When imported goods are shipped from a seaport to regional hubs throughout the United States via rail, the timing of their arrival can be varied and unpredictable. The inability to accurately plan when products will arrive can cause added expense and delays for Royal Food Import, which imports private-label processed fruits, fish and vegetables packaged in Asia and South America, and supplies them to U.S. retailers.
So when the company began seeking a temperature-monitoring system for its containers in transit—to ensure temperature-sensitive products, such as pouches of peaches and pineapples, maintain a safe temperature threshold—it discovered that a single solution could solve both temperature and scheduling issues. What’s more, the system could also provide container security, and allow customers to gain a real-time view into where their products were located.
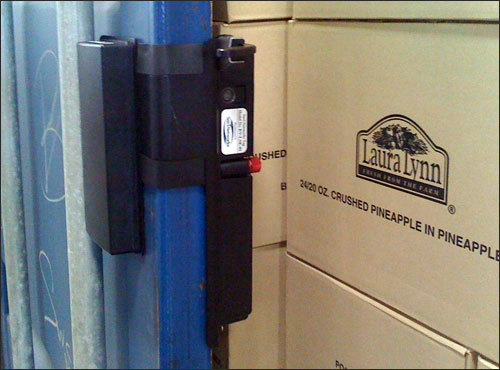
“Initially,” says Collin Tuthill, Royal Food Import’s president, “we were hoping the system would provide the mechanism to monitor temperatures” of temperature-sensitive products during shipment. “But we found there were other benefits,” he adds—namely, a locating system enabling the firm to better understand when and where freight arrives, and the ability to share that information with customers.
The solution, Savi Networks‘ SaviTrak, utilizes cargo container security seals with GPS technology to identify the locations of goods that the company imports. The system capable of monitoring temperatures, and sends location information, security status and sensor data to a Web-based server via a cellular connection.
Royal Food pays for goods when they arrive at a rail yard, immediately prior to taking custody of those products. Paying even one day before it is necessary to do so means funds are prematurely deducted from accounts, and ultimately costs the company money. The firm often pays a day or more before it anticipates a shipment will arrive at the rail yard at which it is unloaded and shipped to a distribution center, in order to ensure the order can be released and then picked up immediately upon arrival at that rail yard, and to avoid paying any demurrage costs as a result of the containers sitting at that site. By providing a locating system that would enable the firm to know its shipments’ locations, payments can thus be made at the appropriate time, not unnecessarily early, or late enough to cause delays. “In the food business,” Tuthill says, “we must be very careful to stay within our margins.”
Royal Food began testing the system on shipments out of Thailand. It tested location, temperature and humidity functionality in 2009, as the containers were being imported by boat to the United States. Having proven to itself, in that test, that the technology works, the company soon plans to start attaching SaviTrak battery-powered LSE container seals to the doors of containers in China and Thailand. The seal slides onto the edge of the container door, says Neil Smith, Savi Networks’ CEO, and has a built-in temperature and humidity sensor to monitor conditions within a container. It comes with a GPRS transponder and a GPS receiver, he adds, as well as a sensor to detect any movement of the seal after it has been locked, such as might occur if someone were to attempt to open the container.
When the seal is first attached, the manufacturer will enter its user name and password into an Internet-based PC to access the SaviTrak software. The plant will then input the container number, as well as the tag’s ID number, which will link that container and tag, and also create an electronic manifest.
Once the seal is locked, it begins transmitting its unique ID number via a cellular connection, to cellular antennas in the vicinity. (The seal can be set to deactivate while at sea and not within range of a cell tower, in order to conserve battery life.) It also sends its longitude and latitude, based on GPS data, as well the temperature and humidity within the container. If the humidity or temperature falls outside the acceptable threshold, or if the seal detects movement that could indicate a security breach, it transmits an alert.
During the test, Tuthill says, the containers sent information from the point of manufacture, where the container was loaded with packaged food, as well as en route to the seaport and at the port itself. Its signal fell outside of cellular range while at sea, but was picked up again upon reaching the U.S. port. At that time, had there been any alerts indicating problems while the container was at sea, Royal Food would have been notified.
Data transmitted by the cargo seals is forwarded to the Savi Networks Web-based server, where it is managed by the SaviTrak control center. Royal Food can then access that information via the Internet, after providing the proper password. The SaviTrak software can also forward alerts to the company’s staff by e-mail or text message.
Royal Food (which pays Savi Networks a monthly fee for the service) also makes this data available to its customers. The system can be set to issue an alert to the food importer, or to its customers, if the container reaches a specified location, thus indicating it will soon arrive at the rail yard, where it needs to be unloaded. At that point, Royal Food can then pay for the shipment and send a truck to pick up the approaching container. For the company’s customers, the benefit is in knowing where their products are, and thus being better able to predict the date and time of their arrival at stores or distribution centers.
“We provide SaviTrak as a full service,” Smith states, meaning that not only does Savi Networks host the Web-based service, it also manages the container seals. When Royal Food removes the seals to unload the containers, it places them in a box provided by Savi Networks and ships them back, so that Savi Networks can later redistribute the seals where needed.
According to Tuthill, the benefits have been threefold. “If you can shave two or three days [per shipment] out of the equation, that can save hundreds of thousands of dollars,” he says. The system also provides safety by sending an alert if the seal has been tampered with. “The safety aspect is extremely important—that’s the driving force for me.” The system can offer customers assurance that no one has tampered with a container while it is in transit, he says, adding that the temperature data is important to perishable products that might be sensitive to extreme heat or cold. “So if there is an extreme temperature discovered on the vessel,” the products can be moved forward to be shipped immediately by rail.
Tuthill says he passes the system’s cost on to those customers who request access to the data, as part of the fee for his company’s service. The increase in cost, he notes, is minor. The food-processing plants that produce Royal Food products will soon begin attaching Savi Networks LSE seals to hundreds of containers, Tuthill says, and the system is expected to go live in late March or early April of this year.