New Belgium Brewing Co. is using radio frequency identification to track the aluminum-and-steel kegs it utilizes to distribute Fat Tire ale and other beers it produces at its brewery in Fort Collins, Colo. In so doing, the company can track when a particular keg was filled at its facility, shipped to a distributor that delivers it to a bar, restaurant or liquor store, and then returned to the brewery for servicing and refilling.
New Belgium is using software provided by asset-tracking solution provider Fluensee, that links the time and date a keg was filled to other information, such as where the keg went and what condition it was in upon being returned. The company intends to utilize the RFID reads to decrease the man-hours spent tracking the kegs and the product they contain, as well as reduce the need to order additional kegs when inventory levels seem down. In addition, New Belgium plans to track the performance of distributors, bars, restaurants and stores in respect to the kegs’ usage and any damage found on returned kegs.
In 2008, New Belgium Brewing had been working with another tracking-technology provider, TrenStar. When Fluensee acquired that company (see Fluensee Purchases TrenStar), it began developing and deploying the existing system, explains Tim Harvie, Fluensee’s president and CEO. If all goes as planned, he says, the beer company intends to have RFID tags on all of its 100,000 kegs, and to deploy interrogators at distribution centers (DCs), as well as at restaurants and other retail locations. At present, approximately 10,000 kegs are tagged.
Like most beer brewers, New Belgium sends filled beer kegs through multiple DCs before the beverage arrives at retail locations. Once the kegs are empty and a sufficient number have collected to justify a truck pick-up, the empty kegs are sent back to the DCs, and then to New Belgium for servicing and refilling.
Prior to installing this system, says Brendan Beers, New Belgium’s packaging materials purchaser, the company did not track the kegs’ locations. The only data the facility managed in relation to keg inventory, he says, was the quantity of kegs that left and the number that returned. If kegs were stalled at a distribution center, bar or restaurant, New Belgium had little visibility into where they were located, and for how long they had been delayed. What’s more, if specific kegs were returned damaged, it was difficult to determine how that damage had occurred, and in whose hands.
With the Fluensee system, which went live on March 1 of this year, New Belgium has installed an Alien Technology fixed interrogator next to the machine used to apply stretch wrap to a pallet of newly filled kegs. Each aluminum and steel keg has a Confidex EPC Gen 2 passive ultrahigh-frequency (UHF) tag, encased in a plastic housing and mounted in a metal holder welded to its face. In the future, Harvie says, the tags’ plastic housing will be attached directly to kegs via adhesives.
After a pallet is loaded with eight large or 20 small kegs and wrapped in plastic film, it passes through the fixed interrogator portal that reads the unique ID number encoded to each keg tag. Those tag numbers, along with the time and date of the read, are then sent to the Web-based Fluensee AssetTrack software system residing on New Belgium’s back-end server. The staff also prints a bar-coded ID number onto an adhesive label and applies it to the pallet’s exterior. The pallet ID number is married to the AssetTrack data regarding the kegs loaded onto that pallet.
At a later time, when the loaded pallet is shipped, its bar-code label is scanned, and that ID number is then recorded, along with the kegs’ RFID numbers and the time, date and intended destination. In this way, the company retains a record as to which kegs are loaded onto which pallet and, ultimately, where they will be shipped. Other data, including the type of beer with which the keg is filled, is also stored in the system.
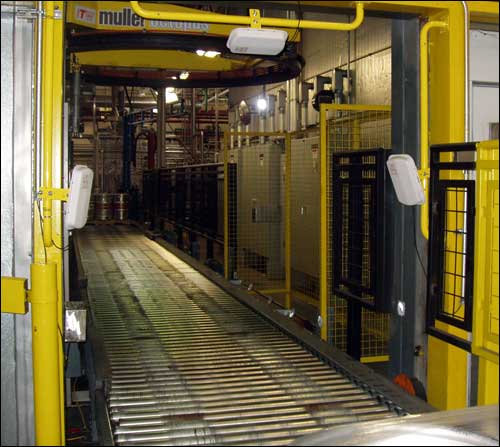
With this information, New Belgium has a better understanding of which types of beer are in demand, as well as how quickly distributors, restaurants, stores and bars return the kegs, and when.
After it tags all of its kegs and installs readers at the DCs, restaurants, bars and stores, the company intends to track each keg’s current location in the supply chain, as well as the length of time the kegs remain at distributors. The system already provides data regarding each keg’s cycle time—the period starting at the moment that keg is filled, and ending when it is later refilled.
“The most important piece of info, initially, is the fill-to-fill cycle time,” Beers states. “We can then calculate keg efficiency [the number of times the keg completes this cycle in a year].” For the average beer manufacturer, kegs turn around approximately four times per year—a number lower than what New Belgium would like to achieve. “We can also gather data on lost kegs [those that have not yet been returned for refilling]. Those two metrics help us make decisions on future keg purchasing.”
Beers calls the initial installation of a fixed RFID reader at its fill line a first step. “It’s a long-term project,” he explains, “but in the end, we hope to improve our keg turn rate or reduce our keg losses. This RFID system will provide the data to show if this is happening.” In either scenario—improved turnaround time or reduced loss—he is confident his company will reduce the quantity of kegs it needs to purchase annually.