Office personnel at energy company Subsea 7 will be using the facility’s new digital-twin- and sensor-based technology to locate workers and prevent overcrowding in the firm’s lunchroom and meeting rooms this summer. As employees return to their desks in a phased approach, the company is leveraging cloud-based software provided by Empathic Building. The system was taken live in May.
Subsea 7, an offshore energy engineering, construction and services company, is one of multiple businesses deploying the visualization software solution to aid in workspace safety, says Gunnar Hansen, Empathic Building’s head of hospital solutions. For Subsea 7, the solution includes a gaming-style digital twin of the facility, cellular-based wireless motion sensors at each individual seat in the lunchroom, and temperature and humidity sensors deployed throughout the facility.
The company was using none of that technology three months ago, according to Jan Roger Moksnes, Subsea 7’s communications manager. On Mar. 12, the firm, along with many other organizations globally, sent employees to conduct their work from home in response to the global COVID-19 pandemic. “We had a couple of months working from home, and then needed to start working on a return-to-work plan,” Moksnes says. “Part of this plan was, of course, to ensure we would follow national authorities’ guidelines and restrictions, to ensure that people would feel safe and be safe when they returned.”
The company has two buildings on its campus (known as Campus1), with a combined footprint of 24,000 square meters (258,000 square feet). Prior to the pandemic, only one building was occupied, while the other was not being used. To bring employees back safely and within health guidelines, the firm opted to open up both for office personnel, with newly assigned desk areas to provide additional space between workers. By reassigning the locations of employees throughout both buildings, the company would enable them to maintain a 2-meter (6.6-foot) distance between them and their workspaces.
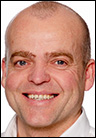
Gunnar Hansen
The rollout is being accomplished in a phased approach, Moksnes says. “What we quickly realized is that we wanted to move people back gradually,” he states, starting at 25 percent. At present, half of all workers are back in the office. Subsea 7 also set up a campaign dubbed #movinghomeofficetowork to help workers understand where they would be working and how their behavior might need to change. The company’s large touchscreens display data to ensure workers behave in a safe manner.
As part of this approach, Empathic Building brings visualization to what is happening in the office for workers and managers, both historically and in real time. Within three days, Hansen says, the firm created a digital twin of the facility in order to provide a model of the entire building, so that it could begin mapping out its strategy. The desks were arranged and numbered, and employees were entered into the system and assigned to locations where they may not have previously been seated.
With the Empathic Building software, workers can view not only their own desks, but also those of coworkers whom they might need to seek out, says Hans Olavesen, Subsea 7’s facility manager. Each employee can access information by signing into the cloud-based Empathic Building software. The system can display that individual’s workspace or enable him or her to request the location of a specific coworker’s desk. A person can also input information and create an avatar to help coworkers view his or her details. Staff members do not carry any sensors, and their locations are not tracked.
To ensure that the lunchroom never becomes overcrowded, the company assigned a scheduled lunchtime for to each floor, but it found this policy to be too rigid. “We quickly noticed that this wasn’t very efficient,” Olavesen recalls. “We wanted them to have more flexibility” regarding when they took a lunch break. Since the cafeteria has a maximum seating requirement, the company needed to provide employees with information about the room’s use at any given time so they could schedule breaks accordingly.
“We realized if we could use the Empathic Building [system],” Olavesen says, with sensors to detect the presence of coworkers in real time throughout the cafeteria, the staff could have more flexibility. When workers access the system and open the lunchroom display, the digital twin map of the cafeteria shows green, red and yellow dots indicating the status of each available dining seat. In that way, employees can view whether or not there is seating available before walking to the lunchroom. A large screen in front of the room’s entrance displays that same data.
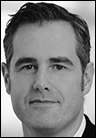
Roger Moksnes
A cellular-based motion-detection sensor is mounted under the table at each seat. When an individual takes a seat, the sensor detects his or her presence and forwards that status to the software, and the space is then illuminated as red. Once the individual leaves, the status turns yellow to alert the cleaning staff to clean that space. After a certain amount of time has passed, the icon turns green, indicating the room is available for use. The solution could also employ wireless sensors, such as Bluetooth Low Energy (BLE), to track more specific data regarding the movements of individuals, but Hansen says Subsea 7 did not require that functionality. “Empathic Building is a visualization tool,” he states. “We are agnostic to any sensor technology.”
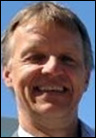
Hans Olavesen
In the long term, Empathic Building’s solution provides Subsea 7 with historical data. For instance, users can leverage the system to view how much each seat is being used, and to help them understand the flow of traffic through the space at different times of the day. The company plans to consider the long-term use of its space, and it expects to use the sensors to track the utilization of various parts of the building. “Maybe we need more space or less,” Olavesen says.
Temperature sensors deployed throughout the office space can measure luminance levels and other criteria, Hansen says, to indicate how the lighting has been used for the purpose of environmental analysis. Data is transmitted to a gateway via cellular connectivity once every minute. Subsea 7 has installed a few sensors in meeting rooms as well, to enable it to determine whether or not the rooms are occupied.
Initially, Olavesen says, the primary benefit will be better management of the lunch area. “It’s about safety, smoothness at lunch period,” he states. With regard to worker convenience, he adds, “They save the time they would have spent walking through the entire area” searching for a coworker’s desk or checking the lunchroom’s occupation. Other companies, including energy offshore business and hospitals, are employing the technology as well, Hansen reports, noting that the solution can locate assets using Bluetooth tags ultrawideband or other technology.
With the software, Moksnes says, Subsea 7 will be able to provide safety guidelines “so that as they go into the system, they can view information about spaces, such as occupancy maximum for a meeting room.” According to Hansen, the Empathic Building solution is designed to let facility managers adapt the development inhouse. “That’s a big cost savings,” he states.