The U.S. Army Logistics Innovation Agency (LIA) is installing more than 6,500 active radio frequency identification tags as part of its Next Generation Wireless Communications (NGWC) program for logistics applications, to track military vehicles and other equipment as they are washed at Camp Arifjan’s Lot 58, in Kuwait.
The tags, provided by Cubic Global Tracking Solutions, employ the IEEE 802.15.4 protocol to form a wireless mesh network. Camp Arifjan—a new, $200 million state-of-the-art facility funded by the Kuwaiti government—will provide permanent support facilities for tens of thousands of American troops stationed in that country, replacing temporary sites in use since the Gulf War. The camp serves as a forward logistics base for the movement of equipment from the entire Southwest Asian theater, including Iraq, to the United States or other deployment locations.
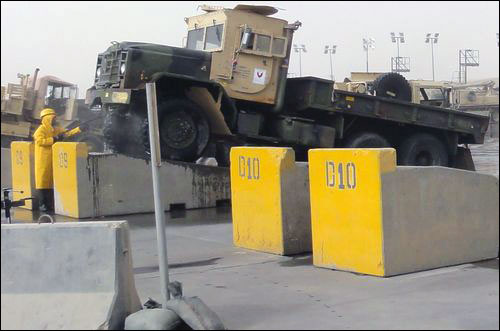
To comply with U.S. Department of Agriculture (USDA) requirements intended to prevent soil-borne insects or other potentially harmful organisms from entering the United States, U.S. military vehicles and equipment must be thoroughly washed before being shipped home. To accomplish this goal, the military utilizes wash racks on which a vehicle is elevated so that it can be entirely cleaned, including its undercarriage. The number of vehicles undergoing Camp Arifjan’s wash-rack process at any given time fluctuates, but averages at approximately 100. As U.S. forces complete their withdrawal from Iraq (slated to take place through the end of this year), the numbers of vehicles—and the speed at which they will need to be processed—is expected to increase significantly. Lot 58’s wash-rack area covers approximately 70 acres, but wash racks are also being set up at three additional remote locations.
Prior to implementing the RFID solution, the military needed to employ contractors to manually record which vehicles were completing which processes, such as cleaning, inspection or maintenance, based on their serial numbers. This manual method provided visibility only into the time at which personnel recorded the ID numbers, says Bill Jarrett, the LIA’s project lead, and that data was ultimately unreliable, resulting in inefficiencies.
To improve the visibility of each piece of equipment, as well as knowledge of its location—and, thus, whether it was cleaned before exiting the country—LIA sought automatic-identification technology (AIT) that it could deploy enterprise-wide, Jarrett says.
Before permanently deploying the Cubic tags, the LIA launched a pilot at Lot 58 in June 2011. For the pilot, 277 tags were deployed to track and monitor class VII equipment—tanks, launchers and other vehicles—in order to prepare, clean and inspect those assets prior to shipment. This initial pilot, and the permanent deployment to follow, is known as the Army Mobility Asset Tracking System (AMATS).
For the AMATS pilot, Jarrett says, the Army Materiel Command (AMC) attached the battery-powered RFID tags—which measure 5.8 inches long, 3 inches wide and 1.3 inches thick—to equipment and supplies coming out of Iraq, in support of the drawdown effort. The tags were affixed using magnetic mounts, and were secured to a variety of vehicle locations via cable loops. Each tag transmits a signal to others within its vicinity, at ranges of up to 400 meters (1,312 feet), though Mary Ann Wagner, Cubic Global Tracking Solutions’ president, says that to ensure 100 percent reads, her firm recommends a mesh network with a maximum between-tag distance of 100 meters (328 feet).
Each tag transmitted its unique ID number, along with the U.S. Department of Defense (DOD) Transportation Control Number (TCN), and that information was passed from tag to tag until being received by a fixed mesh gateway (FMG), provided by Cubic Global Tracking Solutions. Each gateway can manage data culled from thousands of tags, Wagner says, noting, “but we typically install at least two FMGs, for redundancy.” The gateway forwarded tag and location data to the Cubic GTS Device Management Center software, integrated into the DOD’s database behind the agency’s firewall. The software stored tag and location data to indicate which process the piece of equipment had just completed, and provided reports to the DOD.
According to Wagner, Cubic Global Tracking Solutions has been working with the DOD since the company’s combined capabilities—through the acquisition of Impeva Labs’ assets in May 2010 (see RFID News Roundup: Cubic Acquires Assets of Impeva Labs—were merged at the beginning of this year. “We have been on an incredibly fast track since then,” she states. “The Next Generation Wireless Communications effort, in support of the Army’s Logistics Innovation Agency, is a major component of our business.”
In March 2009, Impeva Labs conducted a test for the LIA, with nearly 1,000 mesh asset tags at Moffett Field, operated by NASA’s Ames Research Center, in California (see DOD Completes Large-Scale Tests of Mesh-Networking Tags). Earlier this year, Cubic engineers in San Diego, Calif., conducted a test of 6,500 mesh asset tags destined for Camp Arifjan, creating what they believe was the largest 802.15.4 mesh network ever formed.
The pilot was originally designed to last for six months, and the Army had intended to make a decision following its conclusion regarding whether to adopt the technology. Because of the early documented benefits, the Army opted to permanently deploy the technology immediately, instead of waiting until the pilot’s completion, and to expand to an additional three remote wash-rack sites in Kuwait, in addition to the Lot 58 site.
The NGWC mesh-network capability, Jarrett says, was designed to be a plug-and-play, “soldier-friendly” AIT solution. This means that once a tag is attached, all data is collected automatically without requiring any labor on the part of personnel.
“The NGWC mesh network represents a paradigm shift from conventional RFID (with tags that must pass through a reader portal),” Jarrett says, “and we believe will revolutionize logistics throughout the enterprise.
The installation’s greatest challenges, Wagner says, involved the unreliability of Camp Arifjan’s local power and network infrastructure, which resulted in issues with the fixed mesh gateways and the local servers. This was addressed by configuring the mesh network in such a way that a fixed mesh gateway experiencing connectivity problems could transmit data to another FMG. “The impact on the server was minimized by adding uninterruptible power supplies,” she says, “and optimizing auto-restart functions to minimize down time if the servers experienced power or network issues.
“We also had challenges with rough terrain and the sand storms that occurred during the pilot,” Wagner adds. The rugged terrain, she notes, required the use of some fixed tags to allow the mesh network to reach the outer limits of the storage lots; the hardware, she reports, was not impacted by the sand storms.
“The ability of the mesh network to automatically switch from one FMG to another minimized the impact of an isolated power or base-network failure,” Wagner states, adding that when it came to the arid Middle Eastern environment, “weather and terrain challenges actually presented opportunities for us, because we could showcase the abilities of our yard-management solution under unpredictable conditions in the desert. We were able to demonstrate to the Army that they could maintain visibility of their assets by utilizing our tracking devices—even in a sandstorm, where visibility with the human eye was extremely limited, if not totally impaired.”
Now, Wagner says, as the solution is being permanently deployed at the camp, the LIA is looking into adding sensors—such as those that detect door status (open or closed), and those that measure light, humidity, temperature, motion and acceleration—which could be built into Cubic tags to provide additional information regarding some equipment.
“The real value of the mesh network,” Jarrett indicates, “will be realized when Army/DOD integrates the mesh protocol with sensors to monitor the condition/status of key assets and equipment.”
Since the system was installed, Jarrett says, “AMATS is providing near-real-time visibility of assets enabling yard management.”
Jarrett will discuss the Camp Arifjan deployment at RFID Journal‘s RFID in Defense and Security 2011 conference and exhibition, to be held on Nov. 17, 2011, at the Sheraton National Hotel, in Arlington, Va.