Würth Oy, the Finnish arm of the Würth Group, a global supplier of assembly and fastening materials, is employing radio frequency identification in the picking process along a 1.5-kilometer-long (0.9-mile-long) line at its plant in Riihimäki. The closed-loop application features 40 stationary readers that interrogate EPC Gen 2 passive ultrahigh-frequency (UHF) tags on roughly 1,000 plastic containers. The information collected via RFID is used to direct the conveyor belt system to send the containers to the proper picking stations.
The system not only saves time by ensuring that the containers are routed to the correct stations, but also lowers labor costs by reducing the number of manual steps in the picking process, according to Antti Känsälä, the business development manager at Vilant Systems, the company that designed the RFID system for Würth Oy.
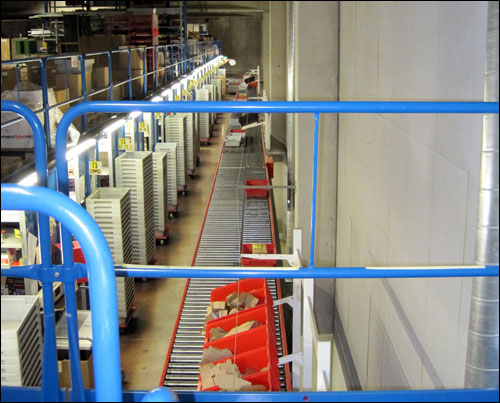
Würth is using Web tags from UPM Raflatac, as well as Astra readers provided by ThingMagic. A single tag is glued onto each container.
Würth had been operating an almost identical system based on low-frequency (LF) tags that it installed 15 years ago. However, the firm could no longer obtain parts for the proprietary system, so it hired Vilant to replace it, and to do so without requiring any downtime on the line. The company operates the picking line in two shifts every weekday, and more than 70 percent of its orders are processed there daily.
With the new UHF system, data to direct the conveyor system is saved on the tag, just as it was with the older LF system. At the beginning of the picking line, the system writes that information to each container’s tag. Readers then interrogate the tag on the container as it moves down the line. When a container approaches one of the 20 picking stations at which it should stop, the system moves that container off the main conveyor and on to an adjacent picking station, where a worker loads it with products, as instructed by a printed picking list. Once finished, the employee slides the container back onto the moving conveyor belt. Each container stops at an average of five to 10 picking stations along the line, in order to be filled with products from the company’s catalog of 30,000 items, such as screws, bolts and protective clothing.
Würth is utilizing a total of 40 readers, installed at various points along one side of the line. However, Känsälä notes, only 20 of those units are mounted near picking stations. The others are mounted at the start and end stations on the line, as well as at other points not associated with a picking station. These readers collect data regarding tags that pass by, so that Würth’s managers can have a real-time overview of each container’s progress along the picking line, and give certain containers priority if necessary.
“Managers can see the route map for each container,” Känsälä states.
According to Känsälä, Würth decided to implement a system in which data for directing the conveyor belt was placed on tags instead of in an external database, because the company was happy with the way the previous system worked and did not want to go through the process of redesigning a new one. In addition, both the old and new systems had to be operational simultaneously during the switchover to the new technology. Finally, Würth wanted the picking stations to operate independent of network connectivity—that is, it did not want to rely on a WLAN or cable connection linked to a back-end system, in case the connection were to fail.
The planning and testing of the system began in September 2009, and the first new readers to be installed became operational in January 2010. Vilant added additional readers, step by step, until the project was finished this month.
For Känsälä, the project’s big challenge was to implement the new RFID system while still operating the old one, so that the picking line would experience no downtime.
“During the ramp-up of the new system, we had to circulate containers tagged with both UHF and LF tags, and we had to replace old readers with the new readers, one by one,” Känsälä explains. “We had to make sure the data on both tags on each container was the same, and make sure the data was passed to the back-end system correctly… Since the systems needed to be interchangeable with each other, many restrictions were created that you don’t have when designing a system from scratch.”
Würth’s managers plan to use the new system to collect better data for quantifying how often each picking station is used, Känsälä says. Such information may help them maximize the use of each station, by eliminating picking bottlenecks.
According to Känsälä, some customization of the software in the readers was necessary so that the information could be used to direct the conveyor belt.
At a later date, Känsälä says, Würth plans to use the RFID system to eliminate all paperwork from the picking process. Currently, a worker looks at the picking list, fulfills the picking order by placing the items in the container at his or her station, and then uses a pen to mark the task as completed on the list. The system that the company envisions would present the employee with an electronic picking list associated with the RFID-tagged container that is guided to the picking station. The list, on a handheld reader, would inform the worker about which shelf to go to for picking.
Känsälä declines to reveal the amount of money Würth invested in the RFID system.