Jun 01, 2007On May 2, 2007, RFID Journal presented the first-ever RFID Journal Awards for outstanding achievement in radio frequency identification technology, at RFID Journal LIVE! 2007, our fifth annual conference and exhibition. DHL was the winner for Best Use of RFID in a Service.
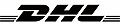
DHL, the express and logistics brand of Deutsche Post World Net (DPWN), saw the problem as a challenge—and an opportunity. It developed an RFID- and sensor-based system to provide pharmaceutical companies with real-time visibility into the temperature status of their shipments. "What is important for this new solution is we can react during the transport process, not just after," says Keith Ulrich, director of DPWN's Technology and Innovation Management Group, which manages all projects of the DHL Innovation Initiative, the DHL Innovation Center near Cologne, Germany, and the group's patents.
Pharmaceutical companies can lose millions of dollars if a pallet of drugs is rendered unsuitable for use because temperatures fluctuated out of bounds. And the number of temperature-sensitive drugs is on the rise, thanks to advances in biotechnology and the trend toward more liquid-based drugs that are particularly susceptible to degradation brought on by temperature change. Experts say roughly one-third of all cold chain shipments are related to the pharmaceutical and biotechnology sectors.
"The other trend affecting the industry is more regulations, especially in the U.S.," says Ulrich. "The U.S. government would like to make sure that the products are from the original producer, and that the products are still working. To have a reliable and controllable new solution, which is also cost efficient [to address all these trends], is very important for the [pharmaceutical] industry."
And for people, adds Ulrich. A medication that hasn't been correctly controlled for temperature through the whole process may be ineffective for the patient who takes it. Worse yet, certain items for which temperature hasn't been controlled or monitored—such as therapeutic proteins used to treat cancer—may even prove dangerous.
DHL's RFID- and sensor-based system tracks the temperature of shipments at various points from departure to arrival and makes that data available to customers in real time over the Web. With access to this information, pharmaceutical companies can, if necessary, recall a shipment and quickly get a replacement underway.
DHL began to develop the Smart Temperature Sensor Project in 2006, when the DHL Innovation Center launched its RFID initiative. Ulrich says pooling the knowledge of its partners and customers is critical for discovering opportunities that have far-reaching benefits to all the parties involved. Partners in DHL's Innovation Initiative include IBM, Intel, Motorola and SAP. Pharmaceutical customers represent a significant portion of DHL's contract logistics practice, and it was due, in part, to their concerns about monitoring the cold chain that the initial focus of the Smart Temperature Sensor Project is on the pharmaceutical industry.
IBM spent three months mapping out the process framework to determine the service's key functional parameters, such as where and when RFID tag readings should occur. The IBM Sensors and Actuators EBO (Emerging Business Opportunities) organization helped to design the architecture of the solution. Currently, DHL has a live implementation of the technology in place with Roche Diagnostics, with which it partnered on the pilot. During the pilot testing, DHL and Roche tried out a number of different products under live conditions and conducted numerous tests in cold rooms to help determine which type of tag to use. The implementation took six months.
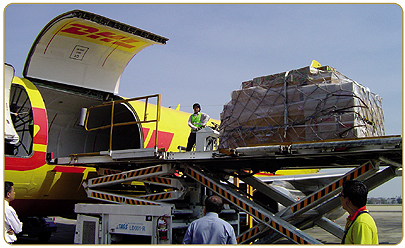
DHL's temperature-monitoring solution, which works in both Styrofoam and insulated containers, uses Freshtime RFID tags provided by Infratab, an RFID company. Each EPC Class 2 UHF tag includes the temperature profile for the specific product; a certain drug may be fine if temperature varies as much as 10 degrees from the recommended temperature, while another may be able to withstand greater or lesser fluctuations. A sensor takes the actual temperature of a drug in dense intervals—every two minutes, for example—depending on customer requirements. At each interval, the temperature is measured against the minimum and maximum temperature ranges for the product.
One of the interesting findings about tag requirements discovered during the testing stage of the process was that the tag and the sensor could not be positioned close together, as was originally planned. Often, aluminum or water-filled boxes are used as internal packaging during transport, and when the tag is close to such materials, the read rates are affected. "So we have split the sensor from the tag," Ulrich says, resulting in a "long" tag design in which the sensor is close to the product and the tag is close to the outside package material. "Now," he says, "you have both very good read rates and very good temperature control."
A typical process works like this for DHL's contract logistics customers: At the pharmaceuticals plant, the customer packs the shipment into an RFID-enabled Styrofoam or insulated box. A DHL employee uses a mobile handheld interrogator to read the RFID tag as the shipment is loaded onto the truck. When the shipment arrives at the airport, DHL reads the tag again. After arrival at the destination airport, DHL reads the tag before the shipment is moved on to the customer depot or to a DHL facility, where it would be read at least one more time before it is transported to a customer warehouse.
DHL employees can view the freshness gauge information transmitted from the tag on their mobile handheld interrogators. DHL and its customers also get real-time information about product freshness via a Web portal, developed in conjunction with IBM. By constantly checking the shipment at various points along the supply chain, decisions can be made about whether any actions need to be taken on a particular shipment.
"The customer can give DHL rules and guidelines for how to react when something happens," says Ulrich. Other customers may prefer to decide what steps to take. For example, they could expedite a shipment once it arrives at their warehouse for delivery to pharmacies or hospitals while it is still usable and safe for patients. "They'll know that it has a freshness of 80 percent after transport because there was a small temperature problem during processing, but that the product is still working," says Ulrich. "Normally, this product may have a shelf life of one year, but now it's only ten months, so the pharmaceutical company can address this."
Sensing Benefits
DHL says one of the benefits Roche has realized is an overall improvement in delivery reliability. Many other DHL logistics customers are requesting the service, Ulrich says. "After a very successful pilot [with Roche] and deployment phase, we are now in the phase to do rollouts and have a concrete product for all our customers," he says. DHL is aiming for this to happen in the second half of the year. The company also says it plans to introduce the service for DHL Express's pharmaceutical customers.
Right now, DHL is deploying the infrastructure to enable its temperature-monitoring solution for shipments in its "main lanes"—that is, its primary transportation routes. The solution may have particular applicability for shipments heading from Europe or the United States to Africa, Latin America or other developing parts of the world where there is less infrastructure to keep items at regulated temperatures. "This new solution," says Ulrich, "makes sure we have temperature control in regions in the world where it's not so easy to have a controlled and reliable cold chain process."
Ulrich says there are some hurdles to bringing the solution to a wider audience. Those include setting up mobile interrogators to cover other transportation lanes and getting the tags in the volumes needed.
For such customers, the added costs of using this solution—which Ulrich declines to specify—won't be an obstacle to taking advantage of the technology in their logistics processes. "What is important for the solution is that the benefit is huge, and existing logger solutions are also cost-intensive," he says. "The cost increases or prices won't be the argument against this solution."
Ulrich doesn't expect to see RFID replacing bar codes in DHL's standard parcel operations anytime soon. "I think for us, RFID is a technology where we think it will have a huge benefit for the industry when it creates more benefits for the customer than the existing bar-code system is doing," he says. "For our parcel network, when you have a good bar-code system in place, RFID will take additional years to have additional benefits when you compare it with the bar-code system."
But where it makes sense, expect DHL to take aggressive steps.
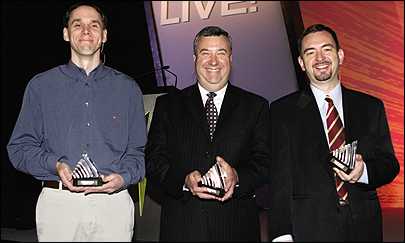
The Other Winners
Read about the other RFID Journal Award winners by clicking the links below:
• Hewlett-Packard Brazil for best RFID implementation (see Keeping Tabs on Printers)
• Dow AgroSciences for most innovative use of RFID (see Getting the Bugs Out)
Like DHL's's project, each story is unique, highlighting the many different ways RFID technology can be implemented. Each shows how RFID can be used profitably today, and each will likely inspire end users to deploy RFID in new ways to create real business value.