East Coast Warehouse & Distribution (ECW), a provider of logistics services, has reduced labor costs and boosted productivity via a radio frequency identification solution that tracks the locations of more than 1,000 shipping containers throughout its 60-acre yard.
The solution, known as the Advanced Yard Management System, was provided by PINC Solutions and includes passive ultrahigh-frequency (UHF) RFID tags attached to containers, as well as RFID readers installed on yard trucks (switchers), and cloud-based yard-management software, says Rafael Granato, PINC’s marketing director.
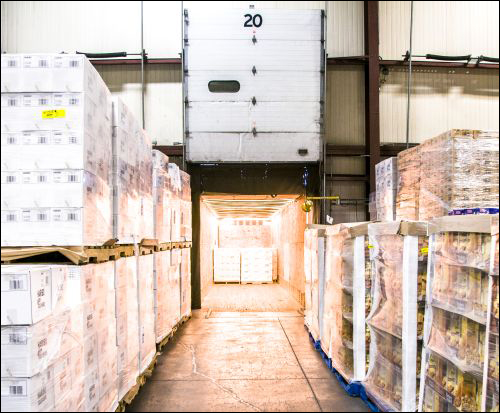
Bob LaMere, ECW’s CIO, says his company was able to reduce the number of its switchers from 10 to seven, while still increasing its overall productivity by 19 percent.
ECW operates its food and beverage logistics services site at the Port of New York/New Jersey, in Elizabeth, N.J. The site covers 60 acres, including 1.5 million square feet of refrigerated space. It also has 14.5 acres dedicated to U.S. Customs inspections, where it lines up loaded containers arriving from foreign countries via ship so that customs officials can inspect them. After containers arrive by sea, drayage truck drivers transport them to ECW’s site, where workers unload the contents—such as boxed goods on pallets or kegs of beverages—and place them in storage within the company’s temperature-controlled warehouses. The emptied containers are then stacked and stored in the yard to be returned to the port terminal by a drayage truck driver.
Managing the complexities of this environment was a difficult task, LaMere says. For the past six years, the company has used its yard-management software to store data regarding which containers were located in which areas, which had gone through customs and which had been unloaded. The system required, however, that warehouse and office personnel manually record data and then input that information into the software, which was a time-consuming process. Typically, he adds, there can be more than 1,100 containers on site, in three different warehouses or at the customs area.
“It worked well functionally” to use the yard-management software, LaMere reports, “unless someone did something they weren’t supposed to.” For instance, he says, if a switcher driver moved a container but forgot to record that event, that container could be difficult to find at a later time. If any containers remained on site longer than the expected duration, ECW might have to pay a per diem fee for that extra time, so the misplacement of any containers could prove costly.
The company considered multiple technology options, LaMere says, but found PINC’s yard-management system to be the best choice. “What I liked about PINC was that it didn’t require antennas all around the facility,” he states. Instead, readers are installed on the company’s switchers, and read data is collected as those vehicles operate around the tagged containers. (Granato declines to name the specific make and model of reader being used on the switchers.)
PINC provided the Omni-ID passive UHF RFID tags that ECW attaches to all containers entering its property. The containers are trucked to ECW’s site after they arrive at the port via ship and are loaded with goods, but then leave ECW empty and may never return. The company mounts a tag to each container via magnets, attaching it to the front bottom right corner of the container. Each tag’s encoded ID number is also associated with a bar-coded ID printed on the driver’s gate pass, and that ID is then inputted into PINC’s Advanced Yard Management System cloud-based software via a bar-code scanner and linked to the container’s identifiers, including the container’s chassis and security seal numbers.
The gate guard assigns an Omni-ID RFID tag to that container by scanning the bar code printed on the tag, attaches the tag to the front bottom right corner of the container, and instructs the driver where to deliver it. In the meantime, the software has a record indicating when the container arrived, so that the system can begin timing how long it takes for that container to complete each subsequent step.
When a switcher moves a container to the customs area or to a dock door, the RFID reader mounted on the truck documents that action by reading the Omni-ID tag temporarily mounted to that container, linking the tag ID with its own GPS location and forwarding that data in real time to the PINC software via a cellular connection. In this way, the system is updated to indicate when the container was unloaded or reached customs, as well as when it left that location. In addition, PINC had installed three portals, each with an Impinj Speedway Revolution reader, which detect when containers pass from one area of the yard to another.
When an empty container is ready to be returned to the port terminal, or when a loaded container is ready to be emptied, a switcher operator will see his work order on the screen connected to his reader. The order not only indicates the action he needs to take regarding a particular container, but also lists that container’s location, thereby enabling him to prioritize his work based on location. The software allows ECW to also prioritize the containers that are nearing the end of their allowable time on the property and, therefore, must soon be returned to the terminal. “That way,” LaMere says, “we can do the oldest ones first and get them back to the terminal” before any additional fees are accrued.
The software displays each tagged container as an icon on a map of the facility. The icons are colored green, yellow or red, according to their status. Red icons indicate that a container has remained in storage for too long, yellow means a deadline is approaching and green signifies that a container is within its schedule.
Approximately three weeks after the system was taken live in summer 2015, ECW began offering a web-based portal for its customers—food and beverage companies—to view for themselves the status of the containers carrying their products. A customer can simply sign into ECW’s yard-management software with a user name and password, and can then view the location and history of every container since its arrival onsite. “We also provide reports that show measurements of time,” LaMere notes, so that customers understand the average time that lapses from one process to the next in relation to their containers.
Since the system was taken live, LaMere says, his company has achieved multiple benefits. “The key benefit was the number of switchers,” he states. When the PINC system went live, the firm required 10 switchers to manage all of the containers it needed to move on any given day, whereas it now requires only seven trucks to complete the same amount of work. That means lower labor costs, less fuel use and a reduced opportunity for accidents. The vehicles also experience decreased wear and tear, LaMere says, since they are moving more efficiently to the closest container for each task, and spend less time searching for containers.
According to LaMere, the GPS data from the switchers also enables management to analyze whether some vehicles are being moved too fast, allowing them to then retrain drivers when necessary. “That improves safety,” he says, “and accidents are reduced.”