Morgan Thermal Ceramics has installed a radio frequency identification solution to meet the needs of a growing thermal-insulation industry at its plant in Pachuca, Mexico. The firm, part of the Morgan Crucible Co., designs, manufactures and installs a variety of thermal-insulation products.
Since the RFID system’s installation, the company reports that it has achieved an increase in inventory accuracy of finished goods, without requiring manual inventory checks, and that it has increased the rate at which trucks are loaded for shipping.
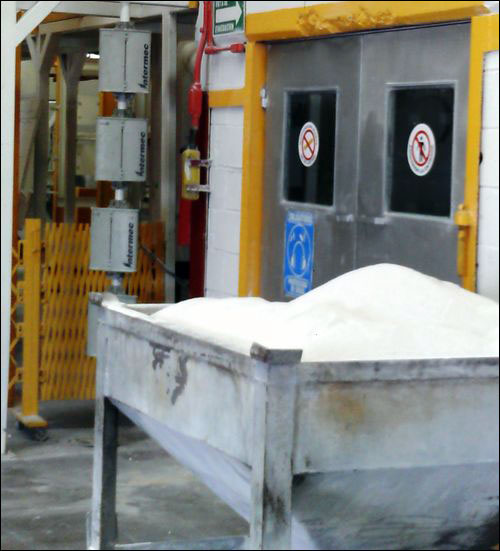
The Pachuca plant, known for producing new products and innovation for the past five years, was thus determined to be the best location to test a real-time location system (RTLS), says Jose Manuel Zavala, the cofounder of Technologia y Consultoria para la Industria (TCI), an enterprise resource planning (ERP) consulting firm that provided the system’s installation, as well as integration, software programming and system monitoring. Zavala served as Morgan Thermal Ceramics’ consulting technical projects advisor. In addition, Mexican RFID firm HTK RFID configured the reader installation, and also provided tags and some software programming.
The thermal-insulation market has been growing as the material is being used in an ever-widening variety of markets, including aircraft, buildings and automotive, to improve energy efficiency and meet safety standards.
As a result of this growth, Zavala says, Morgan Thermal Ceramics provides an increasing number of products in a wider variety of form factors than it did just a few years ago. “Having this demand on new products increased our need for efficiency and customer service,” he states, “and at the end of the day, having more market and customers, we had only two options: replicate (by building an additional facility) or improve efficiency.”
The company sought a solution that would provide the data necessary to track inventory levels of the variety of products being made, Zavala says, as well as ensure on-time delivery to all of its clients—some of whom had critical time constraints of their own. For example, construction products must arrive to a construction site within a set schedule. “Any mistake has an impact on our customer,” he explains. “Shipping wrong product to a construction site could be devastating for a customer relationship.”
To achieve 100 percent on-time capability, Morgan Thermal Ceramics wanted to be able to know which products had been manufactured and which had been shipped, in order to ensure that finished products never ran out, or were stockpiled unnecessarily.
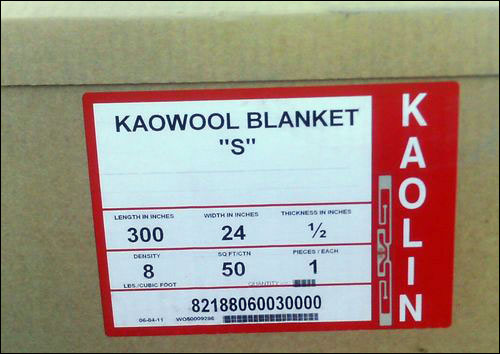
“Before we used RFID, the plant was efficient enough,” Zavala says. However, he notes, many hours of labor were required to ensure that inventory was accurate, and that shipments were completed on time and accurately. For instance, staff members needed to manually walk through the vast facility, then create reports regarding which raw materials had been consumed, and which finished products were awaiting shipment.
Using RFID, Zavala says, would eliminate the need to scan a bar code or read a label visually, and the RFID data could be stored in the company’s software.
Morgan Thermal Ceramics installed Alien Technology fixed readers and Intermec RFID antennas—one reader to track metal containers filled with raw materials being transported to the production area, as well as two fixed interrogators and one handheld to read boxes of finished goods on pallets before they are stored within the warehouse prior to shipping. The company also installed readers on three forklifts, with touch screens to track the storing and loading of products.
After the plant receives raw materials, it issues an internal manufacturing order, based on the inventory stock of finished goods. To fill that order, various minerals are combined within a metal container measuring 2 meters (6.6 feet) in length and width and 1.5 meters (4.9 feet) in depth. A ShortDipole ultrahigh-frequency (UHF) EPC Gen 2 passive tag, made by UPM RFID (now a division of Smartrac), is printed on a Printronix RFID tag printer-encoder, and is then placed on the mix inside the container. Information regarding that product, as well as the mix of materials that will be used to produce it, is then input and stored with the tag’s RFID number in Morgan Thermal’s Oracle JD Edwards ERP back-end management software.
On its way to the production area, the tag is interrogated by a fixed Alien Technology reader. That ID number is then stored in the back-end software, indicating that the mix of materials entered the production process.
Next, the material is removed from the container and placed on one of the factory’s three production lines. (The tag in the container is discarded). At the end of the production line, the finished product is weighed, with the weight indicating the product type—each product type has its own unique weight, based on the material’s density and size. Thus, by weighing a product, the company can record that weight, know which product it is and record its production in the JD Edwards software. An RFID tag is then printed, encoded and placed on the box in which the roll of insulation is packed. “The system now knows I’ve produced this amount for an order,” Zavala explains, and that information is added to an inventory of specific offers available to customers.
Morgan Thermal Ceramics’ employees place boxes on pallets, measuring 2.5 meters by 2.5 meters by 2.5 meters (8.2 feet by 8.2 feet by 8.2 feet) when loaded with 50 cartons. The loaded pallet is shrink-wrapped, and is then moved to the warehouse via forklift truck. Each of three forklift trucks has a Noax Technologies onboard computer terminal equipped with an RFID reader. The interrogator captures the ID numbers encoded to the boxes’ tags and forwards those IDs to the software, which connects each number to a specific product and lists the goods on the Noax screen for the operator. The RFID application also determines the best warehouse location for the product, and instructs the operator where to place the pallet. Once finished with a delivery, the driver presses the touch screen to indicate that the process is complete, and the RFID application and JD Edwards software are updated to show where the product has been stored.
When a customer’s order is received from JD Edwards, the RFID application software sends a list of orders to the forklift operators, including the locations of the products required to fulfill that order. The system determines not only the type of product that should be shipped, but also the age, thereby ensuring that the item manufactured first is shipped first. The driver then retrieves the appropriate items, the forklift reader again captures the tag IDs of the boxes in which those goods are stored, and the software indicates whether the correct products have been selected. The software then updates the status on the JD Edwards software to indicate that the item has been shipped, prompting the issuing of advance shipping notices and invoices, while also updating each item’s inventory count.
The company is currently employing approximately 120,000 tags annually, and reports that it has been able to increase shipment efficiency and accuracy.
“We know the right product—and the right age of product—has been shipped,” Zavala states, since the system instructs drivers regarding which goods should be shipped, and also stores a record of that event. “We don’t need to have supervisors making sure the right products are being loaded,” which he says is time-consuming.
In the future, the company plans to extend its RFID deployment to include the management of packing material used for finished products, as well as for controlling personnel access and monitoring internal assets.