Chemical company BASF is completing the installation of a wireless asset-tracking system to monitor the location and condition of its fleet of railcars containing the company’s six most hazardous chemicals. The VeriWise tracking units, supplied by GE Asset Intelligence—an equipment services division of the General Electric Co.—along with GE’s VeriWise software system, provides BASF with visibility of approximately 1,000 of its 7,000 railcars as they travel from chemical plants to customers throughout North America.
A VeriWise asset-tracking unit contains a GPS receiver, a communications satellite transceiver and a battery (recharged by a set of four solar panels), as well as optional sensors, such as those used for detecting impact and motion, or for measuring temperature. The entire unit measures 2.5 inches by 11 inches by 30 inches, and is bolted to the top of a railcar. Once installed, the device transmits its ID number, its location and any other data at predetermined intervals over a low-orbiting communication satellite, to a VeriWise server hosted by GE. BASF can then access the information via the Internet. According to Steven P. Williams, BASF’s logistics technology manager, VeriWise software running on the server can also send alerts to BASF and authorized users in the event of a specific incident—such as a railcar collision, an unacceptable temperature fluctuation or tampering with a car’s dome (the hatch built into the top of the car, used to access the interior).
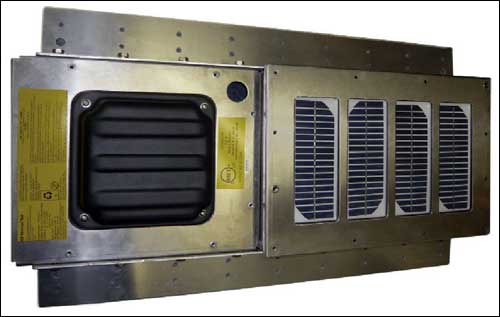
In 2005, says Doug Hoehn, GE Asset Intelligence’s commercial leader, BASF first began working with GE to find an automated solution that would provide greater visibility into railcar movement throughout North America. The chemical company was interested in two things: improved efficiency of fleet management, and greater security based on data regarding the cars’ condition. Security-related information could then be provided to such agencies as the Transportation Security Administration (TSA).
BASF utilizes its fleet of railcars to transport 50 different commodities—some hazardous and some not. The company’s Rail Command Center manages the fleet, and is responsible for tracking the location of every railcar, whether loaded or empty. Until the firm installed the VeriWise system, however, most data came to the command center from the railroad companies that own the tracks on which the railcars travel.
BASF owns some of the railcars it uses, and leases others. In either case, if the company’s employees wanted to know where a particular car was, they needed to contact the railroad operators, which then often had to do their own legwork—such as contacting specific rail yards, and sometimes sending railroad workers out into the yard to look at cars’ serial numbers. If a car spent too much time at a specific location, railroads also charged BASF a demurrage fee, which could be expensive and impossible to verify. “We wanted to develop technology that would provide us with more accurate, timely data [than the existing manual method],” Williams says. “and help us reduce the number of cars in our fleet.”
Moreover, BASF wanted to receive rapid alerts in the case of any incident involving cars loaded with its most hazardous chemicals. For the past three years, BASF and GE have been using and improving on GE’s VeriWise technology, including hardware and software. The initial deployment consisted of 133 tracking units, tested to prove the hardware’s reliability. BASF and GE also developed the server software to provide the type of information BASF needed most. Today, Williams notes, the company uses version number 5 of the hardware, as well as version number 4 of the software.
Some improvements throughout the multiple versions include the most recent tracking units’ ability to both transmit and receive data (thus enabling BASF to communicate directly with the device), and software that allows a variety of access levels for authorized users, such as BASF’s staff and customers. The company has installed VeriWise units on every railcar used to transport its most hazardous chemicals, as well as 90 percent of the cars utilized for the five next most hazardous chemicals. More than 1,000 cars already been equipped to date; BASF’s goal is to equip a total of 1,200 cars.
According to Williams, each tracking unit BASF installs comes with a sensor suite that includes location, impact and motion sensors. The units are set to transmit their location, along with any new impact or motion data, via satellite four times daily. The sensors enable the firm to know where the cars are, whether they have received any impacts (which could result in damage to the car, or a potential hazard related to chemicals stored within that car), when the cars are in motion and when they are still. Each location at which the cars are loaded or emptied—such as BASF’s manufacturing plants and customer locations—is input into the server as a geo-fencing (electronic boundary) location, so that specific information can be sent indicating when the cars arrive at a particular site, and when they depart.
For the more hazardous chemical cars, additional sensors connected to the units provide dome sensors to indicate when the dome might have been opened outside of a geo-fence area. They also come with temperature sensors to track temperature changes within the car. In this way, the company knows when the chemicals’ temperature becomes too high or too low. This data can also be used for business analytics, Williams says, because it provides an indication of the chemical’s specific temperature when it was loaded and unloaded.
Customers require that some of the chemicals be at a specific temperature while being unloaded. Due to this requirement, BASF heats or cools a chemical before it is loaded onto a railcar, in order to achieve that temperature by the time it is delivered. For example, the company may heat a chemical to 110 degrees Fahrenheit to ensure it will be at 75 degrees upon delivery. However, with temperature data, the company can now better determine the rate at which the chemical cools, and thereby adjust the heating process accordingly. That, Williams says, is one potential savings related to this installation.
The company also expects to save money previously spent on the demurrage of cars left too long in a rail yard. By tracking collisions based on impact sensor data, Williams explains, BASF knows when a car may have been damaged, and in whose possession that car was at the time that the accident occurred.
But the system’s safety aspect is also critical to BASF, Williams adds. Beginning next week, the company plans to provide alert data to the TSA in certain incidents, such as a collision or railcar tampering. The system will also send BASF an immediate alert itself when an accident occurs, and include such data as the particular chemical loaded in the car, whether that car is upright or tipped over, and where it is located.
One challenge in the hardware’s development, Hoehn says, involved providing the necessary power, depending on the variety of uses of the sensor units. If units are programmed to beacon more often than four times per day, for instance, they will consume battery power much more quickly. Railcars do not generate their own power, so GE and BASF developed the system to include solar panels connected to the unit’s rechargeable battery. Installing the system has been another challenge, Williams says. Because the railcars generally move across the United States, the company must wait until a car arrives at a location at which trained BASF employees can install the unit and input data about that car, including its serial number and the type of commodity it carries.
Williams is confident that his company will receive multiple financial gains from using the system, based on reduced demurrage costs, improved car deployment and greater visibility into responsibility in the event of a collision. The business analytics will add another benefit, he says, though some of that benefit will be better realized when all cars for the six targeted commodities are fully equipped. Before deciding whether to install the system across the entire fleet of 7,000 railcars, Williams says, the company intends to continue analyzing the financial gains for itself and its customers against the system’s cost.