Psion Teklogix, a company that makes mobile computers, handhelds and other devices, is utilizing passive ultra-high frequency (UHF) RFID tags to help make sure its products are repaired and returned to customers as promised.
The manufacturer first began employing the tags about two years ago at its service and repair facility in France, to track devices sent in for repair from customers who had signed up for three-day service-level agreements (SLAs). Those who sign up for the service receive RFID tags (the quantity depends upon the particular service agreement) for placement in the boxes used to ship the devices to the manufacturer’s repair center. When a box arrives at the center, the tag’s presence alerts Psion Teklogix technicians that the device within requires a three-day turnaround. Devices lacking RFID tags are repaired less quickly, based on the order in which they are received.
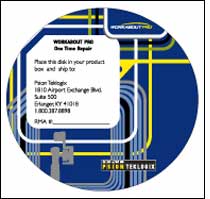
If the manufacturer fails to fix the unit within the three allotted days (excluding shipping time), Psion Teklogix gives the customer another RFID tag that it can use at anytime to have a device repaired or serviced in one day. The company chose to use RFID because the technology allows repair technicians to identify those devices requiring special treatment without having to manually open every box and read the enclosed return materials authorization (RMA) documents before deciding how to route the devices. By using RFID, however, workers open only those boxes prompting an alert; the unopened boxes are opened later, according to the order of arrival, when personnel are ready to service the devices within.
The RFID implementation worked so well, the company says, that Psion Teklogix quickly expanded the technology to its service and repair facilities in Hebron, Ky., and Mississauga, Ontario. Now, the manufacturer is also selling RFID tags individually, or in bundles, so customers can get their mobile PCs repaired in one day.
To use the RFID-enabled service, a customer logs into a secure Web site called Teknet, creates and prints out an RMA form and places the device and the RFID tag—which is embedded in a disk about 3.5 inches in diameter—into a shipping box, according to Dennis Castor, Psion Teklogix’s director of Americas service and support. The disks, which contain an RFID tag compliant with EPC Gen 2 standard, are manufactured by JMD Etiquettes in France and are discarded once the boxes are opened, rather than being sent back to customers for reuse. However, the company notes, as volume of expedited repairs continues to increase, this policy will change.
At the company’s service and repair facilities, all incoming boxes are first placed on a conveyor equipped with an RFID tunnel. Whenever an RFID tag is detected, the conveyor stops and a light stack positioned nearby lights up, alerting technicians that an RFID-tagged shipment has arrived. The RFID tag data is correlated with back-end information about the customer, and that data is presented on a nearby computer, to which the technician has access. The technician checks the customer data, opens the box and labels the device by means of a color-coded sticker designating either a one-day SLA or a three-day (a one-day repair gets a red label, for instance). Then, Castor says, the worker delivers the device to the repair technician responsible for servicing that type of equipment.
When an item is repaired at the Psion Teklogix facility, whether or not it contains an RFID tag, the technicians update the repair status by scanning the unique bar-coded serial number that all Psion Teklogix devices have. The scan is recorded in a back-end database. Thus, customers can log onto Teknet, pull up a page associated with their specific RMA and check where in the process the device is.
“They can see that it was received, and that it is in the repair queue,” Castor explains. When the device is repaired and ready to be returned to the customer, technicians will also update the database with shipping information, including a tracking number that customers can access by logging onto the Web site of the assigned courier. “Customers can track their devices from the point they enter the receiving department, when they hit the repair bench, when the devices go through the repair process, and when they are shipped out,” Castor says.
To date, Psion Teklogix estimates, 6,300 mobile computers are tagged with RFID annually at its North America depot. The company’s use of RFID has been incorporated into an expansion, announced this week, of a service called I-Serv, for its line of rugged mobile computers. The program is designed to provide customers with a single global contract they can tailor by combining different options of I-Serv customer care, such as the one- and three-day guaranteed services that leverage the RFID tag, as well as live support from a help desk and on-site collection of damaged products requiring repair.