Back in 2003, when Walmart first asked its top suppliers to tag pallets and cases, consumer packaged goods companies had a lot of questions. What tags do we use? Where do we place them? How do we know the tags will be read in a Walmart facility? This gave rise to a considerable amount of testing in labs worldwide. The tests typically involved putting tags on cases of tomato soup, and reading the tags as they traveled along a conveyor.
The quality of passive ultrahigh-frequency tags and readers based on GS1‘s Electronic Product Code standard have improved a great deal—and so have testing procedures. Now, as more retailers are moving RFID-tagging of apparel and other items to the point of manufacture, suppliers are once again asking these questions. And the University of Arkansas’ RFID Research Center is prepared to answer them. But instead of testing tags for each supplier, the center has created the Arkansas Radio Compliance (ARC) program, which aims to qualify tags that will work in a specific retailer’s environment.
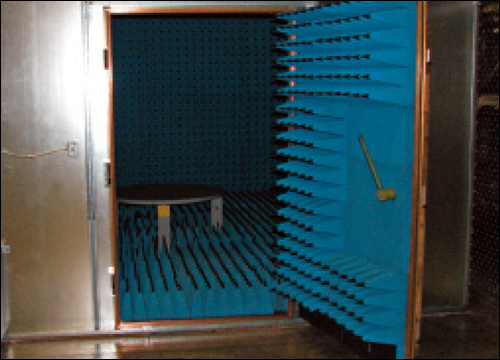
RFID Journal recently visited the center’s new 20,000-square-foot lab in Fayetteville, Ark., to view the testing being conducted for the ARC program. The program was launched in January 2011, at the request of retailers that wanted suppliers to be able to choose tags from a variety of approved vendors. The program qualifies tags that can be used by suppliers of a particular product category, so every supplier doesn’t have to recreate each retail partner’s store environment and test the tags.
The RFID Research Center set up a three-step process to qualify tags. First, the center’s researchers visit one or more of a retail chain’s stores to observe the environment in which the tags will be read. They tag a variety of products within a category the retailer wants to track with RFID, and they read those tags to understand the variables that affect RFID performance in that environment.
“The retailer has usually chosen its technology partners and has a clear idea of what they want to track,” says Justin Patton, director of the RFID Research Center. “We use the RFID readers they are planning to use—say, handhelds from a specific vendor—and we read the tags to understand how tags generally perform in that environment. Then we create a specification for the store use case. We can compare that spec to tags we tested back at the lab.” The specification might include the required sensitivity of the tags, the angles at which they’re positioned or the materials on which they’re placed. The center also provides this spec to tag vendors and suppliers.
Researchers then test the tags in the lab’s 12-foot by 12-foot anechoic chamber, which has steel walls and is lined with foam spikes that reduce radio wave reflections. The chamber is designed to filter out any potential interference and provide a controlled test environment.
The tags are tested on standard materials based on the category—denim for jeans, plastic for apparel that comes in polybags, and corrugate for flat-panel televisions and other large items packed in boxes, for instance. Tags are read from a variety of angles, based on how they will be read in a store. Testing a single tag can take several days.
The third step in the process is to take the tags that are likely to meet a retailer’s performance criteria back to the store, to verify that they will work the way the lab tests indicate they will work.
“A lot of people ask us how we can be sure the tags will work in a store when we are testing them in the anechoic chamber,” says David Cromhout, the center’s research director. “The answer is, we take a few types of control tags to the store and test them. Based on which of those passed and failed, we find the performance cutoffs. We know the chamber performance of those inlays, so we can make a spec, and quickly compare it against all of the others.”
The lab has tested 136 inlays from 18 manufacturers and collected 160,000 data points on each inlay (an inlay is an RFID transponder that has not been converted into a label or embedded in a hangtag). So far, 51 of the inlays submitted have been fully enrolled in the program.
Four retailers are involved with the ARC program today, and more than 75 retail suppliers rely on the program for tagging information. If a retailer adds a new product category—say, car batteries or smartphones—the center will create a specification and test tags from participating inlay manufacturers. In some cases, existing tags will work fine on new products. In other cases, tag makers will need to develop new designs in order to sell a tag that will meet a retailer’s needs.
“Since we share the specification with the participating tag manufacturers, they can easily create prototype tags, test them and confirm they will meet the retailer’s requirements before they mass-produce them,” Patton says.
The ARC program is beneficial to retailers, suppliers and tag manufacturers. A retailer can expand tagging to a new product category and have confidence that suppliers will be able to purchase tags from one or more tag manufacturers that can be read in its store environment. Suppliers can buy tags without having to do a lot of their own testing. And tag vendors can understand the requirements in a standard language and create tags they are sure will work for specific applications.
Why Tags Are Not Read in Retail Stores
Several retailers have asked the RFID Research Center to conduct audits in stores, to determine whether their RFID systems were working properly. They wanted to know, for instance, whether they read 100 percent of the tags when they did cycle counts.
The center sent a team to the stores to do manual counts and cycle counts with an RFID reader. They rarely found 100 percent of the tags were read. Below are the key reasons they found that tags were not read. The first two reasons relate to problems with the tag; the others are process issues that can be resolved with training.
• The tag was damaged and could not be read.
• The tag didn’t function due to a broken antenna or another issue.
• The manufacturer or supplier didn’t put a tag on the item.
• Two tags were placed on the same item.
• The tag was not encoded with an EPC.
• The tag was encoded but the EPC didn’t match the UPC.
• The tag was functioning but was not read during a cycle count.
• The tag fell off or was torn off by a customer.
• The tag was read but was not attached to an item.
• The tag was removed by a customer after purchase, and then the item was returned.