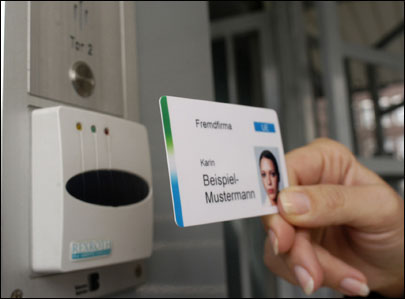
Atkins says RFID is a better option than most because more data can be stored on the tag, such as contents, expiration date and when the cylinder was inspected. Since the company deployed the system, customers who want to adopt RFID tagging to track cylinders are using it increasingly. That’s created so much additional data that Air Liquide needs to upgrade its underlying software system. During the transition to the new software, the company will replace RFID tracking with bar code tracking, but Atkins says the company foresees a migration to an updated RFID system in the future.
Some third parties that supply containers for rental purposes have also started tracking these assets. One example is pH Europe, a Huddersfield, England, container supplier that has an active RFID tag on each of its reusable 1,000-liter stainless steel chemical containers. “When the containers are in our warehouse, we know how many of them we have in stock,” says Ivelina Ivanova, pH Europe’s RFID project manager. “We know precisely when a container was returned, so that we can automatically calculate the charge [to bill the customer].” The RFID system also minimizes labor in the warehouse because inventories and data collection on returned containers is gathered automatically.
Managing Inventory
For manufacturers that use chemicals in their business, RFID tracking of the location and movement of the chemical products at their facilities can help improve security and safety while also providing visibility into inventory. IBM has been piloting RFID tracking of chemicals it uses in chip production. The company has placed tags on cylinders, drums, plastic carriers and bottles within its semiconductor chip manufacturing plants in Fishkill, N.Y., and Burlington, Vt. IBM is using dual-label RFID tracking for movement and bar codes for achieving a positive match between the container and the location where it will be used. The system has an alarm that will alert security if a container is removed from one location and fails to arrive at its destination within a certain amount of time.
IBM thinks that RFID will help the company exceed environmental and safety regulations, but it also has financial reasons for tracking chemicals. Some of the materials used in chip production cost as much as $5,000 to $10,000 per gallon, such as chemicals for photo etching on microchips. Real-time visibility into inventory would allow the company to more efficiently order these and other chemical supplies. IBM has been talking to its suppliers about expanding the RFID pilot to better manage inventory through the supply chain.
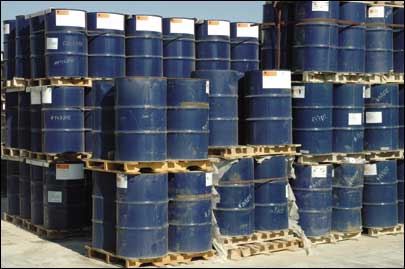
Supply chain inefficiency is one of the main operational challenges leaders across industries are trying to address with RFID, according to the 2005 AMR survey. Once chemical manufacturers have more visibility in their supply chain, knowing exactly what stocks of what chemicals are en route in ships or already waiting at ports, they can better fulfill customer needs in a timely fashion.
Complying With Mandates
The chemical industry is a big supplier to manufacturers of such things as consumer products, pharmaceuticals, automobiles, building supplies and paper. But some chemical products also wind up on the shelves of Wal-Mart and other retail chains that have asked their suppliers to start RFID tagging pallets and cases. As more retail chains—especially stores such as Home Depot or Lowe’s—adopt RFID as a way to streamline their supply chains, more chemical companies will be impacted by RFID mandates, says AMR’s Masson.
BP, which owns the Castrol brand of motor oils, volunteered to comply with Wal-Mart’s RFID tagging initiative for pallets and cases. BP partnered with IBM Global Services to develop a system of automatically applying RFID tags to each case of Castrol motor oil as it is made and packaged. Those cases are sorted onto pallets, which are also tagged to identify the pallet and its contents. Tagged cases and pallets are read at dock doors and in warehouses, both at Castrol plants and Wal-Mart distribution centers and stores.
BP estimates that it can save more than $1 million per year by using RFID to reduce chargebacks and shipping errors. The company also expects that RFID tagging will allow it to reduce inventory requirements.
The DOD is also a consumer of chemical supplies and has issued its own mandates to suppliers for putting RFID tags on shipments, which is helping to push some chemical companies into launching RFID trials. While DOD mandates started going into effect earlier this year, most manufacturers of packaged chemical products will not be required to tag cases and pallets until 2006. Bulk commodities—those shipped in railroad cars, by tanker trucks or by pipeline—will not be covered under the DOD mandate; these include petroleum and other liquid chemicals and any agricultural products, according to a spokesperson for the Department of Defense.
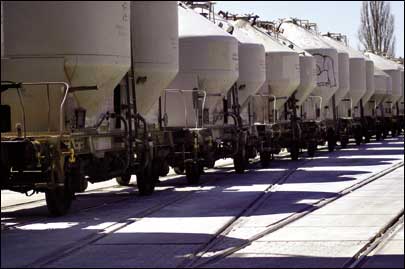
Moving Slowly
Despite the compelling potential of RFID to improve supply chain efficiency, inventory management, and ultimately safety and security, the chemical industry has been slow in adopting the technology. Industry sources say companies are waiting for the technology to mature and looking for a return on investment above and beyond ensuring security. (While deploying RFID in the chemical supply chain would require a significant investment, the chemical industry is booming, according to Chemical & Engineering News magazine.)
Another reason RFID adoption is slow is that there is no security mandate for change. The chemical industry in the United States is advocating for a watered-down version of chemical security legislation that would codify some of the voluntary initiatives its members have already undertaken.
Analysts say it is unlikely that the U.S. government will mandate the use of RFID in the chemical sector—even in the event of a catastrophic accident or terrorist attack. “It could be expected that the reaction to a major breach in security of the chemical supply chain by terrorists would not result in a broad mandated use of RFID, but could result in regulated real-time tracking and secured access of selected hazardous materials and facilities, that would extend existing voluntary and legal reporting requirements in the chemical, oil and gas, pharma and food industries,” says AMR’s Masson. “As always, national security comes at a price, and the cost of RFID deployment would have to be weighed against the potential improvement in securing supply chains.”
A Chemical Solution: Sensors and RFID
The chemical industry has been using sensors—devices that respond to physical stimuli and produce electronic signals—to keep chemicals at optimal temperatures, monitor vibrations of containers holding volatile chemicals and detect motion in a secure room for hazardous chemicals. Now it’s starting to combine sensors and RFID technology to improve the management, security and safety of potentially hazardous materials.
NASA’s Dryden Flight Research Center in Edwards, Calif., has deployed RFID and sensors on smart (RFID-enabled) shelves to make sure chemicals that react with each other—such as acids and bases—are not stored close together. In addition, employees wear RFID badges encoded with the names of whichever chemicals they are allowed to have access to, providing additional security and safety.
The flight center pioneered a program last year using RFID tags and interrogators, in conjunction with temperature and motion sensors, to track the location, handling and condition of chemicals at the facility. The setup provides real-time data to Dryden’s Web-based hazardous materials management system, boosting security and reducing labor costs.
Dryden researchers have launched a second phase of the program to see if the combined technology can help first responders to an accident or terrorist attack at a chemical facility. They are testing whether an unmanned aerial vehicle equipped with RFID tags and sensors could identify chemicals and other conditions, such as temperature readings.
“Our idea is when something goes wrong—whether at the chemical plant, while in transit or as a result of terrorist activity—it might be so bad we wouldn’t want to send people in to do a reconciliation of what would go on,” says Ralph Anton, chemical program manager at Dryden. “We would send it [the unmanned aerial vehicle] into a hazardous area to download sensor data and coordinate that with the database in order to help the emergency responders.”
Naresh Malik, a partner specializing in RFID at IBM Global Services, says most of his company’s clients in the chemical industry and related fields are implementing RFID pilots. He believes that, over time, they will be interested in testing RFID tags with built-in sensors to monitor temperature, pressure and vibrations, among other conditions. “This is the next step forward,” Malik says, “to use RFID tags not just in identification but in sensing additional information.”