POAGS, Australia’s largest bulk and general stevedoring firm, has turned to radio frequency identification to manage hundreds of heavy vehicles daily at its remote Utah Point Bulk Facility, at the Port Hedland port, in Western Australia.
Utah Point serves the booming mining industry in Western Australia’s Pilbara region, providing shipping services to small and expanding mining companies. The facility readies up to 24 metric tons for shipping per annum—primarily comprising iron ore and manganese—and manages approximately 370 heavy vehicles daily. According to POAGS, a heavy vehicle arrives at its Utah Point site every four-and-a-half minutes, 24 hours a day, seven days a week.
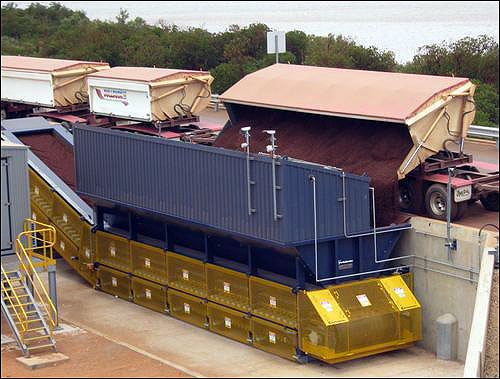
With so many heavy vehicles arriving at, and moving throughout the Utah Point site, says Ray Connell, POAGS’ general manager of information technology, it was vital that the management of their movements be precise, reliable and safe, which is where RFID comes in.
“The high volume of heavy traffic provided a number of significant challenges,” Connell says. “Firstly, we had to ensure the efficient flow of heavy-vehicle traffic to the allocated stockpiles, and ensure availability of loading equipment to avoid delays and queues. Secondly, we he had to ensure accurate tipping of the product to the correct stockpile to prevent contamination. Thirdly, we wanted to automate the operation to safely manage it with acceptable staffing levels and deliver a high level of visibility of all activities.”
With Utah Point handling approximately 127,000 truck movements per year—a figure expected to rise as the facility increases capacity—POAGS set about modeling traffic volumes and throughput based on its projected mine and export targets, in order to develop a traffic-management system. POAGS initially investigated a range of traffic-management and road-tolling systems from a number of intelligent transportation system (ITS) providers, before choosing a solution from RAMP.
“Given the unique characteristics and requirements of the project,” Connell states, “the need to significantly modify and enhance the enterprise ITS, and the tight timetable, we abandoned the ITS approach. We evaluated a number of RFID providers and selected the RAMP RFID solution.”
RAMP deployed Identec Solutions‘ Intelligent Long Range (ILR) technology, including 3,500 i-Q350 active tags, operating at a frequency of 915 MHz. The company installed 20 Identec i-Port M 350 readers, with one interrogator positioned outside the facility for remote early detection, and the remaining 19 located at entry gates (to detect a truck’s arrival and departure), at hoppers for storing minerals prior to shipment and at the tag-return site. The solution also features integrated electronic variable message signboards (VMS) to direct truck movements, along with a purpose-built traffic-management system (TMS) application. The TMS application provides database records for truck deliveries and event management, as well as complex queue management logic to control traffic flow, and integration with the central control system.
The tags are allocated to truck drivers at the mine sites, where the drivers pick up ore for transportation, and are attached to the inside of the windshield using suction cups to enable the vehicles to be tracked en route from the mine site and at the Utah Point Bulk Facility. A truck’s presence is first recorded by the remote early-detection reader, located about 5 kilometers (3.1 miles) from the facility’s entry gates. It is then detected at the gates to Utah Point. As the vehicle moves throughout the Utah Point site, it is identified by the remaining readers. The TMS software uses the RFID data to direct the vehicles, via the signboards, to the appropriate stockpile queue, where the load of ore is then delivered to a hopper.
According to Connell, there were a number of significant challenges inherent in rolling out the system, including the facility’s remote Pilbara location; the harsh, arid environment, in which temperatures can regularly exceed 45 degrees Celsius (113 degrees Fahrenheit); and the variety of stakeholders involved in the project. The Utah Point facility was also still under construction and beginning partial operation when the RFID solution was rolled out. As a result, he says, considerable testing was performed beforehand, including verifying the technology within RAMP’s facilities in Sydney, as well as a number of test-case scenarios to ensure that the RFID hardware was integrating with the complex queue logic, and that the system was delivering exact results. Tests were also conducted to ensure that the solution could accommodate the high traffic volumes before the system was delivered on-site and installed.
“Working around civil, electrical and mechanical construction teams provided various challenges,” Connell reports, “yet we managed to complete the implementation within the project timetable.”
“The traffic-management system provides a high level of vehicle movement visibility to the control-room operators,” Connell states. “It allows control-room operators to track the in-bound vehicles as far as 5 kilometers away from the entrance to Utah Point, then determines the truck’s stockpile destination within the facility, operational state of POAGS’ equipment for unloading the ore, and demand for that stockpile location by heavy vehicles at the truck’s determined time of arrival. Among other benefits, this visibility allows us to effectively manage demand for timeslots [at the stockpile]; monitor unloading equipment at the hopper, status and break-downs of unloading equipment and the hoppers; and keep truck turnaround to a minimum.”
The TMS application is also integrated with the central control system, in order to coordinate the automatic startup and shutdown of POAGS’ unloading equipment with the trucks’ arrival times, and to maintain the efficient running of the equipment. Moreover, the application determines that the correct truck is at the proper stockpile before allowing that vehicle to unload, thereby preventing costly contamination.
POAGS is working closely with it clients and the Port Hedland Port Authority, Connell says, and may consider extending the TMS and RFID capability as the port’s capacity is expanded.