On May 2, 2007, RFID Journal presented the first-ever RFID Journal Awards for outstanding achievement in radio frequency identification technology, at RFID Journal LIVE! 2007, our fifth annual conference and exhibition. Hewlett-Packard Brazil was the winner for Best RFID Implementation.
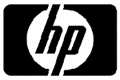
To better track its consumer products, HP launched a pilot project in Brazil in late 2004 using radio frequency identification technologies to tag individual printers and ink-jet cartridges. The company had some experience with RFID—it began tagging cases and pallets of products in 2002, in part to comply with Wal-Mart and U.S. Department of Defense mandates. Overall, it has implemented RFID at some 26 manufacturing sites around the world, including tagging printer boxes at its Memphis, Tenn., facility. But in Brazil, HP decided to take its RFID efforts one step further. The company believed that by tagging each printer from assembly, it could realize benefits not only in supply chain management but also in its manufacturing and distribution processes. In addition, the tags could be used to identify and track products returned to the factory for repairs under warranty.
Since its RFID system went into full production in Brazil in August 2006, HP has tagged more than 2 million items. With the increased visibility into the whereabouts of its products, HP Brazil estimates that it has been able to reduce its printer inventory in the supply chain by 17 percent—and says it is now closer to perfect order fulfillment. HP Brazil is not yet tracking products to any retailers.
Another big benefit of item-level tagging is the insight HP has gained into its operations—from the manufacturing line to the distribution center and warranty repair service, says Kami Saidi, operations director for HP Brazil. By tagging each printer from assembly, HP now knows, for example, how long each printer spends at each station on the assembly line and how long a printer sits in a temporary storage area. The company is analyzing that data so it can remedy any problems—whether in equipment or work processes—that might be slowing down production and distribution.
HP is also using the RFID tags to create a “DNA” for each printer. By saving unique information to each tag—such as testing results, install-by dates for cartridges and product destination—HP can identify and track printers that are returned for repairs under warranty. The company says that having a full record of a printer’s history has improved its repair service and made the return of printers to customers more efficient.
Slow and Steady
HP chose Brazil for the pilot because both manufacturing and distribution operations for the printers are within close proximity, allowing HP to more easily capture and track information than in markets where the operations are spread out. HP outsources the printer assembly to Flextronics, a $15 billion contract manufacturer, and distribution to DHL—and both of those companies have operations in Sao Paolo. Also, the volume of printers assembled in and distributed from Brazil—3 million this year—is large enough to provide a statistically valid model of the impact of RFID on operations, says Marcelo Pandini, manager of RFID and business development at HP Brazil.
To oversee the development and management of the pilot, HP set up an eight-member implementation team, which included a project manager, engineers, technicians and IT staff. An RFID team was also set up with representatives of HP and Flextronics, to coordinate the rollout at the manufacturing facility. In addition, HP’s RFID Core Team—which includes members from various worldwide HP departments, such as research and development, supply chain, consulting, procurement and legal—provided guidance as the project got underway.
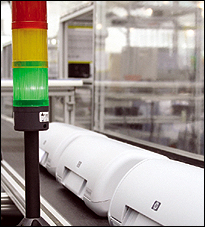
HP created an RFID lab in Sao Paolo for testing different RFID products and system configurations. HP was able to replicate the actual conditions found in the assembly plant and the distribution center, so it could test the RFID tags, interrogators and software in the environment in which they would be used.
The pilot was launched in late 2004 and testing continued the following year. The rollout was methodical and incremental: RFID was introduced at one production line at a time. After each trial’s results were evaluated and the system adjusted, testing would begin on the next step in the manufacturing process. Once all phases of testing were completed and the results analyzed, HP decided it was ready for a full deployment of the RFID system. More than 300 employees at HP, Flextronics and DHL have been trained to use the system.
To date, more than 100 RFID interrogators from Sirit have been installed at Flextronics and DHL. At Flextronics, interrogators are installed at the manufacturing lines, the packing lines, the inventory portals, areas where products are temporarily stored, the in-warranty repair lines and the outbound door. At DHL, there are interrogators at the receiving door, the pallet preparation area and the outbound door.
Initially, Philips EPC Generation 1 UHF tags were deployed, but seeking better performance, HP began migrating to Gen 2 UHF tags last year. With the new tags, which operate at 950 MHz, read rates improved from about 92 percent to 99.5 percent. The tag includes an Electronic Product Code number, the unit’s serial number and part information. The tag has additional memory where the product DNA information is stored. HP uses the information stored on the tags in a variety of ways. At the manufacturing site, the testing results are used to make sure only approved products are sent on to packing. The distribution center uses the destination information to make sure printers get shipped to the right country. And the serial number is used when printers are returned for repairs under warranty.
The RFID applications are built on OATSystems‘ OAT Foundation Suite 5.1, an RFID data management platform that includes middleware. Data from the RFID system is integrated with HP’s enterprise resource planning (ERP) software from SAP and with Flextronics‘ Baan ERP applications. The data that is read from the tags at Flextronics and DHL is written to databases at each company. An automatic query is used to pull data from the databases and transfer it to HP.
The assembly process begins at Flextronics, where an RFID tag is applied to the bottom of the printer’s chassis. Three different interrogators at each production line are responsible for commissioning the EPC tag, recording the manufacturing information on the tag and tracking the printers as they progress down the line. After the assembly is completed, the printers are moved to inventory transition points, or portals, at the manufacturing facility. Interrogators at the three portals track the printers as they are moved in and out of temporary storage areas. In the packing lines, three separate interrogators re-commission the EPC tag (the finished product has a new stock-keeping unit), record packing information on the tag, and track the printer in the packing line. At the outbound portals, tags are read as they leave the factory and the shipping information is sent to the distribution center.
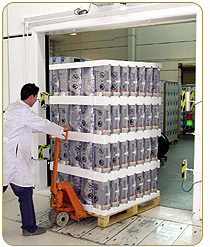
At the DHL distribution site, tags are read as the printers enter the receiving area and again at an area where pallets are prepped for distribution. Finally, an interrogator at the outbound door reads the tagged printers as they exit the site for shipping. In all, some 40,000 tag reads and writes take place every day at the manufacturing site and the distribution center.
With such a complex system, it’s no surprise that a host of technical challenges had to be overcome before the system could be put into production. At the manufacturing site, a high level of electromagnetic noise from sources such as the computers that control the assembly lines interfered with the writing and reading of tags. To address the problem, the HP team simulated the factory’s noise conditions in the RFID lab, and tested different tags and antennas and various configurations of interrogators, tag positions and printer locations inside the carton to get optimal performance.
Another hurdle was that the interrogators were reading two or three tags at a time instead of one because of the close proximity of the printers to each other on the production line. HP did extensive testing of potential setups for the interrogators and antennas to find the best configuration.
To achieve the scale necessary to go from a pilot to full production, HP had the benefit of drawing on the expertise within the company and using its own servers to build the infrastructure to support the system. To handle the ever-growing amount of data collected from the tags, HP has contracted with T3Ci, an RFID analytics and reporting company. T3Ci consolidates and analyzes the data according to HP’s requirements. Throughout the project, HP had to adapt its business processes as the RFID system evolved. For example, at first during assembly, data was being written to tags at different RFID stations on the production line. But over time it became clear that these steps could be consolidated, with the information written to the tag at just one station.
Unexpected Benefits
While HP anticipated supply-chain and inventory management improvements from the RFID investment in Brazil, an unexpected benefit is the level of insight gained into the manufacturing process. “Normally, inventory levels and aging FIFO are things that companies expect to improve after an RFID implementation,” says Saidi, HP’s operations director. But with the printers being tagged at the beginning of the assembly process, HP now has data that shows any steps in the process that are taking longer than they should. “We can see the exact date, time and quantity of products that were impacted,” Saidi says.
With that information, HP can check the production line equipment and the quality of parts being used, and analyze the assembly process and other factors to pinpoint and troubleshoot any problems. So far, the RFID data has shown some variations in the dwell time, or the time it takes for a printer to move from the start of the manufacturing process to the end. The company is now analyzing the possible causes for those variations and will make necessary changes to improve efficiency, says Pandini, HP’s manager of RFID and business development.
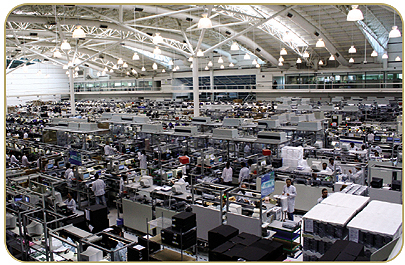
“You can’t measure return on investment in the traditional way,” says Pandini. “You can’t presume a savings, because you don’t know what you don’t know. With RFID, we have learned that we can for sure make our operations much better.”
Looking ahead, HP Brazil is eyeing the expansion of RFID technologies within its supply chain. The company is planning a pilot project under which suppliers would tag cases or pallets of high-value raw materials, such as printer case parts, before delivering them to manufacturing. Being able to track the materials would improve warehouse management and decrease manufacturing downtime, Pandini says. Based on the success of the project in Brazil, HP says that likely markets for expanding the RFID system are its manufacturing operations in Asia and the Americas, but to date no decisions have been made.
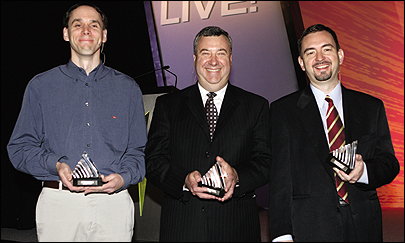
The Other Winners
Read about the other RFID Journal Award winners by clicking the links below:
• DHL for best use of RFID in a service (see A Prescription for Spoiled Drugs)
• Dow AgroSciences for most innovative use of RFID (see Getting the Bugs Out)
Like HP-Brazil’s project, each story is unique, highlighting the many different ways RFID technology can be implemented. Each shows how RFID can be used profitably today, and each will likely inspire end users to deploy RFID in new ways to create real business value.