French third-party logistics company SeD Logistiques is using an ultrahigh-frequency (UHF) Gen 2 RFID system from Tagsys at its Paris distribution center to improve the services it provides to its brand-name apparel manufacturers, by moving products faster and with less risk of inaccuracies than its competitors. The solution, which went live two weeks ago, provides the company with the ability to automatically track the receiving, packing and shipping of fashion apparel, and to provide one of SeD’s apparel customers with data regarding its products’ movements through SeD’s DC, thereby enabling the customer’s own inventory management and stock replenishment.
SeD moves a total of 5 million to 10 million garments through its facility annually for approximately five customers; this involves receiving and storing products, and then packing and shipping specific orders for retail stores. One customer, which has asked to remain unnamed, has begun tagging each of its fashion items with an EPC Gen 2 passive RFID tag, and had requested that SeD install an RFID infrastructure to begin reading the tags, as well to automate its receiving and shipping processes. The brand-name apparel company is employing Tagsys’ Fashion Item Tracking System (FiTS) solution at two of its own warehouses—one in the United States, and another in Europe—as well as at 70 retail stores across Europe and United States. In an effort to continue leveraging the RFID system into the supply chain, SeD’s management hoped that if the firm began reading the RFID tags as well, the brand company could then have further inventory data about the amount of product located at the logistics center, and the amount being received and shipped.
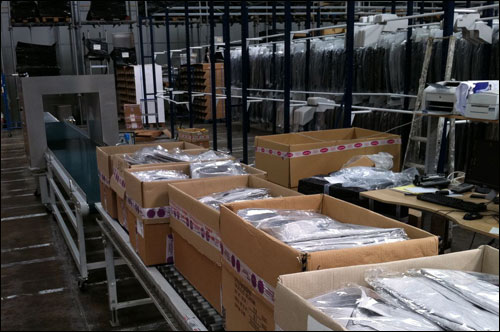
“We were thinking about implementing RFID before [for reception and order preparation process optimization],” says Pascale Barbier, SeD’s sales and special project director, but the customer’s request “was the real trigger.” He adds that the customer requested that SeD utilize Tagsys as its vendor.
Since installing the solution at its Paris facility late last month, SeD has used the system to track which items are received at the warehouse—SeD has a total of 70,000 square meters (753,500 square feet) of space dedicated to all of its fashion logistics operations—as well as what is packed for retailer orders and what is loaded onto trucks destined to those retailers.
Tagsys installed two reader stations using its own hardware—one consisting of a tunnel reader for boxes, another utilizing a reader for hanging apparel. The second station includes a desktop interrogator for reading and verifying tags on items as they are packed in boxes to fulfill a retailer’s order. Tagsys also provided five Toshiba TEC RFID printer-encoders, enabling SeD to begin producing RFID labels with embedded Tagsys AK passive RFID tags for the approximately 200,000 untagged items that the customer already had onsite. The tagging of those items is still underway. By September of this year, the company also expects to be employing a Tagsys HHU-400 handheld reader for inventory tracking, in the event that workers are seeking specific items in the warehouse.
Traditionally, the tracking of items through the facility relied on bar-code labels and scanners. To determine which items are received, packed and shipped, staff members manually scanned the bar code printed on each item’s label. This process was time-consuming, the company reports. With the RFID readers, bar-code scanning is no longer necessary at the receiving, packing or shipping process. Warehouse employees still read bar codes during the picking process, however, as they remove items from shelves to be packed for a particular order.
This summer, the brand-name apparel company began attaching Tagsys AK tags to its products before they are shipped to SeD, according to Didier Mattalia, Tagsys’ sales manager for the company’s apparel division in Europe, the Middle East and Asia. The items arrive either in boxes or on hangers. Once received, the boxes of items are placed in a Tagsys SRU-400 fixed tunnel reader, and the unique ID on each item’s tag is read. Goods on hangers are placed on a conveyor, and then pass the other fixed SRU-400 RFID interrogator located in the receiving station. For either boxed or hanger items, Tagsys’ FITS e-connectware middleware, running on a server at SeD’s warehouse, receives the unique ID data, and forwards that information to SeD’s existing warehouse-management software, which links the ID number with the product’s serial number and description.
When an order is received from a retailer, a member of SeD’s warehouse staff picks the items being ordered, scans their labels’ bar codes with a handheld scanner, and then delivers them to the packing area—known as the preparation station. There, items in quantities of up to 10 are placed on the desktop reader. Both boxed and hanger items are packed in boxes during this step. E-Connectware then displays a list of products based on the RFID reads, via a monitor connected to the reader, and indicates if any item does not correspond with those listed on the retailer’s order. In that way, the warehouse staff can correct any packing errors before a box is closed and sealed for shipping. The data is then sent to the warehouse-management software.
Finally, the boxes are moved to the dock doors, where they pass through the tunnel reader used for receiving. The tags within the boxes are then read one final time, in order to confirm that the correct items are being loaded onto a truck for a specific order, and a monitor at this location displays that information.
At this point, Barbier says, it is still too early to confirm how many labor hours are reduced by using the system. Nonetheless, he indicates that he expects greater efficiency to be achieved, since the items’ bar-coded labels will not need to be manually scanned when received, packed or shipped. He forecasts that the system will also provide increased reliability, by ensuring that a product is not missed at any point along the receiving or shipping process, and that it will enable SeD to provide additional services, such as sharing data regarding the goods’ location and status (that is, whether they were received, packed or shipped).
The brand-name apparel customer currently using the system is already tracking data about the status of items shipped to SeD’s facility directly from e-connectware middleware installed at its facility. Tagsys receives information from both the brand-name and SeD facilities, Mattalia says, and shares status data pertaining to the tagged items in SeD’s warehouse with the brand customer, which pays a fee directly to the RFID technology provider.
SeD hopes that more of its apparel customers will begin tagging its products, thereby enabling them to take advantage of the improved efficiency and visibility offered at SeD’s facility. In the meantime, the firm continues to utilize bar-code scans for tracking products from its other customers.